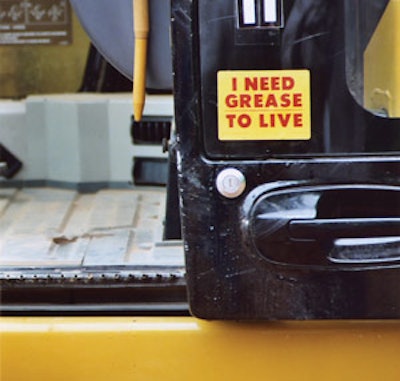
Hydraulic breakout forces that can exceed hundreds of thousands of pounds... Dirty, wet and muddy work environments that are home to damaging contaminants... It's no wonder that articulation joints, pins and bushings can seize and lock up if not given the appropriate care.
To keep moving parts functioning properly for a long and productive life, it's essential to maintain regular greasing intervals using the appropriate grease formulation.
"When you grease a bearing, a universal joint, connecting rod, etc., it's important to re-grease it at the proper intervals to pump out the old grease that is contaminated with water, dirt or even metal from any wear that may have happened during the application," says Walt Silveira, U.S. technical services manager, Shell Lubricants. "Selecting the right grease will help extend service life. It's about reliability and longevity of the equipment to keep it from wearing prematurely."
Thick or thin?
There are several things to consider when selecting a grease. One of the first you will want to evaluate is pumpability.
Greases are classified according to National Lubricating Grease Institute (NLGI) grades, which rate a grease's thickness or fluidity. Essentially, the difference between grades boils down to how much soap, or thickener, is added to the base oil - the higher the grade number, the greater the amount of soap used, and the greater the tendency for the grease to stay put in heavily loaded components.
The most fluid grease, Grade 000, has a consistency similar to molasses or heavy gear oil, while a Grade 6 resembles a bar of soap. The grades used most often in the construction industry fall into the 0 to 2 range.
Grade 0 grease is commonly used in auto lube systems where the grease has to be fluid enough to circulate through several feet of hose. Grade 1 is thicker and can be a good choice for cold climates in winter, because they maintain sufficient pumpability when temperatures plummet. Grade 2 is typically used in the summer in colder climates and in warmer climates year round. It provides a balance between pumpability and clingability.
The type of soap used in a particular grease is also a determining factor in selection. It is essentially a holding agent that traps droplets of oil. When force is applied to the grease, the soap releases the oil to lubricate the metal surfaces. "The thickener acts like a spider's web," says Mark Betner, heavy-duty lubricant manager, Citgo. "It interlaces and locks in the oil until you need it to be released."
Be aware of the type of thickener being used, because they don't all get along. "There's a lot of family fueding between thickening agents," Betner notes. "Lithium greases are like type O blood; they get along with everyone. Other thickeners, such as aluminum complex-type greases, can offer advantages in performance, but they don't like other thickeners.
"If you put two greases that are chemically incompatible with each other, they start to fight, and one of them leaves," he continues. "That's why we tell owners if you're changing brands or types of greases, be aware of the chemical compatibility. You may have to lubricate the fitting more often to remove the old grease as fast as possible."
Which additives do you need?
Once you've selected a grade, it's time to evaluate properties of the base oil - such as viscosity - and additives that can enhance performance for a given application.
Oil viscosity plays a role in determining a grease's load carrying ability and how well it will perform under extreme pressure. Load carrying ability ratings are reported on data sheets as the four-ball weld load and the Timken "OK" load. "The higher the numbers, the greater the load carrying capacity, and the greater the grease's ability to withstand heavy loads without breaking down," says Corey Taylor, grease technology manager, BP Lubricants.
Different components and applications require different viscosities. For example, you don't want to use a heavy base oil to lubricate universal joints, because you want the oil to easily flow in between needle bearings. But in slow-speed/high-load applications, you need a heavier base oil to protect bearings.
Structural, or mechanical, stability of the grease is also important. "As grease in that pivot point or bearing gets worked, you don't want the grease structure to fall apart or slump out of the bearing," says Silveira. "You want it to have as good a consistency as when you first pumped it into the bearing. You want it to maintain its consistency and stay in that application."
Some equipment manufacturers suggest using a grease formulation that contains molybdenum disulfide, commonly called moly grease. This additive takes durability one step further. "Some construction equipment is so powerful, with so much force, that no matter how good we build a grease, it may end being displaced," says Betner. "This additive gives some final plating protection even if the grease gets pushed out, washed out, etc. It stays in place even though the thickener has left. It's called a boundary lubricant."
Other additives available range from corrosion and rust inhibitors to dyes and durability enhancers.
Corrosion and rust inhibitors do exactly as their name implies - protect against corrosion and rust. Greases with these properties are especially beneficial when work environments are extremely wet and/or harsh. Water can break down grease, leaving metal components exposed to the environment; this ultimately leads to rust. The right thickener, coupled with additives, can help fight water washout.
Grease manufacturers also use additives to give grease staying power by building in characteristics such as temperature resistance. "When grease gets hot, it softens," says Taylor. "At some point, the physical structure breaks down. If you choose a grease without enough temperature resistance, it will melt and leak out. So you want to select a grease that provides enough temperature resistance for the application."
Some additives don't necessarily affect grease performance, but they do make managing a lubrication program easier. Dye is one such ingredient. "Color has no affect on performance," says Betner. "It's just used for identity."
"Color has nothing to do with quality," agrees Silveira. "But dyes do serve a purpose. Once the grease is contaminated or if it comes out of the application, you can see it. Also, as you pump the grease in, you can see fresh, new, colored grease come through vs. dirty, contaminated grease. It helps, but it doesn't necessarily directly affect performance."
How much to keep on hand?
Because of the different properties of grease, you could end up with multiple formulations in your shop. However, it's best from a management standpoint to consolidate to two or three.
Yet, it's important not to consolidate too far. "[The risk of ] incompatibility is heightened when you have multiple products in the shop, so some equipment owners may be inclined to use a one-size-fits-all grease," Betner says. "But you may sacrifice staying power and maintenance reliability in critical equipment you want to protect when you try to get by with just one grease."
To determine the appropriate formulations to keep on hand, ask yourself what is your most expensive equipment, and what is the greatest potential expenditure on parts replacement. "Ask what grease selection would give you the best return to protect your costliest investment," Betner advises. "Select for your most expensive machine. Don't always go with the cheapest or with what's easiest."
"Grease is cheap insurance," adds Taylor. "The penalty for not paying attention to it is not cheap when you consider downtime and parts repair. It can be costly to have a failure if you don't pay attention to your lubrication program."
Storage and Handling Tips
Now that you've taken the time to select the right grease, you will want to give it the best chance to perform its job. "When you're working in a dirty environment, good storage and handling practices are critical," says Walt Silveira, Shell Lubricants. "When you contaminate the grease with dirt, water, etc., it will take away from the life of the equipment."
Following are some storage, handling and disposal tips to help you get the most from your grease:
Storage - Grease does have a shelf life, albeit a long one. But over time, it can thicken and age-harden if stored for too long. The oil and thickener can also separate, although slight separation can be common and is harmless.
For optimum life, store grease in a clean, dry environment and avoid exposing it to environmental contamination. If you store drums outside, turn them on their side. When they stand upright, water can collect on the lid, and if it makes its way into the container, it can break down the grease.
"Water attacks the thickener," explains Mark Betner, Citgo. "Some additives can also mix inappropriately with water and form an emulsion, which can cause the grease to lose its protective properties. If you have to store drums outside, take some precautions to protect the product from the elements."
Handling - Service technicians play an integral role in the ability of a grease to perform at its maximum. Take care when handling a grease gun. "If you drop it in the dirt then use it to grease a bearing, you can expose that bearing to contamination," notes Silveira.
Ensure that personnel responsible for applying grease go through some type of basic practical training on proper application.
"You can apply too much grease," indicates Betner. Such over-lubrication is wasteful, has a negative impact on the environment and can potentially damage components. "Excess grease on the outside of a component tends to attract dirt. That dirt can work its way into the fitting over time."
If you manually lubricate pins, bushings, etc., wipe off the grease fitting before applying new product, since dirt clinging to its exterior could be pushed into the fitting.
Technicians should also be able to recognize worn components, since they tend to leak grease faster, and report to maintenance management any parts that are experiencing high wear. "Over time, this can translate into reduced maintenance costs and downtime," says Betner. "For example, if you have a pin and bushing that's worn, your hydraulic system has to work harder. That can cause the fluid to overheat and you can burn more fuel. It's like a chain reaction. Grease can impact on the rest of the equipment."
Disposal tips - Use a licensed disposal company to get rid of any used lubricants, and be sure to abide by all existing environmental rules and regulations.
Buying grease in plastic bladder liners that can be inserted into metal containers can also be beneficial. When the liner is empty, you can remove it and use the metal container for other things, or your lubricant provider can pick it up and reuse it. Have your lubricants provider show you how to properly set up the dispensing apparatus to avoid any dispensing problems.
"When you're finished using the grease, you can also remove the liner and squeeze the excess into the next container," says Betner. "These liners can save you up to 30% of your grease compared to purchasing grease in a drum."