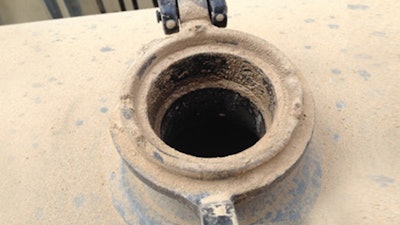
Originally published on Chevron Lube Matters blog
Hold a single hair in your hand or look at the dust that rests on the monitor that you’re reading this article on. Barely visible, right? Now consider this: Those dust particles are roughly four times the size of contaminants that can easily find their way into the oils and hydraulic fluids that protect your engines and equipment. That single strand of hair may be eight or more times larger.
Contamination can be costly in components designed with the extremely tight tolerances needed to ensure effective performance. The smallest amount of contamination, often undetectable to the naked eye, can negatively impact efficiency, service life and even safety.
Follow best practices
Fluid and lubricant storage and handling practices that prevent contamination are essential. Oils and fluids that are stored for maintenance also are susceptible to contamination.
Simple and effective common sense procedures include making sure caps on storage containers are tightened securely, desiccant breathers that absorb moisture and filter out particulate are functioning properly, and fill hose nozzles are not put in contact with dirty surfaces.
These are all vital and important steps to help prevent fluid and lubricant contamination in your operation. However, it also is not uncommon to find that contaminants are introduced in new oils and fluids during production, transfer and distribution processes.
It is important to purchase clean lubricants that meet your equipment manufacturer’s ISO Cleanliness requirements. The International Organization for Standardization (ISO) has developed the cleanliness codes to help determine overall cleanliness, and establish target values to achieve.
Buying the contaminant-free fluids and lubricants that meet your OEM’s ISO cleanliness requirements is considerably easier when your supplier has your back. For example, the Chevron ISOCLEAN program provides lab-tested, certified products of a consistent quality.
However, clean oils and other fluids don’t mean anything, if you are storing them in dirty tanks or allowing contaminants in during transfer. ISOCLEAN also offers a range of expert services, including on-site removal of contaminants from reservoirs and storage tanks using various processes and techniques, system flushing for both new installations and routine maintenance, reservoir and tank cleaning by technicians trained and certified in confined-space entry, evaluation of bulk storage facilities and product handling processes, and sampling and monitoring, along with trend analysis and corrective action planning.
When it comes to lubricant and fluid contamination, what you can’t see can cause the greatest amount of damage. Knowing the obvious sources of oil and fluid contamination is a sure way to safeguard against the costly equipment problems it may cause.
It can cost 10 times more to remove virtually invisible contaminants from fluids and lubricants than to keep them out in the first place. Comparatively, that’s an investment that will pay for itself ten times over in lower repair and replacement costs, and less downtime.
With over 35 years in the oil and gas industry, Dan Holdmeyer has worked for Chevron the past 14 years, serving in a variety of capacities with the company in addition to his current post as Industrial and Coolants Brand Manager where he works as a lubrication engineer that supports Chevron Delo and other related lubricants brands. He plays an integral role in supporting and managing a variety of programs related to off-highway and on-highway lubrication needs. Dan also works as Chevron’s Training Specialist for their Global Lubricants division since joining the company. Prior to joining Chevron, Dan worked as a Field Engineer at Mobil Oil Corporation for 20 years (1979-99) after graduating from the University of Missouri-Columbia with a Bachelor of Science in Chemical Engineering.