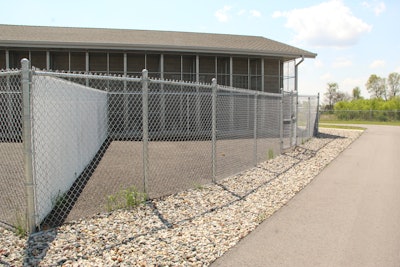
When the Humane Society of Elkhart, IN, decided to construct almost 6,000 sq. ft. of eight new outdoor play and exercise areas for dogs waiting for adoption, they wanted a material that was easy to clean, comfortable for the animals, and porous.
The material they chose was Porous Pave XL, a three-component, pour-in-place permeable paving material that has been used across North America on a wide variety of projects where control of stormwater and runoff is a concern.
Jesse Angel, southern district manager for Permeable Coating Solutions, Greenwood, IN, which completed the Humane Society job, says the product consists of 50% recycled tire rubber chips, 50% granite aggregate, and a proprietary liquid binder. He says it installs just like concrete (its main competitors are permeable concrete and permeable pavers) and when installed properly the finished surface is 27% porous, making it ideal for areas where runoff needs to be controlled.
“If you’re looking to shed water it’s the most porous product on the market,” Angel says, adding that while it’s often installed on patios and walkways, it can be driven on once cured so it can be installed on parking areas and driveways.
A Specialist Contractor
The eight-person Permeable Coating Solutions specializes in constructing permeable surfaces, with crews traveling throughout the country. According to Angel, while many contractors install porous pavement products, most install no more than 3,000 sq. ft. at a time. Permeable Coating Solutions, on the other hand, installs jobs as large as 100,000 sq. ft. in addition to smaller projects. He says the company installs between 300,000 and 500,000 sq. ft. of permeable surface each year.
“Most contractors install it as one of three or four other things they do. And they only do it on small projects because it can be labor intensive,” Angel says. “We install permeable surface on any size job because it’s the only thing we do. We specialize in it.”
And because they specialize in it, Angel has developed customized equipment that enables the company to perform large installations, including a large mixer, a slipform paver and a long-handle roller. He says that in many cases the material can be placed by just about any power screed on the market, which he says is an essential piece of equipment for this material. He recently completed an 8-ft.-wide path, 2 ½ miles long. “You don’t want to be on your hands and knees with a 2 x 4 smoothing out that job!”
Working with the Material
The three components are mixed on site in a mortar mixer, then transported to the location via wheelbarrow or transport buggy. Angel has an 8-cu.-yd. mixer for small jobs and a specially designed, one-of-a-kind 20-cu.-yd. plant for larger jobs. Mounted on a trailer, the plant has a crane that can lift 2,500-lb. sacks of material into two hoppers. The two hoppers calibrate and feed the correct amount of rubber, stone and binder, creating the product that is put down. Angel says the large mixer can produce a 400-lb. batch in 45 seconds.
Once the material is poured (usually 1 in. to 2 in. deep), Angel’s crew uses a combination of its customized slipform paver, power screed and bull float to spread and level the material. The type of equipment is determined by the space available in which to work.
“It’s cold and it’s gooey,” Angel says. “If you’ve ever made Rice Krispy treats, that’s what it’s like.”
Once the material is level, Angel’s crew compacts it with a custom-made roller. The material can cure in as little as six hours (depending on the level of humidity).
Labor-intensive Humane Society Job
At the Humane Society, Angel installed the porous rubber-rock surface on top of 1 ½ in. of ¾-in. crushed aggregate. The aggregate had been installed and compacted by a subcontractor using a plate compactor.
Angel and his crew mixed the material in the 8-cu.-yd. mixer, poured and then leveled the material using hand towels and a bull float. He says that normally his crew can put down between 4,000 and 5,000 sq. ft. in a typical day on an open area. But this project took three days.
“This was an especially labor-intensive job because we had to work around fencing, pens, and the individual kennels,” he says. “Most of the areas were small and very tight to work in.”
Angel says that when properly maintained – including reapplying the binder every three-to-five years – the rubberized porous material can last up to 15 years or longer, depending on the use.
“The Humane Society liked its permeability. They can just hose off the outdoor pens for the animals. It is now a much easier process for them,” he says.