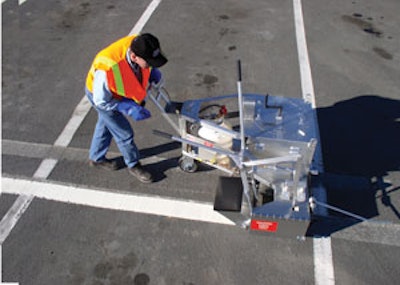
You have been striping parking lots and street corners for years with a traditional walk-behind paint striper. Now, suddenly, a customer asks for a more durable line, one that will last up to three to five years. After all, repainting can be costly and, depending on customers, the subsequent disruption can mean a loss of business for them.
In an increasingly competitive marketplace, if you can find ways to reduce operating costs for your customers, you can find a way to add positive numbers to your bottom line. In this case, the line is made of thermoplastic material. Wait a second, you say. Applying thermoplastic is costly. For starters, it requires using a totally different hand liner, a means to melt the material, and possibly a trailer to haul around additional equipment. Then there is the material and the process itself, which to some may seem a bit laborious compared to laying down paint. The truth is, say two marking equipment manufacturers, the return in thermoplastic technology is well worth the investment for pavement contractors looking to capitalize on a growing niche market.
The market
One may ask, "Can there really be an increasing demand for a technology that has been around since the end of World War II?" The answer is a categorical "Yes," says Steve Shinners, vice president of sales for MRL Equipment Co., in Billings, MT, and Rose Connelly, inside sales manager for M-B Companies in New Holstein, WI.
"Increased traffic volumes today require more durable marking materials, and local government bodies as well as major chain stores such as Lowes and Home Depot are specifying thermoplastic," Shinners explains. "Being able to supply this service is one way pavement contractors can grow their sales and it serves to differentiate them from contractors who exclusively apply paint." He notes that thermoplastic also brings with it a higher profit margin than paint striping.
Because thermoplastic lines can be 6 to 10 times thicker than a paint line, the technology has been more popular in southern states than in the north where snowplows and other snow removal equipment can damage lines. As Connelly adds, though, the use of equipment to feather the line's leading edge and the fact that thermoplastic is easy to patch has made the technology attractive in many colder, northern states, as well. "The cost effectiveness of the technology makes thermoplastic something more and more contractors are looking at seriously," she says. "In addition, there are equipment options available today that make the process more affordable, especially for smaller contractors."
The process
Contractors who want to apply thermoplastic stripes with a walk-behind extrusion applicator have two basic options. They can employ a pre-melter to heat the thermoplastic and apply the material with a hand liner or use a smaller melter/hand liner combination that essentially removes a step out of the process. Either way, the material is heated to 400°F - 425° F and then applied to the pavement. An LP gas heat source keeps the material at the proper temperature in the hand liner during the striping application.
Walk-behind hand liners can hold up to 200 to 250 pounds of thermoplastic material and another 50 pounds of glass beads.
Operators lower the die to the pavement using one control lever and control the flow of material into a die with another.
As Shinners explains, pavement and air temperature should be at least 50°F and the surface dry at the time of application.
Thermoplastic can be applied over old markings but adhesion will only be as good as that of the existing stripe, he adds, noting that new concrete should be allowed to cure at least 14 days and any curing membranes or compounds should be removed prior to striping. Consult your thermoplastic supplier for their recommendations if in doubt.
"Since the application temperature of thermoplastic is in the 400°F - 425°F range, operators need to be cautious," Shinners emphasizes. "They must wear welding-type gloves, long sleeve shirts, steel toe work boots, and have a suitable face shield when loading pre-melters. There should also be a cooler of water nearby and a ‘burn kit' on site should they come in contact with hot thermoplastic."
The equipment
Hand liners can be fitted with any of several different die sizes for stripes varying in width from 4 inches to 12 inches. Features include a glass bead dispenser to add reflective quality to stripes and an onboard heat-source. MRL Equipment and M-B Companies offer two walk-behind models.
"Both of our MRL Equipment Companies Model 250ATC and 250MTC units have a 250-pound capacity and a quick change die system that requires no tools," says Shinners. "The major difference between the two units is the temperature control. One features automatic temperature control whereas the other has a manual control. Most contractors, today, prefer the model with automatic control." Both units can be equipped with an optional, "on board" Mini-melter that allows the melting of thermoplastic on the hand liner itself.
M-B Companies markets an Apollo® II and Apollo® III walk-behind extrusion applicators. Apollo® III features a standard or Speedmelter that again allows operators to continuously melt and apply material without the need for separate pre-melters or other support equipment. The Speedmelter is an option on Apollo® II.
"The feature, which is designed to melt blocks of thermoplastic material, is ideal for small jobs, and it will allow a single operator to apply up to 1,500 sq ft of markings in a normal work day," Connelly says. "Our units are also well-balanced to enable operators to easily maneuver them left or right to accommodate turns or when striping arrows."
Shinners says that using a hand liner with separate melting kettles can dramatically increase production for pavement contractors targeting bigger projects. "As a general rule of thumb, figure daily melting at three times a melter's capacity. For example, a 1,500-pound melter will produce 4,500 pounds of 425° F of thermoplastic in an 8 hour day. This would equal nearly 15,000 feet of 4-inch wide material applied at 90 mils." He notes that pavement can be stripped at a thickness of 60 mils, 90 mils, and 120 mils.
The costs
The average price of a hand liner equipped with one die and a glass bead system is around $7,500. Additional dies cost anywhere from $375 to $1,000 each, which puts the price tag at about $2,000 more than a walk-behind painting unit. The price, though, does not include the cost of skid- or trailer-mounted pre-melters, which range anywhere from $14,000 to over $30,000 depending on the models. Again, contractors targeting smaller jobs can dramatically reduce their initial investment by purchasing a unit equipped with an on-board melter.
There are other costs to consider, as well, Shinners says. He says hand liners will consume anywhere from 20 to 25 pounds of LP gas per day and a typical set of two 1,000 pound pre-melters will consumer 24 pounds of LP gas per hour. Then, of course, there are material costs, including the cost of glass beads. The beads sell for 30 to 50 cents a pound and are applied at a rate of 10 pounds per 100 sq ft. Thermoplastic sells for approximately $800-$1,000 per ton.
Despite the fact that applying paint is less costly than laying down thermoplastic stripes, thermoplastic makes up the difference in wear life. In fact, assuming a painted stripe needs to be repainted twice a year and that a thermoplastic stripe will last four years, thermoplastic will have eight times the wear life.
Shinners estimates that at that rate the material cost for a painted stripe (4 inches x 12 inches) costs approximately $.08/foot per year compared to $.04.5/foot per year for a thermoplastic stripe.
One of the biggest benefits to customers is that the parking lot will not be tied up each year during the restriping process. That's good news for your customers, and if it's good for them, it's good for you.
No, thermoplastic is not for every pavement contractor, many of whom will still prefer to subcontract out projects that specify thermoplastic. For others, though, the technology will do more than heat up materials for a more durable striping job. It will actually heat up sales in a growing, niche market.
Based in Neenah, WI, Rod Dickens is a freelance writer specializing in the construction industry.