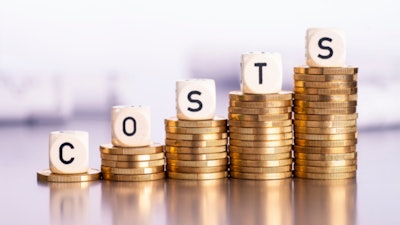
The lookout for most contractors is promising in terms of the amount of work that appears to be available to bid. However, overcoming the continued rise in costs for materials, vehicles, equipment and tools is becoming an even larger concern. And, add the seemingly endless requests by current workers and job candidates for more pay and we have the real coming together of the perfect storm for most contractors.
While we may not be able to control such rising cost, most of which is greatly influenced by our national and world events, there is one area in which we greatly influence, what we control and that is how we proceed to produce work in the most cost-effective way. After years of studying this reality, even with rising material, equipment, etc. costs, most contractor hurt themselves when they do not put on their “full court press” to lower and eliminate their mistakes.
Two brief examples support this last statement. First, it is still amazing that so many contractors either do not have a preventive maintenance program for equipment, vehicles and tools or simply do not execute their own program. From the sealcoating world, one daily “PM” action that should be executed is to always clean out your hoses and tips, not allowing material to harden. Yet, many sealcoating crews will often finish their day and in the hurry to get off the job and go home, will fail to complete a daily flushing out of the hoses. Depending on the time of year, the material left behind may not totally harden, preventing material from being sprayed, but over enough days of the same failure to clean out hoses, the crew will find themselves shut down for hours, maybe days, in cleaning out not only the hoses but perhaps even the lines carrying the material from tank to hoses.
My second example comes from placing concrete. Like ordering asphalt for the paving crew, ordering concrete from the plant is critical as well. However, it’s amazing to see how many crews stranded at the job site because someone didn’t check with the plant the day before to confirm they could get material to the site for a 10 a.m. pour. In some parts of the U.S., contractors may have to place their orders more than one day ahead of their scheduled pour.
When such mistakes are made, it often costs us many hours in waiting.
The two examples provided are easy to see because most contractors have all experienced them…sometimes multiple times. Yet the cost of such mistakes add to the “rising costs” presented earlier. The difference? We (contractors) control the two mistakes in the examples provided. Such mistakes can have a direct negative cost impact of hundreds, if not thousands of dollars. And if we embrace the teachings of Dr. E. Deming, known as the “Quality Guru,” then we actually experience a “3 X 1st Cost.” Briefly, this is how that breaks down:
If our COST to sealcoat a parking lot is $10,000, then if we perform it right the first time, we make the profit that was put on top of the cost. However, if our crews make mistakes where we have to replace the first effort, there is another $10,000, since material doesn’t come free, our workers do not work for free. Yet, Deming said there was a third cost. This third cost is known as “Lost Opportunity Cost,” that is, we lost the opportunity to make money on this third cost applying it to a new project of equal value. Therefore, instead of doing the job right the first time and making money, there is a very good likelihood that this one job cost us $30,000 and we lost our shorts!
This reality about mistakes, “3 X 1st Cost,” Deming called the Cost of Quality. In short it means, do things right the first time and you make money; do things twice and it costs you three times the initial cost amount…and sometimes more.
Contractors cannot control the price of oil, steel, equipment costs, etc. but we can control all that we are responsible for once the people, materials, equipment and tools are in production. May we all work harder, and smarter, in lowering our actual cost of production. In the end, it may be all we have that defines our reputation and longevity as a contractor.