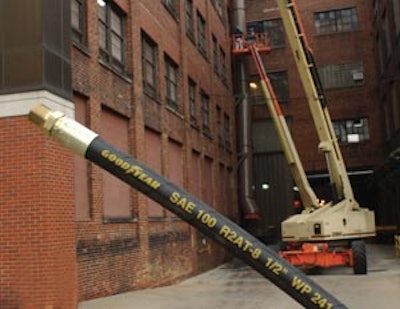
Suppliers offer hundreds of different types and styles of hydraulic hoses, and thousands of different couplings and fittings to choose from. So when it comes time to replace a hydraulic hose assembly, how do you know which hoses and thread ends are the right ones?
"There are some pitfalls and some issues that can come up if you don't understand hydraulics," says Mike Watts, marketing manager for hydraulics at Goodyear. "Hydraulics have become progressively more complicated. Pressures are getting higher, and dimensionally hoses are getting smaller so they can be routed into increasingly tighter spaces. Plus, there is more and more equipment being imported from overseas. Those specs are a little different so there isn't always a direct conversion."
Your best bet is to consult with a specialist — either a distributor or regional applications expert — from the hydraulic hose manufacturer. Many manufacturers also offer training courses to which you may want to send a select group of employees.
"Hydraulics is high pressure, and high pressure can injure people," notes Dave Douglass, product marketing manager for hydraulic hoses at Gates Corp. "It's important to get training so you understand hydraulic systems."
Get STAMPED
Following the STAMPED principal can help guide you through the selection process.
S = Hose size: This is the inside diameter of the hose. The correct size will keep pressure loss to a minimum and avoid hose damage during heat generation or excessive turbulence.
Size information will be printed on the layline of the original hose. If it is painted over or worn off, cut the original hose to determine the inside diameter. Also double-check to ensure it is, in fact, the right size for the application. If the old hose was a replacement, it may not have been sized correctly, which may be the reason it's failing this time. Regardless, it's important to use the manufacturer's recommendations when changing out a hose assembly to ensure optimal performance and prevent voiding any warranties.
Cut the new hose to the correct length. If it's too long, it can lead to extra bends, which can shorten hose life by creating more places for abrasions. And the unnecessary length simply costs more. If it's too short, you can damage the reinforcement and integrity of how the assembly is crimped together.
T = Temperature: Consider both fluid and ambient temperatures. Excessively hot or cold temperatures can crack covers and tubes and damage reinforcements.
Hoses are designed for temperatures from -40 to 300° F, with special hoses available for as low as -65° F. Choose one that can withstand the minimum and maximum temperature experienced by the system. Also consider where you route the hoses. If the route takes you past hot manifolds, a heat shield may be required.
A = Application: Determine where and how the replacement hose will be used. Most often, a duplicate will suffice, but reevaluate hose size according to application to ensure it is the correct size. If the inside diameter is too small, the increased velocity can create friction, which will wear out the inside of the tube more quickly. If it's too large, it will increase the amount of heat in the system, and take up more space than needed. It will be bulky to route and will likely exceed its bend radius, creating turbulence that can make it harder to keep the system cool.
M = Material to be conveyed: There are many different types and styles of hydraulic fluid available. Hose selection must be compatible with the fluid. The fluid's viscosity level can affect the performance and lifespan of the assembly. For example, low-viscosity oils may have very small molecules that can pass through the tube but become trapped between the tube and cover, creating problems. "You just need to be aware of the type of fluid you are using and the permeation rate of the hose," says Dennis Kemper, OEM applications engineer at Gates.
P = Pressure: Be sure to account for any spikes the system may incur. Published working pressures must be equal to or greater than the system pressure. Never try to exceed the 4:1 safety factor because doing so will shorten hose life.
E = Ends or fittings: A general rule of thumb is to connect a hose with the least amount of connections possible. Refer to the manufacturer's catalog or consult a specialist to determine the correct fittings. Several manufacturers, including Goodyear and Gates, offer software programs to help guide you through the hose/coupling selection process.
D = Delivery (volume and velocity): If the same inside diameter of the original hose is used, you can assume the system is properly sized to efficiently transport the fluid. However, if you have a new system, or if you have altered the old one, you will need a new hose size. Consult the hose manufacturer's catalog for recommended flow rates.
Safety tips
Safety is of utmost concern when it comes to hydraulic systems, including when selecting, maintaining and replacing hoses.
"Those hydraulic hoses are going to a cylinder that distributes power," says Watts. "If a hose fails when someone is using a bucket on a loader, the cylinder can make the bucket close or it can dump its contents unexpectedly. If it's a high-lift application, safety is of greater concern."
With that in mind, these experts outline the following tips for minimizing hydraulic hose failures:
1. Utilize one source, one system. Purchase all parts — hoses, couplings and crimpers — from the same company. "As manufacturers, we make our hoses with some differences that make them incompatible with someone else's coupling," notes Douglass. "It is a very dangerous practice to mix and match hoses and couplings from different manufacturers."
2. Learn to identify potential hazards. Look for cracks and abrasions in the cover. "The cover protects the reinforcements (wire or fabric) from weather and environmental hazards such as rocks," says Kemper. "If the wire or fabric is exposed, water and debris can adversely affect the reinforcement by either rusting the wire or, in the case of fabric, allowing water to wick into the system and get behind the coupling where it can cause damage."
Also check to see if the hose is twisted. Look for any seepage in the area of the coupling or on the hose and any bubbling on the cover.
In extremely abrasive situations or in areas where you simply can't get away from abrasion points, consider hoses with special coverings, such as Gates XtraTuff and MegaTuff hose covers, which can offer from 25 to 300 times the abrasion-resistance of a standard hose. Goodyear also offers its Armorcoat hose coverings for these situations.
Be aware that if you utilize nylon sleeves for abrasion resistance, you can still see abrasion beneath the cover and, in some cases, the sleeve may actually cause the abrasion.
3. Keep good maintenance records. "The best predictability of life is maintenance records," says Watts. Goodyear offers a software system that can track hose replacement to provide data on when to replace hoses when no cracks, abrasions, etc., exist.
4. Develop and adhere to a preventive maintenance schedule. Inspect the hydraulic assembly on a regular basis based on the application. Hoses used on a boom arm, in a rough environment with a lot of dirt and sand and/or in a sunny area should be checked frequently. If you see a hose starting to crack, replace it before it fails in the field. "Downtime on the jobsite is much more costly than maintenance time in the shop," says Watts. "Make those inspections an integral part of your routine."
5. Install the assembly correctly. Keep the assembly capped until you're ready to use it. When installing fittings, crimp them correctly for the diameter of the hoses.
If an elbow is used, be aware of the orientation for attaching it to the equipment. If there is a swivel on one end, don't twist it during installation. Consult a specialist to determine the best routing. "Installing it according to its original route may not be the best way to reinstall it," says Watts. Reinstall all the brackets to ensure adequate support.
"Above all, follow the manufacturer's recommendations," he continues. "You can't be too careful with hydraulics. Pressures are so high in today's equipment. Even a pin-sized hole can cause problems. There are a lot of ramifications for not doing it correctly and there are a lot of resources available for learning how to do it right."