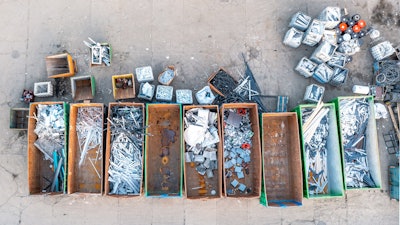
The building and construction sector is undergoing a transformation driven by a global effort to bring emissions to net zero. As this is rightly a priority and to ensure that this becomes a reality, governments together with the United Nations have set global targets to reduce emissions by 45 percent by 2030 and reach net zero by 2050.
To achieve the carbon neutrality required by net zero – ensuring that carbon dioxide emitted into the atmosphere and how much is removed from it by a company or individual or in balance – will ultimately require implementing solutions that are carbon negative, meaning, we have to remove more carbon dioxide from the atmosphere than we emit.
Achieving these goals has led to new regulations designed to reduce the emissions footprint within the building and construction industry. In California, for instance, starting July 1, 2024, buildings that are larger than 100,000 square feet must follow one of three paths to lower their carbon footprint. The Performance path is to have a whole building lifecycle assessment (WBLCA) demonstrating 10% lower embodied carbon emission than a baseline project design. By Jan. 1, 2026, the threshold will drop to buildings larger than 50,000 square feet. California has set targets of 48% carbon emission reductions by 2030, which is higher than the statuary mandate, and carbon neutrality by 2045 in the building sector.
The State of Play in Construction
While regulation is designed to move the industry in the right direction, contractors, architects, suppliers and other industry stakeholders need immediate solutions to ensure the sector achieves the needed emissions reductions.
Currently, the emissions associated with building structures, substructure, and enclosures account for 11% of global GHG emissions. These all fall under the category of Embodied Greenhouse Gas Emissions, or Embodied Carbon – that is, the emissions “released during the lifecycle of building materials, including extraction, manufacturing, transport, construction, and disposal.”
To mitigate, Architecture 2030, a non-profit formed to transform the built environment, issued the 2030 Challenge for Embodied Carbon with targets aimed at the global architecture and building community. These include immediately reach a maximum global warming potential (GWP) of 40% below today’s industry average for embodied carbon emissions from all buildings, infrastructure, and associated materials, followed by 45% or better in 2025, 65% or better in 2030 and Zero GWP by 2040.
To achieve the carbon neutrality required by net zero – ensuring that carbon dioxide emitted into the atmosphere and how much is removed from it by a company or individual or in balance – will ultimately require implementing solutions that are carbon negative.@Sansert - adobe.stock.com
Moving the needle on emissions and meeting these ambitious goals will require the industry to move sharply away from fossil-fuel based materials.
Fossil Fuel-Derived Materials in the Construction Industry
The construction industry consumes 20 percent of all plastics and 70 percent of all polyvinyl chloride (PVC) products that are produced globally each year. Plastics are used in a vast range of building components, such as siding, trim, decking, railing, seals, windows and doors, roofing, internal and external finishes, panels, pipes, guttering, cables, floor coverings, supporting structures, and insulation.
To meet targets, many players in the industry are using energy efficient, lower carbon footprint materials such as recycled plastics, which boasts these benefits over virgin resin. Wherever feasible, waste that was traditionally landfill bound has been diverted to other areas including re‑use, recycling and recovery. The building and construction sector has also made efforts to recycle unused materials and use post-industrial recycled materials to limit the negative effects that the opposite and outdated practices have on the environment. However, the reverse logistics required to return unused materials counteracts many of the gains made by recycling.
Carbon Negativity is the Only Negativity We Should Live With
Implementing greener alternatives to reduce a building’s carbon footprint is progress, but in some cases recycled plastics are more expensive than virgin plastic derived from crude oil. Equally, durable plastics like PVC are popular but recycled PVC is not carbon negative.
Architects have a significant role to play as the designers of commercial building projects. In creating specifications, architects are looking for materials that will reduce the emissions footprint of projects; to even bid for materials on many projects, suppliers will need to come up with solutions that hit reduced carbon requirements, while also delivering on performance.
Biobased materials may offer a solution, but not all biobased materials are created equal. First-generation feedstock options for biobased materials were made from carbohydrate-rich food crops like corn, wheat and sugarcane. However, these have been critiqued for diverting food from human and animal consumption, which can contribute to food scarcity issues globally. Moreover, growing these crops requires significant land and water resources.
Second-generation feedstocks have not faired much better. These comes from agricultural waste which requires additional processing to extract fermentable sugars, but concerns exist regarding the impact of edible oils on food resources and deforestation in this context.
Third-Generation Feedstock is Showing Promise
If these first two iterations of feedstock have cause for concern, the third generation is showing genuine promise in answering the question of how to ensure that the materials used in building and construction are carbon negative while also not having an unintended negative consequence.
Waste has emerged as the third-generation feedstock option. Through energy and resource efficient conversion of waste into a novel material that functions like a thermoplastic, the building and construction industry can reduce its use of fossil fuel-based plastics with a circular, carbon negative material. By converting the entire waste stream, including organics, into a new and safe material, waste as a feedstock fills the gaps of today’s limited recycling infrastructures, while diverting waste away from landfills and incineration.
The Future of Building and Construction is Green
The building and construction industry desires and is being required to become more sustainable by incorporating sustainable and circular practices. It has made a great start and is moving in the right direction. Now, it’s about implementing available solutions that can quickly help the industry achieve net zero targets by 2050.
Industry stakeholders, from architects to contractors and materials suppliers for the industry can now begin implementing waste-based materials into a wide variety of building applications as an alternative to today’s extensive use of fossil fuel-derived plastics. In doing so, they win simultaneously on multiple sustainability targets: reducing waste, emissions and reliance on fossil fuels.
Practically, this means pivoting as an industry on scale to using third-generation biobased materials made from waste that can hold up to both environmental and performance standards. This can be part of a new class of solutions that support emissions reductions targets that we must reach as an industry.