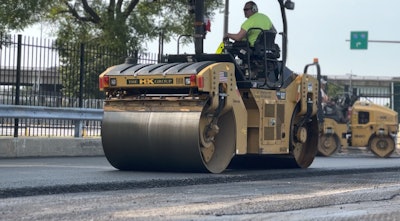
The Philadelphia Sports Complex is where the NBA’s 76ers, NHL Flyers, MLB Phillies, and NFL Eagles all call home. One gigantic asphalt playground for all the city’s major sport fans. All-Out Parking Lots first started doing sealcoat work in some of the surrounding lots about ten years ago. That was a job that they say came about from what literally amounted a cold call, and, year-by-year they’ve earned larger and more complex maintenance work with the popular city destination.
As native sons of Philly, Marco Menna and Kevin McGarvey’s history isn’t just rooted in the area in general, but they have “business” ties going back to the high-profile jobsite location where they milled, paved, sealed, and patched over the course of two weeks.
“Our first business venture here was a while before that, though,” said McGarvey. “When we were in high school we had this hot shot idea to sell t-shirts outside a big concert, so we dropped $400 on a box of knock-off Kenny Chesney merch.”
Menna interjected, “To a highschooler, that was like an insane amount of money, but we thought we were going to walk away rich.” Their entrepreneurial spirit was not appreciated at this stage in their career. “Literally, within five minutes security pulled up to us, confiscated all our merchandise, and kicked us out.”
At this point it’s fair to say that, after a decade of a continually expanding list of maintenance projects with the complex, that initial loss has been made back many times over. The work they’re doing this year is massive.
The Scope Of The Work
The Philadelphia Sports Complex is a sprawling center for fandom and entertainment in the city. It’s located within walking distance to some nearby neighborhoods, but for those driving in for a visit, there’s plenty of parking space. With nearly ten million square feet of blacktop, it’s a big job to keep it all serviced and safe.
“For this particular job we’re doing 500,000 square feet of sealcoating, crack sealing, and line striping,” said McGarvey as we walked from one patch job being completed, past the Phillies stadium, and towards where the bulk milling job was underway.
“We are also doing 200,000 square feet of milling and paving,” he continued. “In addition to all that, we have just over two thousand square feet of excavating and patching. That’s the whole project.”
The timing of when to conduct this body of work was important, and the first two weeks of June were perfect. Despite the city’s disappointment when the 76ers were eliminated from the NBA playoffs, it signaled the start for All Out's crews, and they had to be ready to go. The scheduling is a matter of calculated coordination.
“For a very brief period, there’s a lot fewer events, and we are taking full advantage of that. But we still have to plan the job out as efficiently as possible,” said McGarvey. “Right now, the Phillies have one week of consecutive away games and travel. For their main parking area, this phase is all crack sealing. Then they’ll be home for a week, and we’ll pause the work until the following week where they’re gone again. That’s when we will tackle sealcoating and re-striping for that area.”
Marco took me over to where a squad of their crack sealers were gradually winding their way over a spider-web like network. Each worker had a combo melter/applicator box on wheels. It was the first actual thing on this visit that I got to take a “crack” at (pun intended). The biggest takeaway from that, for me, was that it looks a lot easier than it is.
I struggled to keep the balance of melted material within the applicator squeegee and stay in-line with the depth and direction of the pavement cracks. A great example of the saying, “There’s no such thing as ‘unskilled’ labor.” Because there’s a huge gap between how fast the All Out crew members were hustling, and the stop-and-go method I brought to the scene.
The Mill and The Fill
E Lot (the executor lot) at Wells Fargo Arena is where the biggest work took place. All-Out's 7-foot Wirtgen mill churned out a full tri-axle load every two and a half minutes. The team took up 3 1/2 inches of depth, but below that the base contains an extra ingredient they had carefully avoid.
“It’s called a geotextile fabric,” said Pedro Bermudez, a project manager and pavement advisor for All-Out Parking Lots. “The base on any pavement surfacev is 80% of the strength. That makes this material ideal for roadways and big traffic areas. It comes in really large rolls, tacks the existing surface, and then it rolls out. Then they can pave right over top of it.”
I picked up a small scrap of the material that was kicked up during a milling pass. It felt a lot like a roofing shingle, except thinner and more flexible. “Little pieces like this aren’t going to effect the mill, but if you were to run the whole thing up, constantly, it would slow down the process.”
When it comes down to the paving, the crew brought in a highway class CAT AP655F (as shown on the cover of the issue), laying down two and half inches of compacted base layer, and one and half inches compacted of top course, in two lifts. A total of two hundred thousand square feet, or thirty-two hundred ton of asphalt. The goal was to reach 4 inches after compaction.
To ensure that the quality of the mat met spec, they had a nuclear density tester, and a specialist to utilize it on site, taking measurements as the work progressed. The sensitive tool uses gamma rays to bounce through the mat, measuring air holes, and gives the crew a sense of how many more passes are needed to reach peak compaction.
Patching Busted Drainage
On the second day of the jobsite visit, rain was a very present threat to the day’s work. An old catch basin was needed to be removed, the new one put in, and the area around it repaved.
“This is the kind of work, when you come in and assess the project for a client, that you find and that identify the major liabilities for the client,” said Menna, and pointed to the exposed underside of the concrete basin as it was removed by mini-excavator. “You can see how it’s just crumbling underneath. If that were to collapse, that becomes a serious liability issue.”
In order to try and get ahead of the weather, I tagged along with Jeffery “JP” Parris to the asphalt plant to fill up All-Out's asphalt hot-box. JP had personality by the truck load, and wasn’t shy in sharing some of his three decades of knowledge and experience. In fact, when we reached the plant we were given a small tour of the facility by someone he had worked with years before.
The real fun for me was when we returned to the catch basin, and was put behind the “wheel” of a small plate compactor. After they installed the new basin, rain just started to fall lightly over the site. Everyone grabbed shovels and started spreading the hot asphalt as quickly as possible. Even Operations Manager Javier Valdez jumped in.
“I started out on the shovel, so I know what that’s like,” he told me later. “All the time, guys will say to me, ‘Why are you doing this or that? You are the foreman, don’t have to do it.’ And honestly, sometimes I do it just because I don’t want to be bored,” Valdez laughed. “But seriously, it’s important to me to show my guys that I know what the work is, what it takes, and we are all on the same team.”
Not too long after, I was asking him for help as I tried to effectively use the plate compactor. I approached it like a lawnmower, but it was definitely piloting me more than I was piloting it.
It’s a strange thing to balance when you’re out there on a job like this, and it crossed my mind multiple times while I was there. Everyone watching me knows what they’re doing, and I came to learn, but at the same time you don’t want anyone to think that’s it’s just for “show.”
When I come to a jobsite, I want everyone to know I’m there because I respect the work. That’s first and foremost. I might make jokes at my own expense, but I don’t think the work is a joke in the slightest. I’m thankful for people like Javier, Pedro, and JP who took the time to show me these things hands-on.
Growing A Company Takes Relationships (and Money)
It’s a cliché to say it, but it still takes money to make money. And for All Out Parking Lots, their growth over the last 10 years has meant an increasing amount of resources needed. While visiting with them for the Philly Sports Complex job, I learned something that won’t come as a surprise to any contractor reading this story.
They don’t get paid when the job is completed, not usually, and the larger the corporate entity they deal with, sometimes, the larger the gap between completion and payment.Marco Menna (left) and Kevin McGarvey (Right)
“It’s just literally the cost of doing business at this level, and with these types of customers,” Menna said. “We have to build that into all of our job costing, how long we might have to float the money for one job, and the interest loss on that float period. It has to be taken into consideration or that’s just a loss then for us.”
Some large national corporations and chains that All Out does business with only pay out on contract work like theirs three to four times a year. With so many moving parts, and internal processes that take many months to move through, it takes a long time no matter how you slice things.
“If you’re a mid-level size operation, and you want to someday move to this tier of work, you can’t do it alone,” said McGarvey. And what he’s talking about isn’t just having a strong business partner, staff, and management team. He’s talking about having a strong business relationship with your bank.
“Your bank might not understand our industry, how it operates, the flow of finances,” he said. “What we’ve done with our financial institution is to bring our books in, show them what’s out there, what’s coming in, and we’ve shown over the course of our time working with them, a strong level of consistency.”
That’s not something you can build overnight. While, at first, they wouldn’t have been able to float these kinds of jobs, according to Menna, it’s not unusual for them to have $1 million out there.
“This is why accurate job costing become so important, because when you’re dealing with a credit line, and even relatively low interest rates on that kind of money, you don’t want to be off,” he said.
It all ties back into their company ethos, as well as the culture of the city where they’re not only from, but the city they decided to stay in, put down roots, and build their business. They’re meticulous, and it showed on the way they managed the work and the phasing for the Sports Complex. It’s why they keep getting asked to do more and more of the work there.
The real foundation of All Out Parking Lots comes from something even deeper. “Friendship,” said McGarvey. “That’s what we are built on, and that’s why I think we’ve been able to create a successful business together. Marco and I have been friends since the sixth grade.”
That friendship and partnership continues to bear fruit today in the city of brotherly love.