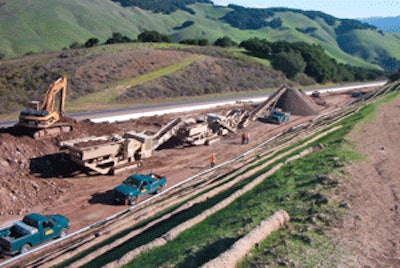
Highway 1 in Central California is famous for some of the most beautiful coastline and rural driving in the world. From Santa Barbara to Lompoc, this state-designated Scenic Highway offers dramatic views of rocky headlands and the Pacific Ocean, which gradually give way to rural winelands and rolling hills as the road nears Lompoc — known as the “Flower Capital of the World.”
California Department of Transportation (Caltrans) criteria for designation of Scenic Highways, first established by State Legislature in 1963, include rules for minimum intrusions or impact from construction and development. And while there are no special restrictions in place for construction or maintenance activities on Scenic Highways, it goes without saying that a conscientious contractor would work to protect the scenic designation of the corridor during construction or repairs to the maximum extent feasible during the project.
When Caltrans awarded Granite Construction the contract to repair a 1.5-mile stretch of Scenic Highway 1 south of Lompoc, CA in early 2004, the company looked at all feasible options for replacing the existing pavement.
“We had a choice of either removing the existing underlay and hauling it off, or crushing it onsite,” says Jason Thompson, Granite’s Santa Barbara plants manager. “We determined we could save a considerable amount on trucking if we made the base onsite by crushing with a portable system.”
In addition, by crushing the recycled asphalt pavement onsite, the visual impact of Scenic Highway 1 would also be far less compromised than if trucks were used to haul material to and from the project.
Granite Construction decided this job would provide an excellent chance for the company to test a system of Fast Trax track-mounted crushing and screening plants it had recently purchased — including an FT 2650 track-mounted jaw plant and an FT 4250 track-mounted horizontal shaft impact crusher plant (HSI), manufactured by Kolberg-Pioneer (KPI), an Astec company, as well as a track-mounted PEP PDF 2618VM screen, manufactured by Astec Mobile Screens (AMS). The Caltrans Highway 1 project began around Thanksgiving in November 2004.
For this project, Granite had to handle one mile of lane removal by milling the asphalt into a long, narrow stockpile, 20 feet from the live traffic. To handle the project in the most efficient manner, Granite set up the equipment in a “train” configuration onsite, with the FT 2650, the FT 4250 and the PEP screen working behind a K-rail barrier.
“With the crushing equipment right on site, it was easy for us to remove the material and feed it directly to the crusher without having to re-handle it,” says Thompson. “The track-mounted equipment was able to follow the rubble windrow, and deposit Class II base in the needed section. With the aid of our new track-mounted plants, we were able to create 20,000 tons of Class II base for the project with very little traffic impact.”
“There really was no better way to crush the material on site. The footprint was too small to crush the material without track-mounted equipment that could ‘walk’ along the stockpile and crush base as we milled material,” says Bradly Estes, branch division plants engineer for Granite Construction.
Ron Brajkovich, plants equipment coordinator for Granite Construction, agrees. “If you look at the alternative — hauling material in and out of the jobsite — the costs would have been prohibitive,” he says. “With trucking costs around five cents per ton per mile each way, and the nearest location we could have hoped to find for crushing was at least 10 miles from the project site, it would have cost a dollar per ton round trip to haul the material offsite for crushing. And that’s a minimum. The terrain in that area has rolling hills; it would have been difficult for us to find a suitable parcel of land within a Caltrans right-of-way to actually do the offsite crushing.”
Estes and Brajkovich agree that onsite crushing with mobile track-mounted equipment saved Granite Construction a minimum of $20,000 for the Caltrans project. And they also say there are few track-mounted plants available that could have handled the parameters presented by this particular project.
“When you’re looking at mobile plants onsite, and looking at using an excavator or front end loader to feed the primary, most track-mounts on the market today can’t operate in a closed circuit on the operator’s level,” Brajkovich explains. “With most track-mounted plants, you have to build feed pads or ramps and work the plants at different elevations, or use separate conveyors.”
Brajkovich says the KPI and AMS equipment provided Granite with the best possible solution, explaining that the three Astec plants could work together in a highly mobile circuit, with sufficient conveyor lengths to feed each plant on one level. By not having to build feed pads, and not having to bring extra conveyors onsite, Granite also saved time, which translates to cost savings.
Brajkovich says he also liked the fact that the KPI and AMS equipment came from a single, American source, which would provide Granite with good parts and service support. “We wanted to work with just one company,” he adds.
Prior to purchasing the KPI and AMS plants, Granite Construction’s Santa Barbara division had relied on an existing portable crushing and screening system that consisted of a jaw crusher, a cone and a three-deck 6 x 20 screen. All three plants were wheel-mounted plants.
Portable plants on wheels can be pulled onto a site and set up, but they are not especially mobile within a site because of setup and teardown factors, including the need for cribbing timbers for leveling and auxiliary equipment such as cranes or tractors to move the equipment.
According to Estes, the existing portable plants were about 15 years old. “It took time, effort and money to move those older plants,” he says. “And we have some recycle locations where it didn’t make sense to move them in and crush. So when we had a project lined up where we could use the older plant in one location for two to three years, we began to look at new portable plants to use at our various recycle crushing sites, as well as on projects such as this Caltrans project.”
Estes and Brajkovich chose track-mounted equipment because of its portability on a low-boy trailer, combined with its mobility onsite. Estes says where Granite’s wheel-mounted plants took up to two weeks to move, the track-mounted plants can be set up and crushing in a matter of hours.
In the year that the KPI and AMS track-mounted system has been in service for Granite Construction, it has crushed at four separate locations. After the Caltrans Highway 1 contract was finished, Granite Construction began to use the FT 2650, FT 4250 and PEP screen at its recycle yard located near Santa Barbara, Bakersfield and Ukiah, CA. The company continues to crush asphalt and concrete for Class II base with the equipment. And Estes is looking forward to projects which will require up to 10 moves a year.
“We have some crushing operations with annual productions of only 10,000 to 20,000 tons,” he says. “Before, it was only feasible to crush at those locations every couple years. And at stationary facilities, it might also be cost-effective to crush 20,000 tons of a 50,000-ton stockpile, then move and come back later to finish the job. This system is perfect to move in, crush and move out. It gives us a steadier market in all of these locations.”
“The track-mounted equipment was definitely easier to move,” Thompson says. “These machines are well-suited for our needs. All together, a move with this system encompasses four separate pieces, including one feed loader or excavator. This is a reduction of five moves from our older plant. We are set up and running within a day, where our other portable plant could take up to two weeks to move in and set up.”
The company also chose to use a jaw/impactor setup in its new plants, versus a jaw/cone setup with its older portable plants, because of feed issues — an HSI can accept larger, slabbier feed material — and the improvement in reduction ratios that are possible with a horizontal shaft impact crusher are better suited for running recycle. In addition, the company could split the equipment apart and use the FT 2650 jaw on one project, with the FT 4250 HSI on another.
“You can’t do that as easily with a cone — it has to run with a primary,” Estes notes. “And with recycle, you can have problems with material building up under the head of a cone. We just felt that with an HSI we could get the production we wanted without the chance of a major failure and without the headaches associated with running a cone in recycle.”
Another benefit with the track-mounted plants is their acceptance for statewide permitting, Thompson says. The California Air Resources Board allows producers and contractors to obtain statewide operating permits for each piece of portable equipment, so that the company can move the equipment and begin to crush material without the need for an individual permit in each air district where the equipment works.
“With this statewide permit, we’re allowed to move the equipment and crush, as long as we don’t have the equipment in one spot for more than 12 months at a time,” Thompson explains.
Estes says that KPI and PEP engineers worked with Granite engineers to design plant customizations unique to Granite’s present and future needs. For instance, Granite-selected options included water spray dust suppression and low-emission diesel engines to meet rigorous California requirements for dust, noise and emissions control.
With the wet suppression system, the hoses travel on the plants and are able to interconnect all three plants. All transfer points and conveyors are enclosed on the three plants. Granite also added aftermarket exhaust to further ensure the company exceeded California OSHA standards for noise and dust control.
“Particulate regulations are getting more and more strict every year,” Brajkovich says. “In addition, regulations can be placed on a local and a county level. Many air districts already require the best available control technology. So in anticipating compliance with future regulations, we wanted to make sure that these plants already exceeded existing regulations, and KPI and AMS were willing to work with us on these customizations.”
Granite Construction says it is getting production capacities of 150 to 300 tph through the plant, depending on feed material.
“The nature of the feed pile always affects the plant’s capacity,” Estes says. “Well-managed feed material means higher capacity.”
Estes, Brajkovich and Thompson admit the new equipment required some training for operators and service personnel.
“We had a bit of a learning curve initially, working with the track-mounted plants versus the other plants we had used previously,” says Thompson. “The plants are more compact, and denser than wheel-mounted plants, so we had to learn the best way to maintain them. Also, we had to learn to use the hydraulic-driven motors, where we had used electric before. But overall, the mobility is a great concept, and these plants are well suited for the jobs we’ve asked them to do so far.”