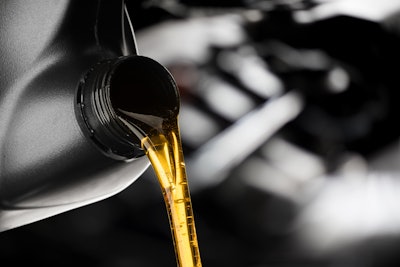
Often, the particles we don’t see are the ones that affect us most. For instance, we can’t see bacteria or germs but those can easily get into our body and make us sick. Something similar occurs with our equipment and the lubricants which are used to help them work more efficiently. SKF notes that contamination and ineffective lubrication are responsible for 51% of bearing, coupling, chain and other machine component failures in equipment.
Logically, if we control the amount of contamination, we can control the number of failures and all the resulting consequences, such as unscheduled downtime and rush expenses (for called out or specialized labor and parts). In this column, we explore how contamination can impact the performance of your equipment, ways to combat contamination and some examples.
What Is Contamination?
Contamination is anything that is foreign to the environment. For machinery lubricants, these are usually classified in three main groups: Gases, liquids and solids. When speaking about gases, this can be air or other gases (such as ammonia or methane) that encounter the lubricant. For liquids, this includes water, fuel or any other liquid that can enter the lubricant, particularly other lubricants or liquids that can be added knowingly or unknowingly. Lastly, solids can mean dirt (from outside the process), metals (from inside the machine) or any other solid particle in the lubricant.
Gases
Gases are the most unsuspected forms of contamination since many people believe that a gas will not affect the lubricant or by extension the machine. However, if air gets trapped in a closed loop system, this can lead to foaming (if the oil makes its way to the surface) or to microdieseling if it remains entrained in the oil.
With foaming, this typically occurs in gearboxes or equipment that are subjected to high churn rates of oil. Foam can settle at the top of the oil and cause the lubricant to not form a full film to separate the contacting surfaces. As such, this can lead to wear of the equipment.
On the other hand, microdieseling or the entrainment of air in the system can also prove to be dangerous because the trapped air bubbles can give rise to temperatures in excess of 1,000°C if they move between different pressure zones. This will lead to oil degradation, often producing some coke or tar insoluble as final deposits. Additionally, this trapped air/gas can also advance to cavitation inside the equipment.
Additionally, if the gas trapped is not air but a catalyst to a chemical reaction, this can incite further or more rapid degradation of the oil making it no longer able to protect the equipment. Therefore, identifying the presence of unwanted gases in your lube oil systems or preventing their entry in the first place is important.
Liquids
Liquids are trickier than gases because they somehow seem to enter the lubricant more easily or get mixed in unknowingly. When a liquid enters a lubricant, it can directly impact the viscosity of the lubricant, either increasing it or decreasing it. In either of these cases, this can be detrimental to the equipment.
If the lubricant’s viscosity increases above the essential value, then the machine will demand more energy to execute its required functions. This will directly impact its efficiency and energy consumption. On the other hand, if the lubricant’s viscosity decreases outside of the essential value, then the lubricant may not be able to adequately protect the contacting surfaces. Therefore, this increases the amount of wear that may occur on the inside of the machine.
Typically, water and fuel are the most common culprits of liquid contamination. These can easily get into your lubricants through poor storage and handling practices. Water can increase the viscosity of your lubricant and cause some additives to drop out of it, reducing its level of protection. Fuel will decrease the viscosity and possibly add to the fire risk of the system. Both can severely damage your equipment.
Another common culprit is the mixing of different types of oil. On an average day, things are busy, and people can get confused and pick up the wrong oil to perform a top up on a system. If we add gear oil or hydraulic oil to an engine oil system, we can have a catastrophe! These oils would have different viscosities, and their additive packages (or even base oils) may not be compatible. This can cause the equipment to stop working, leading to unplanned downtime and then exorbitant resources to get the machine operating again.
Solids
Solids can easily get into our equipment either from the outside or the inside. If there are openings to allow solids to enter then they will. However, sometimes solids enter our lubrication systems without us knowing. This can happen through poor storage and handling practices.
Once solids enter the system, they can:
- Increase the viscosity of the oil
- Increase the amount of wear occurring inside the equipment
- Act as a catalyst (depending on their nature)
- Block smaller clearances causing unwanted downtime in the equipment
Typically, solids are usually dirt, which can enter from outside the equipment. However, these hard particles can cause some metal to be damaged on the inside the equipment which can then lead to the metal being a catalyst for another degradation mode.
Some solids are formed inside the equipment as deposits. These deposits can occur if another contaminant (liquid, gas or another solid) enters the system and reacts with the oil to produce them. As such, these deposits may clog injectors, other valves or tight clearances causing the equipment to malfunction.
How Do We Prevent Contamination?
Contamination exists all around us, but we must prevent its intrusion into our lubrication systems to help keep our machines alive for a longer period. Some simple steps can be performed to help reduce levels of contamination. Also, lab tests can identify the presence of contaminants.
Storage & Handling
Unfortunately, this is the area in which many of the contaminants enter the lubricant. There is no discrimination in this area because all solids, liquids and gases can easily contaminate the lubricant.
Some best practices to follow are to first ensure that all lubricants are properly labeled and that everyone on the team knows the different uses for each lubricant. While this may seem simple, some people think that “oil is oil,” and any oil can work. Educating them on the differences and their effects of being mixed is critical to ensuring that they don’t get mixed up (or used as a contaminant to another lubricant).
Typically, with construction equipment, a lot of smaller sumps do not require a full pail of oil or may require an odd volume of oil. This often means that new unused oil either remains in the original packaging or is transferred to a holding container. If the new oil remains in the original packaging the user should ensure that the packaging remains sealed after use; is airtight (not to allow any other particles in); and stored in a cool, dry place.
If it is decanted into another container, this container needs to be:
- Clean (not previously used for another oil, not “cleaned” using fuel or some other substance)
- Properly capped (to prevent any contaminants from entering)
- Kept in a cool, dry place
Filtration
While this may seem trivial, lots of users assume that their new lubricants meet the required cleanliness standards for their machines. This is not true. New lubricants can be dirty and should be filtered before use. The filtration specification will vary depending on the cleanliness required for your machine.
For instance, the cleanliness specification for a hydraulic machine will be different from that of the engine oil specifications because hydraulics have closer clearances. Although many machines contain system filters which will also catch some of the contaminants, it is always a best practice to filter all lubricants before placing them in your system.
Oil Analysis
Oil analysis is not a likely method to prevent contamination, but it can inform end users of the presence of contaminants. Because of this benefit, it should be used to monitor the level of contaminants in a lubricant and trend their increase or decrease over time. This can spot whether a leak in the system, if a correlation between wear and contaminants exists or an anomaly is present in the system.
The tests that should be used to identify the presence of contaminants include:
- Viscosity (to determine if there is change in this value)
- Fourier transform infrared spectroscopy
- Elemental (to identify wear metals, additives and contaminants)
- Karl Fischer or crackle for the presence of water or fuel
Elemental analysis can easily help identify the presence of wear metals or contaminants, but it can also identify the presence of additives that are not representative of the oil in use. This is a good way of identifying the presence of an incorrect lubricant or solution that may have been used during a top up for that component.
Example
A mixed fleet operator began noticing that the jobs allocated to the excavation crew were taking twice as long as usual, and the costs associated with those jobs for materials also increased. He decided to tag along with the site manager for one of these projects to understand the escalation of the hours and costs.
At the site, the project began smoothly and ran as it should for the first two weeks. Afterwards, he noticed that the equipment began experiencing some downtime on the site. Typically, this occurred on the day after the site maintenance crew carried out their lubricant top ups.
The lubricants were being stored in the elements close to a makeshift shed that held some other necessary tools. The maintenance crew did not have smaller containers to decant the oils for the hydraulic equipment, so they used their disposed soda bottles to “help.” Any lubricant that remained in the bottle was left open to the atmosphere, and then this was topped up by the new lubricant.
Unknowingly, these users were contaminating their oil before placing it in the machines. This led to the unplanned downtime and extra resources, such as more oil, filters and hours for the mechanic. Immediately, proper storage and decanting containers were purchased. The onsite staff was trained in using these containers, which were also color coded to avoid the mixing of different lubricants.
The allocated time for these jobs returned to normal. In addition, the costs associated with the materials decreased because they no longer had to purchase extra oil to make those oil changes when the equipment shutdown.
Contamination can have a significant impact on the downtime of your equipment but can be easily prevented by using proper storage and handling techniques and monitoring the presence/absence of particles through oil analysis.
References
SKF, (June 6, 2024). Solutions for Contamination. Retrieved from SKF: https://www.skf.com/group/industries/mining-mineral-processing-cement/insights/solutions-for-contamination.