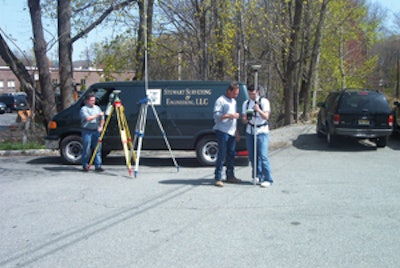
Executing a basic parking lot layout is old hat to many striping contractors, but that's only true when the layout and design are straightforward, the lot can be squared up, and there's enough time in the schedule to make sure it all gets done right.
But when those elements aren't in place, and the project goes from challenging to darn near impossible, how do you get it done? That's the question Vinny Toth, owner of V&V Line Striping, Boonton, NJ, asked himself last year after he was awarded the striping on a redesigned layout of a parking lot at Six Flags Great Adventure. The repair and sealcoating job, done by Advanced Pavement Technologies (and profiled in the March/April 2006 Pavement) was fraught with its own pitfalls, but the whole reason for the sealcoating job was to redesign the layout. The park's engineers needed to add an additional 1,000 parking spaces—despite having taken a bite out of the parking area with the footprint for a new roller coaster.
"When we bid it we planned on creating a nice square and laying out the parking within that square," Toth says. "We could have done that but we would have lost parking spaces and they couldn't afford to do that. So after I saw the layout they needed, I said to myself, ‘Now that I've got this, how are we going to do it? And how are we going to do it in such a tight time frame?'
"Most jobs are consistent with themselves," Toth says. "On this job nothing was consistent and nothing was square. Each part of the lot was different all the way across. Six Flags wanted one drive lane, with one-way traffic, but not even like a wishbone.
Some angles were 30 degrees, some were 45 and some were even 40 degrees. That's what made it so difficult. If you have it square and you have 45 degree angles throughout and it's consistent over 10 rows you can snap a line right across and it's pretty easy to lay out." Toth says. "But Six Flags couldn't afford to lose any spaces so we had to lay out each and every row differently."
How GPS helps stripers
So Toth turned to Fred Stewart, Stewart Surveying & Engineering LLC, Rockaway, NJ, which V&V has relied on in the past for unusually difficult layouts. Stewart, using a Leica Geosystems GX 1230 GG global positioning system (GPS), was able to ease the layout, increase the confidence level of V&V and its crews, enable the crews to work more quickly, and provide an opportunity for V&V to both finish the job on schedule and for profit.
Working as a subcontractor to V&V, Stewart essentially assumed the responsibility for the layout the park wanted.
"V&V wasn't responsible for the layout, I was," Stewart says. "So rather than Vinny having to worry about laying out a certain angle, we had it all figured out for him. All V&V had to do was go out there and snap their chalk lines off our marks, and start painting. They could basically do the striping off my points and check on themselves every few feet."
Stewart says most jobs require at least two visits to the site: the first visit to set up a control network of GPS points; the second to mark points for the stripers.
"We start with the engineering drawings so we know what the finished job is supposed to look like," Stewart says. "Then we coordinate that engineered layout with the GPS coordinates we're using in the field. Then, using the computer, the engineering drawing, and the GPS map we assign numbers to key points within the striping area."
Any GPS unit receives signals from a satellite. The GPS unit manipulates the signals into coordinates indicating a location on the Earth. The coordinates are related to a set of known coordinates, in this case GPS coordinates of a state GPS map.
At the Six Flags site Stewart set up a "base station" with one GPS unit at a known GPS coordinate (a surveying marker already placed in the ground). Once the base station is established, Stewart dons a "rover station," which includes a backpack unit with a pole-mounted antenna. As the rover walks across the site, the rover and base stations communicate with one another and with the satellite. Through triangulation (the satellite, the base, and the rover) Stewart can pinpoint a location on the Earth and assign that location coordinates.
How does he decide what locations to mark with GPS? Partly he selects specific locations he can use to verify that the engineering design he received is accurate.
"We sometimes run into situations where the design on the paper is not consistent with the exact site conditions, so we set up control points to verify the accuracy of the design," he says. "We'll mark the outer limits of the parking area, for example, the corner of a building, and light poles within the lot itself."
These "known" points serve as a control network. Once Stewart has established "known" points on the parking lot, he returns to the office, uploads the points and their coordinates into his computer, and then overlays the map of coordinates onto the engineering design to make sure they are working off the same dimensions.
"The engineering design often uses a digital plan based on aerial mapping to show the outer limits of the lot, but sometimes the aerial mapping is not up do date," he says. "Maybe the parking lot was extended 5 or 10 feet in on area for some reason, so we locate the perimeter of what the intended limits are. None of that happened on this job. It went okay."
Then, using the established GPS coordinates, Stewart assigns new coordinates to specific, important points within the engineering design's striping layout.
"Using the computer we point to the end of a centerline, for example, and tell the computer to give us the coordinates of the end of that line. It does and we mark that point and the coordinates in the layout," Stewart says. "Now we know exactly where that centerline needs to start to execute that layout."
He works his way through the entire layout that way, using the computer and GPS points to determine coordinates of other important layout points. Important points include the beginning and end of a bank of stalls, the beginning and end of a stall stripe, or any point in the layout where a centerline might bend.
"Basically we determine coordinates for key locations where a striper might run into a problem or any place in the layout where the people striping need to know something different is going to happen," Stewart says. "We also will provide some markers along long lines so the striper can check himself as he goes."
Once he has determined the coordinates of the key locations, he loads that information into the Leica Geosystems GX 1230 GG GPS units and returns to the site to mark them on the pavement for the striper.
Back on the site
Once on the site Stewart essentially reverses the process, again using triangulation with the satellite, the base, and the rover.
So assume Stewart assigns "100" as the number of the end of one centerline and "101" as the opposite end of the same line. At the site he tells the GPS unit he wants to go to Point 100 and the unit tells him how to walk there.
"We tell the GPS unit what point we want to go to and it actually tells us where to go to get to that point—maybe 50 feet north and 20 feet west or whatever it is," Stewart says. "We walk in those directions and as we get closer to the point the unit begins to beep. The closer we get the more rapid the beeps become, and once we reach the point it's one solid signal, no beeps."
Stewart then paints the point number on the pavement. He continues the process until all the point numbers essential to the layout are painted on the parking lot. Once the points are marked he gives the striper a printout of the layout with all GPS points marked, and the striper can start chalking the layout.
"Vinny is not working blind out there," Stewart says. "He has a copy of the layout with the numbers indicating essential points, and he can match those up with the point numbers we painted on the ground for him. There's no question about what he's doing and the work goes smoothly. From that point on it becomes a game of connecting the dots."
Striping the job
On this job Stewart divided the project into six smaller sections so V&V could work while Advanced Pavement Technologies was repairing and sealcoating other areas. Once the GPS points were determined for the layout, V&V's crews start chalking the lines. On the first day all V&V's crews worked the morning snapping chalk lines. That afternoon one crew began applying paint.
Throughout the job V&V used two 4-person crews to keep layout, striping, and stenciling of more than 150 arrows moving. Crews used Kelly Creswell and JCL air stripers because he says air stripers are more forgiving on the pavement.
"We always use air machines," Toth says. "Airless machines put down such a crisp line that they show every imperfection with the asphalt. Any bump or pebble in the pavement makes the line look bad. Air machines help the striper overcome imperfect pavement."
Toth says that in a straight layout a 6-person V&V crew can typically stripe up to 3,000 stalls a day.
"That's how complex this job was," he says.
When to turn to GPS
Using global positioning to lay out a parking lot is obviously not necessary on most jobs. Small fast-food and strip mall parking lots can be chalked and striped without turning to GPS. But as the lot gets larger, or if the layout cannot build easily off of previous lines, striping contractors might want to consider bringing in a GPS specialist.
"A lot of it depends on the comfort level of the striper," Stewart says. "If he feels he can layout banks of stalls 200 feet long, then okay go ahead and do it. But the longer the run of stalls, the greater the chance for error where you could run into a problem."
Stewart emphasizes that distance compounds any measuring inaccuracy, pointing out that a 1-inch-per-stall mistake over a bank of 10 stalls might be able to be absorbed within the layout without a problem. But a 1-inch-per-stall mistake over 400 stalls will cost the layout a number of stalls and would skew the design.
"Certainly any layouts with banks of stalls over 400 or 500 feet can benefit from GPS," Stewart says. "When you start getting that long it's easy to veer off instead of going in a straight line."
He says costs of hiring a GPS specialist vary. Stewart's company charges by the hour and spent 30 hours on the V&V job, eventually billing the company more than $3,000.
On the eighth day of the 14-day job Six Flags job Stewart was able to get on site to take GPS readings, and on the ninth day he placed initial coordinates on the pavement, enabling V&V to begin chalking and striping. On the last day of the schedule V&V completed new layout and striping for a bus parking area and the handicapped parking area, and the job was finished.
"It was the most difficult layout we've ever done, and with the help of GPS is worked out very well," Toth says. "It could have been a nightmare but it turned out to be a profitable job."