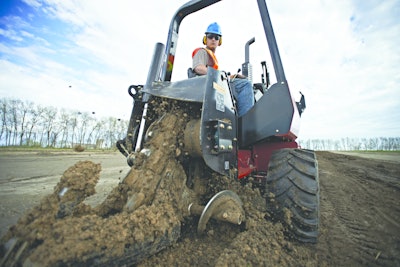
Ride-on trencher tractors have evolved rapidly with new options and features that add versatility while yielding increased productivity and greatly reducing the workload on the operator. Some of these features have been enabled by electronic advancements.
According to Jon Kuyers, senior global product manager for underground, Vermeer, electric over hydraulic controls have been one of the greatest advancements over the past 10 years. These controls simplify operation, and allow advanced features that automate tasks. “You have less complexity in the operator’s station,” he says. “All of our tractors now have electric over hydraulic controls.”
This allows engine horsepower, ground drive speed and attachment drive speed to be optimized. When the load increases or decreases due to changing soil conditions, the tractor will slow down or speed up to maintain the optimum engine speed.
The ability to match ground speed to soil conditions results in major productivity gains. “The productivity increase can be measured in orders of magnitude,” says John Welch, chief engineer, Tesmec. The load control feature can also be useful when obstacles are encountered. “If the trencher hits an immovable obstacle, it stops moving and can bring the digging attachment to a halt. If the object is a moveable obstacle, it slows down or halts momentarily and continues to dig.”
The Ditch Witch organization refers to its technology as cruise control. “It can improve performance by maintaining the ideal load on the machine’s engine despite changing soil conditions on a variety of jobs,” says Steve Seabolt, product manager, heavy duty trenchers. “Most tractors in the Ditch Witch product line come standard with cruise control, which enables the tractor to automatically adjust ground speed to match the changing soil conditions, maximizing productivity. These adjustments allow the operator to focus on other important tasks.”
Many ride-on trenchers also allow the operator to control how much of the engine’s power is dedicated to the ground drive vs. the attachment. “By making this feature adjustable, the operator is able to maximize the productivity of the digging implement for specific ground conditions,” explains Joshua Beddow, marketing manager, The Toro Company.
Electronically controlled pumps allow you to fine tune the amount of power going to your ground drive. “In a lot of cases, you don’t want a lot of power going to the ground drive circuit,” says Kuyers. “You want it going to your attachment drive circuit. You really need to be able to fine tune and dial that in. Especially with a trencher, you really don’t need a lot of tractive effort, but you need all of that hydraulic power going to the trencher drive.” The same applies to a rock saw.
“Conversely, on a vibratory plow, you are constantly balancing between the ground drive and the amount of shake you have in that plow to help it cut its way through the ground,” says Kuyers. “Soil conditions change and it may require more shaking force in certain conditions, where in other scenarios where the ground is softer, you can actually turn your ground drive up and your attachment vibrator down to increase productivity.”
Dealing with Obstacles
It’s inevitable that you will encounter underground obstacles in almost any trenching application. In the past, operators had to have quick reflexes to prevent a machine from stalling as it hit an object. They had to disengage the ground drive and the chain drive in a split second and then reengage the drives at the correct speed.
“When the operator is trenching and hits a tree root or a large obstacle, the chain will stall and will, in many cases, shut the engine down,” Kuyers points out. This can be hard on the equipment. “That is not good on the engine or the machine itself because it puts it under a lot of stress.
“It happens so fast, the operator doesn’t have time to react,” he adds.
Modern electronics now allow the tractors to react automatically to obstacles. For example, Vermeer offers its Trench Sense feature. Trench Sense senses the rate of pull down in the engine as the chain stops. It stops forward movement of the machine, backs it up slightly, reverses the chain and then engages the chain and begins to creep forward almost simultaneously — all without the operator having to touch the controls.
In addition to saving wear and tear on the machine, there is a productivity factor with this feature. “When you are trenching in chunky rock, the operator doesn’t have to constantly adjust, put it in neutral and readjust all of the levers,” says Kuyers.
There are other features that can also help deal with buried obstacles. For instance, Toro offers the HD PowerTrench drive. It stores power from a flywheel that is transferred to the torque amplifying planetary system. This gives the HD trencher the power to overcome rocks or other obstacles in a wide range of conditions.
Keep It Level
The ability to self level is another useful feature. “Track leveling or machine leveling makes it so the ditch is vertical when the machine is digging on a side slope,” says Preston Renfro, production manager, Tesmec. “This is done automatically by a level sensor and the operator need not worry.”
Ditch Witch trenchers compensate for uneven terrain with a frame tilt feature. “This feature enables the operator to ‘tilt’ the tractor frame and hold the attachment completely vertical,” says Seabolt. “Vertical trenches are the most effective and efficient way to displace soil without unnecessarily loading or damaging the machine.”
Some tractors offer the ability to automatically adjust frame tilt as needed. “On the Toro RT1200, operators can choose the optional auto-tilt, which will adjust the angle of the frame automatically to accommodate changing surface terrain,” says Beddow.
Attachments Add Versatility
Attachment availability really depends on tractor size.
“Models with 50 to 150 hp typically offer more options than large track trenchers used primarily in rock and pipeline projects,” says Seabolt. “These smaller ride-on tractors typically support trenchers (fixed or offset), plows, combos, earth saws, backhoes and reel carriers. On some of the medium- to small-sized models, micro-trenching attachments are also available for jobs that require small, clean cuts such as those used in fiber installation.”
Micro-trenching is a growing application due to the booming fiber optic installation market. “Fiber optic installation will continue to be robust because the demand is so strong,” says Kuyers. “So a micro-trencher attachment needs to be part of the arsenal of a ride-on tractor.”
The incorporation of reel carriers and backhoe attachments can help contractors do more with a single machine. “This not only minimizes capital expenditures, but also creates a more productive jobsite, ultimately adding to a contractor’s bottom line,” says Beddow.
“Front attachments, such as reel carriers and backhoes, reduce manpower and the need for dedicated support equipment such as excavators, reel trailers and tow vehicles used in the transport and operation of support equipment,” says Seabolt. “This saves cost, time and space, which are at a premium on most jobsites today.”
Combo attachments are one option to help you maximize utilization. “Combo attachments offer two sets of tools, typically a plow and a trencher, which enable one machine to perform multiple jobs,” says Seabolt. “These tools can also be used together on jobsites where short trenches are dug as entry or exit ‘pits’ for the vibratory plow blade and product installation.”
Combo attachments allow you to select the best tool for the job. “Plows are generally more productive and require less jobsite restoration than trenchers, thereby reducing costs,” says Seabolt. “The trencher half of the combo allows you to place product in some conditions where you could not plow and gives you the ability to install products with larger diameters.”
A vibratory plow offers many advantages in terms of soil disturbance and productivity in the right soil and application. “But vibratory plows are limited to soft and ideal ground conditions,” notes Renfro. “A trencher can handle a wide variety of ground conditions a vibratory plow couldn’t even consider.”
While vibratory plows offer several advantages, you need to be more selective with these attachments. “Vibratory plow design is a bit of an art,” says Seabolt. “The tractor wheelbase, plow linkage geometry, plow blade shape, shaker box amplitude and a variety of other variables must all be considered in a highly productive plow attachment. Operators should select a plow attachment from a reputable manufacturer designed and tested in conjunction with the tractor.”
Check whether the plow has a steerable shaker box. “Plows should have the steer and float functions as well as raise and lower,” says Kuyers. “That gives you an added level of productivity for placement of product in the ground, especially when you are plowing around obstructions on the jobsite.”
Before purchasing a tractor, note what attachments are available. The ability to switch attachments from a chainsaw to a rock saw or a drum cutter can maximize utilization or enhance operating performance. “Many models have versatility like this designed into the unit,” says Welch.
Large trenchers, such as those in the Tesmec line, offer their own attachment solutions. “In our line, we don’t yet make reel carriers. But we do offer custom-design cable guides that allow the customer to lay the line out and transfer it up over the top of the machine as it trenches, laying the cable in the ditch as it is dug,” says Renfro.
Some attachments can tailor operation to meet specific jobsite requirements. Consider the differences between a standard dual auger trencher attachment and a conveyor trencher. “There are a lot of utility-type installations where the contractor does not want the spoil on both sides of the trench,” says Kuyers. “They want it off and away from the side of the trench so they can install the product without having any of the backfill material fall in the trench. It is a lot easier to lay larger pipe because you can lay it right close to the trench and drop it in without having all of that other material fall in.” Plus, sometimes you might want to backfill with sand vs. the material that came out of the trench.
The ability to offset a trencher attachment adds complexity and cost, but can quickly pay for itself in the right applications. “There is no impact to productivity [when using an offset trencher attachment], but instead an increase in versatility for the user to efficiently trench in tight conditions,” says Renfro.
The sliding offset attachment available on Toro tractors allows the trencher to start in the center of the machine and move almost 30 in. on the slider track. “This increases accessibility in tight locations and facilitates the placement of utility lines closer to the desired location without the operator having to reposition the entire machine,” says Beddow. “Essentially, it puts more control in the hands of the operator and helps cut downtime in the field.”
Maneuverability in tight space is also a consideration. Consider the steering options available on the tractors you consider.
“Ditch Witch tractor designs offer rear steer on most models, which ensures maneuverability in tight spaces,” says Seabolt. “This also gives operators the ability to ‘crab’ while plowing, which effectively allows them to plow much farther offset than possible otherwise. This is especially valuable when working along a roadside or in areas where traction and access is otherwise limited.”