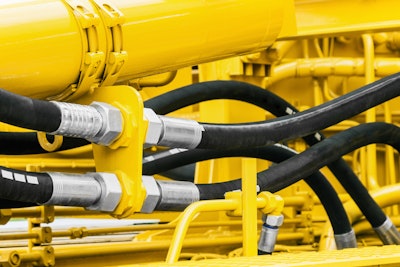
We are always asked, “How long should a hose last?” If I could crystal ball this one, I’d be a very rich person—especially in mining operations, where we have many hose applications based on system pressures and equipment types used in the process. Multiple types of hoses are called for, whether braided or spiral constructions used in surface and underground mining.
Abrasion: The Biggest Killer of Hydraulic Hose
Rubbing or gouging strips the rubber cover, exposing reinforcements. Different types of abrasions exist, for example:
- Rubber against steel frames
- Rubber against ground surface (dragging)
- Rubber against rubber
If the reinforcement is exposed, it may not begin to leak or burst right away. Since the cover is removed, it compromises the construction of the hose performance. Depending on the condition or surroundings of the hose, exposure can make the reinforcement rusty and brittle. It can also continue to remove the exposed reinforcement layer by layer. Additionally, in mining operations, mines can be written up or fined for this condition as it poses a major safety violation.
Today, manufacturers produce many hoses with high-abrasion materials built into the cover. Also, other abrasion-resistant products exist to protect the covers, like flat and round spring guards and fabric abrasion sleeves. Using a better abrasion-type hose or product will help, but rerouting a hose (if possible) to give better protection can be an answer.
Heat and Exposure: The No. 2 Killer of Hydraulic Hose
External heat sources around engine compartments and areas of the country with high outside temperatures cause a hose to age and fail prematurely. Heat exposure can be reduced by using heat-resistant sleeving or, again, rerouting where practical.
Internal system heat temperature will shorten hose life as well. Any rubber-related products in the system, like seals and o-rings, will be affected. Let’s say a hose has a 212° maximum temperature rating which your system runs on the high side of—you begin to cook the hose. To make a hose, it is put into autoclave oven equipment to achieve adhesion of the tube, reinforcement and cover. So high-temperature exposure continues this cooking process. In this case, additional oil coolers may reduce your system temperature, helping system life. Also, check return line sizes to ensure it has not been replaced with a smaller inner diameter (ID) than needed, as this will cause heat issues.
Besides heat exposure, ozone and dust contribute to shortened hose life. These environmental issues cause hoses to dry out, as they pull out plasticizers in the hose’s construction.
iStock
Other conditions affecting hose safety and life fall into different categories:
Hose routing.
Equipment manufacturers engineer the best routing for their specific design criteria. Sometimes rerouting a hose for better life just can’t happen. For example, roof bolters or drills have large bundles of hose that have abrasion issues, but you can’t reroute that configuration to improve life. Anytime you can reroute or protect an assembly where practical, better life can be achieved.
Bend radius.
Bend radius is critical for hose life. Too tight of a bend will cause side loading on couplings, creating leaking issues or failure. Making replacement hoses that look really nice and tight along the framework may cause too tight of a bend radius. If an assembly requires a specific length, replace it with that length unless you’re not sacrificing the bend radius.
Fluid compatibility.
Manufacturers of newer, modern hydraulic equipment use biodegradable, environmentally friendly oils. But the tube stock of many standard hydraulic hoses doesn’t do well with this type of fluid. Fluid compatibility is necessary to ensure the hose’s tube stock is not harmed. Check your oil properties to see what hose tube stock is designed for your needs. Cover blisters and tube swelling are signs of fluid incompatibility on a hose. Another cause of cover blisters is trapped gasses in the system. If you mix old and new equipment in your fleet, using a hose tube stock for biodegradable oils for all applications will eliminate having different hoses to cover all needs.
Hose twist.
When installing a replacement hose in a system, pay attention to hose twist as you tighten the ends to create a seal. Most hoses have printed information, called the lay line, to tell what type of hose you have. If your lay line is twisted or spiraled, you are also doing that to the hose reinforcement, greatly shortening hose life. Place the hose as close to its natural position as possible, tightening one end, then going to the second end—not allowing the hose to twist.
Correct replacement hose assembly fabrication.
When fabricating an assembly, choose the correct replacement hose and fittings to match the original failed assembly for working pressure, ID size and fitting combination. Choosing a hose too small for the application can cause heat and sluggish performance. It’s a good practice to mark insertion lengths on the hose to ensure that couplings are being pushed in all the way into the hose. It’s also wise to measure the final crimp OD (outer diameter) of all hoses made to the manufacturer’s recommended setting. This ensures you’ve made a correct assembly and provides safe working conditions for other personnel.
Tips
- Temperature — Hose should be stored in a cool, dry area, never exceeding 100°F (38°C). If stored below freezing, hose may require warming before handling, testing and placing into service.
- Don’t place in direct sunlight, rain or heaters, or near electrical equipment, humidity or ozone.
- Don’t expose to oil, solvents, corrosive materials or fumes.
- Store hose in the original container if possible. Never stack too high, as its weight can crush hose at the bottom of the stack.
Choosing a method of hose protection will provide better life and reduce costly downtime. Mi Conveyance Solutions provides many solutions in hose and fittings to customers from our world-class manufacturing partners. We also offer on-site safety classes for your specific application needs. Local support is key, and having industry knowledge will ensure that your equipment has less downtime and keeps personnel safe.
Brad Hoback is director of hose fabrication for Motion’s Mi Conveyance Solutions.