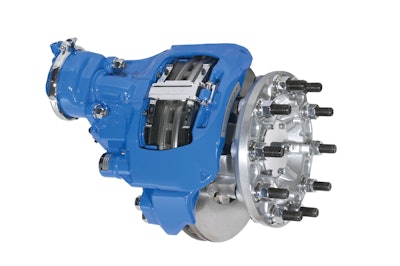
On August 1, 2011 a new air brake standard for three-axle tractors with Gross Vehicle Weight Ratings (GVWRs) up to 59,600 lbs. took effect. This rule applies to tractors invoiced after August 1, 2011. It will not impact any tractors you had in your fleet before that date. But the regulation covers the vast majority of new tractors in use today.
The rule calls for a 30% reduction in the stopping distance from 60 mph versus the previous standards. This means these tractors must stop in less than 250 ft. from 60 mph when loaded to their GVWR and 235 ft. when lightly loaded. On August 1, 2013 heavier specialty tractors and lighter two-axle tractors will have to meet the standard. For a small number of very heavy severe service tractors, the requirement will be 310 ft. under these same conditions.
This regulation was not a surprise, it was finalized by the National Highway Traffic Administration (NHTSA) in March 2007. OEMs have been working with suppliers to develop solutions, which include wider and more capable reduced stopping distance (RSD) drum brakes and air disc brakes.
This regulation is intended to increase the safety on public highways by reducing the disparity in braking between automobiles and tractor/trailer combinations. “Due to the nature of an on-highway tractor, 80,000-lb. GCWs, this regulation makes sense,” says Bernie LaBastide, Navistar chief engineer, brake systems. “It’s not clear at this point that the legislation would reduce collision or fatalities for straight trucks. Straight truck environments are primarily city routes using slower speeds, etc.”
While straight trucks are exempt from the rule, there will be an impact as manufacturers take advantage of the new braking technologies. For example, Peterbilt announced it will make front-axle air disc brakes standard across its entire Class 8 truck & tractor line. For customers who prefer the RSD drum brakes, there is that option as well.
Expect to see some of the higher performance brakes to start showing up on the vocational straight trucks. “It only makes sense to use economies of scale by using the new and improved materials where applicable,” says Curtis Dorwart, Mack Trucks, Inc. vocational marketing product manager.
“My motto is, ‘what is good for a tractor is certainly good for a truck,’” says LaBastide. “We currently offer not only bigger drum brakes but disc brake options for straight trucks as well. The benefit of larger drum brakes are more lining material and some reduced operating temperature due to the larger drum lining interface. Most linings react positively (reduced lining wear rate) with the reduced temperatures.”
LaBastide adds, “While not as popular as steer axle only tractors, we do offer and sell all-wheel disc brakes on some straight truck models. Straight truck rear suspensions pose a distinct challenge to allow decent packaging for the air disc brakes, thus, there is limited availability of air disc brakes on our straight trucks.
But straight trucks can continue using the same brake configuration. “The previous brake lining material is still available for vehicles not affected by the new regulations,” says J. Allan Haggai, Daimler Trucks North America.
The solutions
To meet the decreased standards manufacturers have two options, RSD drum brakes or air disc brakes. Both solutions are relatively transparent to the driver. “It was our desire to design brakes that were more capable and that would not send any specific signals to the drivers,” says Tom Runels, engineering manager for foundation drum brakes at Bendix Spicer Foundation Brake (BSFB). “They can drive away and get no sense that there is anything significantly different underneath their vehicle. These brakes are much more capable and in an emergency they will be able to use that capability.”
The regulations required more than merely making the brakes larger. “To address the new braking standard Mack made component changes to its standard drum brakes so they are more robust and generate more brake torque,” says Dorwart. “We’ve also introduced new friction materials on steer axles and some drive axles.”
However, larger drum brakes will be used by most manufacturers to meet the new standard. “On a typical Class 8 6x4 tractor, we have met the new standard by upgrading from type 20 to type 24 brake chamber, linings and drums with greater width and diameter and larger brake mounting fasteners,” says J. Allan Haggi, Daimler Trucks North America. “The brake lining formulas have also been changed.” These larger drum brakes will add an estimated 90 lbs. to a 6x4 tractor.
Navistar is also offering drum brakes as standard equipment. “Currently, air disc brakes are optional on International branded highway tractors,” says LaBastide. “Our standard brakes are air S-cam type brakes and we offer as an option Bendix air disc brakes. To comply with the new stopping distance regulation, we now offer a larger S-cam brake.”
Navistar selected larger front drum brakes (16.5”x5”) with a different lining material specificially designed for the new regulation, in conjunction with larger service brake chambers (Type 24). “New lining materials were also applied to the rear to balance out the front brakes,” says LaBastide. “As another option the customer can order larger rear brakes as well (16.5”x8.62”) over the standard 16.5”x7” rear brakes. The larger front and rear brakes will increase miles between reline by increasing the usable lining volume and reducing the brake temperatures by increasing the braking area surface.”
There will be an added weight penalty for increasing the brake size to meet the legislation, but it's relatively minor compared to the cost penalty for air disc brakes for example. However, a small percentage of weight sensitive customers will pay for the added cost to avoid the weight penalty. “The larger rear drum brakes will net you an additional 60 lbs. on a tandem rear tractor,” says LaBastide. “This is moving from the 7 in. brake to the 8.62 in. wider brake with the same diameter.”
Despite having been around for the last century, drum brakes have really evolved from a technical and performance standpoint. “They are significantly different than they were 10 to 15 years ago,” says Gary Ganaway, director of drum brakes, marketing and global development, Bendix Spicer Foundation Brake. “They are much more capable. Be that as it may, there are still some fundamental differences that favor air disc brakes. The way that we position them in our product line is the drum brake is very economical. It is a basic product which allows the fleet and the OEM to meet all of the requirements. The disc brake adds an added level of performance and feel.”
The cost difference for an air disc brake can be substantial. “Traditionally, air disc brakes have been priced as a premium to the s-cam brake,” says LaBastide. “There is also a maintenance cost improvement for disc brakes over s-cam brakes relative to time and change out.”
Despite the initial cost difference, some costumers value the benefits offered by air disc brakes. “We see a growing appetite for air disc brakes and expect customers to continue migrating toward that spec in the future,” notes Mack's Dorwart. “Air brakes can provide an increase in service life over drum brakes in the same application, which can make for a positive return to offset the initial price increase for the disc brakes. But be mindful that the duty cycle, vehicle weight, etc. will have a bearing on the life cycle performance. With the wide array of applications, disc brakes are better suited for some operations than others.”
At Waste Expo in May 2011 Mack launched its initial offering of air disc brakes, engineered specifically for vocational applications. “The balance between friction material and rotor material has been optimized for the stop-and-go needs of the refuse industry, providing improved stopping distance and handling,” says Dorwart. “The air disc brakes are easier to service and the friction materials have been designed to last twice as long as the material in S-cam drum brakes.”
Maintenance is one of the key benefits. “An example from a maintenance standpoint, the time it takes to change air disc brake pads once the wheels are off are only about one fourth the time it is for a drum brake,” says Ganaway. “The other advantage is that the disc brake is sealed for life. It doesn’t require any periodic lubrications where most drum brakes you are still required to do that.”
LaBastide adds, “Air disc brakes have a substantially higher initial cost, but are easier to maintain, assuming you are only doing maintenance, like pads changes. Most air disc brake calipers are sealed and non-serviceable, so if the caliper internals fail, you need to replace the complete caliper assembly. So far the latest generation of air disc brakes has performed very well.”
The increased cost of the air disc brakes must be factored into the life-cycle cost. “When you factor in the added acquisition cost to the disc and you total that against increased service times and overall maintenance costs, the longer the over holds the vehicle, the more favorable the disc brake solution becomes,” notes Ganaway.
The weight difference between air disc brake and drum brakes is almost insignificant. “This can vary depending upon the equipment, but they are a few pounds lighter to weight neutral compared to drum brakes,” says Dorwart.
Haggai claims the air disc brake system performs well but may not be the best option compared to a properly spec’d drum setup for vocational customers. “In most applications the vocational user may not realize a measurable return on the additional cost of the disc system.”
The air brake system is versatile, but you do need to consider your application. “Air disc brakes can virtually be used in any application, including the construction vocation,” says LaBastide. “One air disc brake manufacturer utilizes one brake for all applications and utilizes different rotors. Another manufacturer utilizes different brakes sizes and lining material and customizes those attributes to each application.”
On muddy jobsites and working around wet concrete there are some precautions that need to be taken with an air disc brake. “You have to use caution when using air disc brakes in these environments by hosing down the wheel ends,” says Ganaway. “The air disc brake is a robust product, but it is not a maintenance-free product. Those types of application environments just enhance the need to ensure some components don’t have dirt ingress or concrete ingress.”
The challenge comes from load transfer during braking. As the tractor decelerates load is transferred toward the front axle. As a result, the front steer axle brakes became a primary focus. This is where the increased performance of an air disc brake can have the greatest impact. “You get your biggest bang for the buck putting it on the front axle,” says Ganaway.
The reduced stopping distance applies to the as-built new. “It doesn’t apply to the vehicle once it is out on the road and it gets to its first brake job,” says Ganaway. “Technically, someone could find what we call an inferior brake lining or brake shoe.”
“One of the misconceptions that we run across is that aftermarket parts are held to some level of performance criteria,” says Ganaway. “That is really not the case. The new law only applies to new vehicles invoiced after August 1. After those vehicles are in service, it is really up to the fleet to reline with what they see fit.”
But to benefit from the increased safety factor these brake provide you need to use an OE equivalent brake material when you reline. “My concern is if you put an inferior aftermarket lining on a vehicle the driver may not be aware of it initially because drivers brake by feel,” says Runels.
He adds, “The driver may only make an 8-, 10- or 12-psi apply with the new RSD brakes. The driver might be making a 15- , 18- or 20-psi apply with the inferior lining. The driver would not really be aware of it. The driver is just going to press as hard as needed to make the stop. But the driver would become acutely aware that the brakes were inferior if a panic stop was required because those inferior linings would not reach the torque level the new RSD brakes generate. And they will not sustain them even if they do reach it. That’s where your stopping distance would suddenly become very long.”
Benefits outweigh costs
The RSD brakes are going to add a little cost and weight up front, but increased braking performance and service life may offset any potential drawbacks. “In an industry that watches cost and weight very closely, this regulation may have some impact,” says Haggai. “However, increased braking performance and lining life may provide dividends in the long run.”
The first phase of these regulations should have minimal impact on the industry. “I don’t expect much impact on the purchase plans of fleets,” says LaBastide. “The cost pentalties have been minimal except with the optional air disc brakes, which again is optional for Phase I of the regulations. Phase II is a different story though. I expect to see more air disc brakes and even six-channel ABS being required on those units in the Phase II categories.”