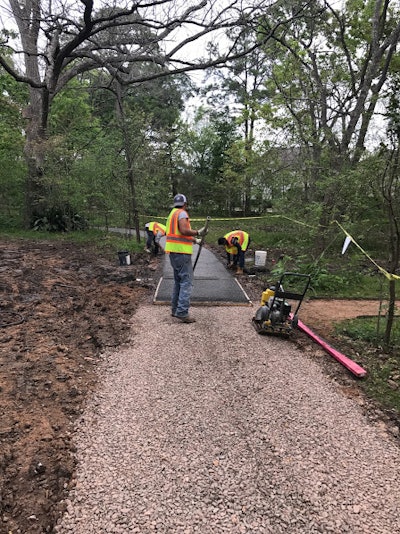
The primary function of porous or permeable pavement is to allow water to run rapidly through the surface to a sub-layer, which allows general or directed drainage. Permeable asphalt and concrete are gaining awareness and acceptance in the industry as good solutions in areas where drainage is an issue.
However, there are situations where the requirements of a permeable paving project can make permeable asphalt or concrete less than ideal and contractors need alternatives. Porous Pave is one option.
What is Porous Pave?
Porous Pave XL is a pour-in-place permeable surface course that differs from asphalt or concrete in that there is no heat, oil or heavy machinery involved in making or installing it. The product is 50% recycled rubber chips and 50% kiln dried aggregate mixed with a liquid binder material onsite in a portable mortar mixer.
Porous Pave is an effective solution when projects require more drainage than permeable asphalt or concrete can deliver. Water passes through the pervious surface of Porous Pave at a rate of 5,800 gallons per hour per square foot, allowing stormwater to percolate down through the base below. This also means that before installation, an open-graded stone is put down to add water storage and protect the base from deterioration.
“The permeability is really the big draw,” says Keith Brooks, P.E., sales engineer at GeoSolutions (a Porous Pave dealer). “Traditional permeable pavement has an air void percentage of 7%, and that allows some water to flow through, but Porous Pave has 27% void space.
“With limited porosity, traditional permeable pavement delivers limited drainage, and it tends to clog with fines and dust particles, so there is more maintenance. Because of Porous Pave’s greater void space, water carries those particles through it,” Brooks adds. “As it gets dust or debris on it, a rain event will wash those particles straight through the pavement instead of clog it.”
Most contractors purchase the product from dealers in 50-lb. bags. On average, a contractor would mix a 50-lb. bag of rock and a 50-lb. bag of rubber chips with 5-qt. of binder. This will yield 16-sq.ft. at 1-1/2-in. thickness.
“A contractor would simply figure out his square footage and divide it by 16 to get the quantities he needs,” Brooks says. “On site, they’d mix it for 60-90 seconds in a mortar mixer and install it. The curing process takes 6 hours before it can be exposed to moisture, with 24 hours full cure for traffic.
“You don’t need to compact it or run a density test on it,” Brooks adds. “Once it’s installed at that recommended thickness, you’re set.”
Fixing a Flooded Path
In March 2017, Porous Pave XL was used to repair a flooded walking path at the Nature Discovery Center in Bellaire, TX. Rainstorms would completely cover the impervious concrete pavers on the old path with four inches of water. Something had to be done to prevent this from happening repeatedly in the future.
"Flooding made our paver path unsafe and unusable," Henry Owen, executive director at the Nature Discovery Center says. "The necessity of building a new permeable path gave us the opportunity to re-design it with more naturalistic curves, winding between four distinct habitat areas."
The Nature Discovery Center and the contractor, Piper Whitney Construction, Houston, TX, considered several permeable paving options. Stormwater infiltration performance, cost, protecting the landscape during construction and appearance were all important considerations.
"Our site was once a pecan orchard,” Owen says. “We have 80-90-year-old pecan trees to protect. We discovered that with Porous Pave, there was no need for big trucks or heavy equipment, and the extent and depth of the required excavation were minimal.
“Porous Pave pours in place, making it easy to shape the path’s curves. The color we chose complements the granite trails in other parts of the nature park. The installation was relatively non-intrusive and the path is now usable and safe right after it rains.”
Once the pavement selection was made, Piper Whitney began work. The project began with a day of excavating out the old pavers and getting the site at a higher grade. The company then installed a nylon fabric that water flows through but traps dirt or silt from entering. They then installed the layer of open-graded crushed stone that also allows water to flow through it easily.
Next, the crew obtained the Porous Pave product from their dealer, GeoSolutions, Inc., and was ready for installation.
“With Porous Pave, you don’t have a big cement truck show up to the jobsite,” Michael Bratton, owner of Piper Whitney Construction says. “You mix the product onsite and immediately put it into wheelbarrows where it’s dumped and installed by hand.”
Bratton says you have about 30 minutes after mixing the product to work with it before it starts to set up.
“We’re constantly mixing,” Bratton adds. “By the time the crew has bullfloated and troweled one wheelbarrow of product down, they’re ready to head back for more mix. We usually have six to seven guys on site, and that’s just to keep them from getting tired from running wheelbarrows all over.”
Crews installing Porous Pave can expect to use many of the same installation items a specialty concrete contractor would use, specifically shovels, bullfloats, trowels and a mortar mixer.
On the Nature Discovery Center Trail, Bratton says the installation on the site was a bit limited where they could move and position the mortar mixer along the 5-ft.-wide path without damaging plants growing along the sides. "It was a little fatiguing for workers walking back and forth to the mixer with a wheelbarrow over the 600-ft. length of the job," Bratton adds.
Bratton says even though installation may seem more intensive, if you have a few mortar mixers on site, you can get a lot done in a day.
“You’d be surprised how fast you can lay down the product when you don’t need to screed or compact it,” he says. “I’ve seen several thousand square feet of this product put down in a day by hand.”
Piper Whitney Construction was able to install 2,500 Sq. ft. of Porous Pave XL on this project in just under two days.
A Niche Business
Since 1989, Bratton has operated a thriving swimming pool construction business in the Houston area.
“This area has very bad soil with a lot of clay, so we started using permeable pavement wherever possible around the pools,” he says.
From there, Bratton was looking for another type of business to get in to that he was familiar with and which aligned with his sustainability ideals. He set up a separate specialty company, installing only permeable pavement and “green paving solutions,” forgoing any asphalt or concrete installation.
“We want to make money while providing a needed service with this permeable niche,” Bratton says. “Cities across the country now require permeable pavement, and it’s only growing. We’re getting in on it when it’s new and when there’s not a lot of competition with companies that specialize in this service.”
And because the color of the rubber chips determines the color of Porous Pave, it can be customized for color preference instead of just black or gray, like asphalt or concrete. Bratton says his customers really like this option, especially the red fire lanes that are attractive and able to absorb both the weight and the water loads of the ladder trucks.
“As a company, we wanted to do something that would outlive us with these sustainable solutions,” Bratton say. “With these materials, we’re able to provide a longer lasting surface for the customer to have a lifetime of use out of it. Sure it might cost more for them initially, but we’re finding that we’re having better customer relations with permeable pavement because they are happy with the product and are referring other companies to us for that same experience.”