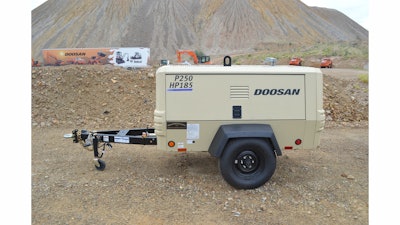
Choosing power sources for the jobsite has become more complicated as traditional diesel-powered generators and air compressors have grown more costly to purchase due to Tier 4 Final regulations. While the Tier 4 technology does promise improved fuel economy, many new technologies have also sprung up.
First, let’s look at the evolution of the air compressor market. Compressors are now offered with electric and natural gas options.
Doosan Power Products recently unveiled an electric-driven portable air compressor. The VP900e provides infinitely variable pressure and variable flow. It operates between 400 and 900 cfm without wasted energy by delivering the exact flow necessary for an application.
Three onboard electric motors, controlled by a variable frequency drive (VFD) system, replace the diesel engine. One electric airend motor and two cooling fan motors are each sized specifically for their dedicated function. This design creates operational efficiencies, using less power than is required of a one-motor-fits-all design.
During operation the VFD automatically adjusts to the load demand, maximizing flow for each pressure setting. This saves power costs and wasted energy over other compressor models that require the motor to run wide open at all times. The operator has the capability to set the pressure at any level from 90 to 150 psi, a unique feature for portable air compressors.
The VP900e is emissions-free and ultra-quiet. It is not subject to EPA emissions regulations or Transport Canada fuel tank regulations. “It is a very good temporary source for air where you have 480-volt power,” says Rus Warner, product marketing manager of air products, Doosan Portable Power.
While this is naturally a good industrial rental machine, it has also had success with contractors working in the oil and gas business, where they must meet a carbon footprint. “There is a growing segment of traditional jobsites where there is already a larger generator,” says Warner. “It’s more efficient to use a large generator to power an electric air compressor compared to using a diesel air compressor.”
Then there is the purchase cost. Warner claims the acquisition price is 15% to 20% lower than a Tier 4 Final diesel engine-driven compressor of the same size.
Gasoline-powered compressors are even making a comeback as a result of the Tier 4 Final diesel price increases. “The technology for gasoline engines has greatly improved. We can make a reliable gasoline unit with good torque that is less expensive than the diesel unit,” says Warner. “You can get good ROI with a gasoline machine now. The operating cost is very similar because the run time and efficiency of the gas vs. the diesel is surprisingly close. We look at dollars per cfm and there is no real disadvantage of going with gasoline. It is just a simpler machine.”
But diesel-powered compressors are still the bulk of the market. When it comes to traditional diesel-powered compressors, there are advancements that make them more efficient than previous designs. “Automatic unloader valves and speed regulators are some of the latest advancements we incorporate into our compressors, and they can have a significant impact on fuel consumption,” says Rich Elliott, product manager, low pressure compressors, Atlas Copco Portable Energy.
“When operators use multiple pneumatic tools with one air system, the output from the air tool and motor can be reduced, which means your tools won’t operate at peak performance,” says Elliott. “In response, the engine speeds up to maintain the right output so productivity won’t be affected. These fluctuations can lead to increased fuel consumption during peak demand times. To combat this, we use stepless, fully automatic unloader valves and speed regulators in many of our models, including the Tier 4 Final XAS 185. These valves and regulators constantly vary the engine speed to match the demand of the operation, which helps save fuel.
“Being able to quickly and easily operate your compressor is also important,” notes Elliott. “Our compressors are equipped with electronic controls that signal the engine to adapt to changing load demands and allow operators to quickly set their working pressures. We also incorporate diagnostic systems that quickly identify any operating complications.”
When adding any compressors to your fleet, Elliott advises you consider the control systems. “If you’re purchasing different compressor models, it’s also a good idea to select those with similar controls. This allows operators to quickly switch between the models without learning to operate an entirely new system. All Atlas Copco Tier 4 Final compressors are equipped with electronic controllers that have similar programing.”
And despite the increased purchase price, there are advantages to Tier 4 Final compressors. “We designed all of our air compressors to save on fuel costs and preventative maintenance as our customers transition to Tier 4 technology,” says Elliott. “Reducing fuel consumption is one way we minimize operational and ownership costs in all of our compressor models, not just the Tier 4 Final.”
Atlas Copco utilizes the FuelXpert regulation system on its larger compressors, from 750-cfm models and up. “The system saves operators 5% to 15% in fuel costs when the compressor is running at 35% to 80% capacity,” says Elliott.
Multi-use Compressors Increase Versatility
Multi-use compressors, such as the Doosan dual pressure/dual flow P250/HP185 add flexibility for the contractor.
“They can use the same machine for multiple applications, so it is a more useful tool for them,” Warner explains. “For example, in 250-cfm, 100-psi mode, it is very good at running pneumatic tools — breakers, rivet busters, etc. But when it is flipped over to the higher pressure, the 185 cfm, 150 psi, it can be used for abrasive blasting, pressure testing pipelines and other tasks a lower pressure machine couldn’t do. It saves the contractor from having to buy or rent a second air compressor when those pipeline or one-off applications show up.”
This compressor also uses new technology to increase efficiency and reduce noise. Most notable is the electric cooling fan. Thermostatically controlled electric cooling fans only run when needed. “With a traditional design, that fan is always spinning if the engine is spinning,” notes Warner. With an electric cooling fan, the compressor is more efficient and uses less power and less fuel because the engine is not working as hard. Noise is also reduced. “One of the loudest portions of a machine is the fan spinning. When you reduce fan noise, the overall package is quieter.”
New Options for On-site Power
In terms of generators, LP and gasoline provide alternatives to traditional diesel power.
For instance, Kohler Power Systems recently introduced two compact gaseous-fueled generators that can switch between optional onboard LP fuel tanks and external LP liquid, LP gas or natural gas fuel sources. According to Kohler, the 50REZGT and 70REZGT gaseous generators can help reduce users’ fuel costs by 15% to 20% compared to diesel-powered units.
The 50REZGT (50 kVA) features a 4.3-liter naturally aspirated engine while the 70REZGT (70 kVA) has a 5.7-liter engine. These generators include onboard LP tanks, so users working in areas without a propane gas supply can use onboard fuel and then switch to an on-site supply when available. The onboard tank is built for a 24-hour run time. The generators are certified for prime power and standby applications by the U.S. EPA, and certified by the California Air Research Board (CARB). Currently, these generators are eligible for incentives of $1,000 to $3,500 from the Propane Education & Research Council (PERC).
Several multi-purpose units that use the diesel engine to do more than generate electricity have also emerged. “Multi-purpose machines are where the industry is going,” predicts Warner.
For instance, Doosan Portable Power offers the L20, which combines a light tower and a 20-kW mobile generator. It eliminates the need for another machine on the job when you need both power and light. The L20 has four 1,000-watt metal halide lamps mounted on a hydraulically powered vertical mast that extends to a full height of over 25 ft. in less than 30 seconds.
The L20 is a good fit for contractors who need limited power to run a job trailer during the day. “You can run that trailer or jobsite during the day off the generator, and at night you can use the lighting for security,” says Warner. “With just one machine, you can accomplish two jobs.” There are many other applications, such as mechanical contractors or concrete contractors who need to run big floor polishers but also need light since they usually start early in the morning and work late at night.
Magnum also offers the MTT combination generator, light tower and water trailer, designed as a single compact unit. Available in two models, the MTT is suited for powering remote locations with multiple power needs, such as oil and mining base camps, concrete cutting and finishing, isolated road and commercial construction site areas, municipalities and disaster relief.
The MTT combination units are powered by Isuzu 4LE1 liquid-cooled diesel engines with a rating of 31 hp at prime. A large fuel tank with a capacity of 246 gal. delivers over five days of continuous run time, saving time and money on labor and fuel costs.
A 500-gal. water tank has a fill rate of three to four minutes at full throttle and a pump flow rate of 3.3 gpm. There are four outside brass spigots to accommodate water distribution. The light tower features four 1,000-watt metal halide light fixtures with 360° individual light rotation for flexible illumination. The three-section tubular steel mast extends to 30 ft. Dual winch systems allow for one-person operation.
What differentiates the two available models is the MT20 provides single-phase power while the MT25 provides single- or three-phase power. The MT20 offers 20-kW standby/19-kW prime output power with 120V and 240V single-phase power. The MT25 provides single-phase 16-kW standby/15-kW prime output power or three-phase 20-kW standby/18-kW prime power output with 120V and 240V single-phase voltage.
As you can see, there are a lot of interesting options being introduced to solve jobsite power needs. Before you decide that a conventional diesel power unit or another type of power unit is best suited for your application, be sure you do your research. A lot has changed in the past couple of years and there are a lot more choices available.