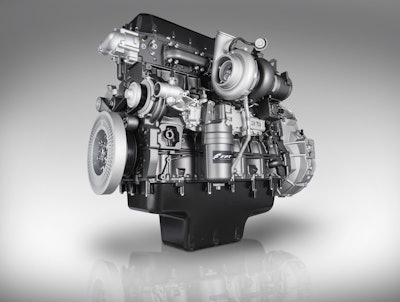
Alongside its patented HI-eSCR aftertreatment technology, FPT Industrial will showcase its smallest and largest engine offering, the R22 and the Cursor 16, at the construction and materials exhibition Intermat, to be held on April 20-25 at Paris-Nord Villepinte, France. The company will be present at Intermat in Hall 5B, Stand L041, with experts on hand to discuss the company’s solutions for the construction market and future perspectives in the powertrain sector.
Making its European debut for construction application, the three-cylinder, 2.2-litre R22 provides a solution for customers seeking a low-maintenance, high-performance engine for applications such as skid-steer loaders and mini-excavators. The compact R22 features single-side servicing and service intervals up to 600 hours. Complying with Tier 4B/Stage IIIB emission regulations via FPT Industrial’s maintenance-free aftertreatment solution, the space-saving unit adopts a combination of diesel oxidation catalyst (DOC) and partial flow filter (PFF), canned in an integrated converter, specifically developed for power outputs below 56 kW.
At the top of its range for construction applications, FPT will also present the six-cylinder, 16-litre Cursor 16 engine. With 18-litre performance in a 13-litre package, and offering optimal power and torque density, performance and service intervals, the engine is specifically suited for large construction and material-handling equipment.
To comply with Tier 4B/Stage IV emissions standards, all engines above 4-litre, including the new Cursor 16, use the patented High-efficiency Selective Catalytic Reduction (HI-eSCR) system. Developed ahead of Euro VI and Tier 4 Final emission regulations implemented in 2014, the patented HI-eSCR after-treatment solution maximizes combustion efficiency in order to reduce particulate matter production and meet legislation. The solution uses clean air rather than exhaust gas recirculation (EGR) before the aftertreatment HI-eSCR converts NOx to diatomic nitrogen and water, and does not need a diesel particulate filter (DPF).
To further support customers with Tier 4B/Stage IV emission regulations, the HI-eSCR aftertreatment system is highly flexible in terms of installation. Resulting from the absence of EGR, FPT Industrial’s solutions do not require OEMs to change the existing cooling packs used in Tier 4A. This saves costs, weight and space and is in direct contrast to Tier 4B solutions adopting EGR. Furthermore, up to 30 different easy-to-install aftertreatment system configurations are available for each power node, providing a variety of off-the-shelf solutions for OEMs.
Tier V Strategy
With the arrival of Stage V, expected in 2019, FPT will not deviate from its long-term SCR-only strategy. Remaining one of the few manufacturers to keep an EGR-free solution, it will instead continue to develop the competitive advantages already achieved with Tier 4B/Stage IV.
By 2019, the new generation of HI-eSCR will see the integration of the particle filter on the SCR, thus fulfilling future Stage V emission requirements. With this solution a part of the SCR catalyst is replaced by the particle filter, thus not creating any significant impact to the after treatment layout, avoiding investments on the vehicle manufacturers’ part, and providing a cost-efficient solution compared to more complex systems.