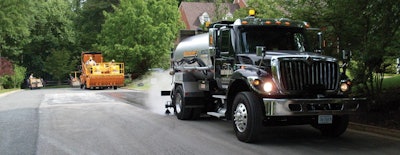
Any asset owner knows that preserving their pavement is the most important thing they can do to protect their investment. Pavement preservation methods, like chip seals, helps pavements in good condition last longer and are more cost effective than remove and replace.
A chip seal is designed to seal and protect a pavement from oxidation and weathering by sealing minor cracks in a pavement surface and preventing the intrusion of water and air. A chip seal can also be used to address raveling (loss of fines), correct bleeding and flushing problems and generally extend the pavement life.
"Chip seals can also add skid resistance," Larry Tomkins, vice president of sales and marketing at Ergon Asphalt & Emulsions says. "If we have a somewhat smooth surface, we can put a chip seal on top of that and it will increase skid resistance immediately."
While chip seals can extend the life of certain pavements five to 10 years, they are not suited for all pavements; the existing structure should be sound with only minor surface defects as they are not appropriate for rutted, potholed, or severely distressed surfaces.
"Chip seals consist of spraying a layer of asphalt on a surface and then covering that binder with aggregate," Tomkins says. "However there are different designs to take in to consideration before completing the work."
Because of the importance of chip seals as a preservation technique, a great deal of work has been done recently to move to a more engineered, technical approach. Advancements have been made in materials, design and testing procedures and application equipment. Materials improvements include the use of polymer modified emulsions, tighter specifications on the use of one-size chips, using fibers, crumb rubber additives, etc. Computerized equipment has been developed that makes placing a uniform application of materials easier and allows for simpler adjustments in progress.
The Importance of Aggregate Selection
Binder and aggregate need to come together at the correct rate in order for a chip seal to be successful so it's important to make sure you're not only selecting the right materials, but that they are also being distributed in the proper amounts.
Aggregates in a chip seal are used to resist traffic abrasion, transmit wheel loads and improve surface friction and safety. Therefore, several factors need to be taken in to consideration when choosing an aggregate for your chip seal application. Tomkins says there are six factors to consider when choosing an aggregate; Type, Gradation, Particle Shape, Cleanliness, Toughness & Soundness, and Absorption.
1. Type:
There are two main types of aggregate; natural and synthetic. Natural aggregates are limestone, granite, gravel, etc. Slag, quartzite, expanded clay and bauxite are a few examples of synthetic materials. What type you choose will depend on cost and what materials are available in your area.
2. Gradation:
When it comes to gradation, the ideal situation would be to have aggregates all one size as that will provide maximum friction and will be less sensitive to variations in binder application rates. Single size aggregates will provide uniformity when placing the binder and better drainage.
3. Particle Shape:
We want to limit flat or elongated particle shapes as they are susceptible to bleeding or excessive chip loss. Aggregates that are too round should also be avoided as they are susceptible to rolling and displacement by traffic. Angular aggregates on the other hand are not as susceptible to rolling displacement by traffic and they also lock together better.
4. Cleanliness
You want to make sure you have as clean of a rock as you can get with 1% or less passing the #200 sieve. Clean
"Dusty aggregates will prevent bonding with the binder," Tomkins says. "Any time you can limit the amount of dust you have in your aggregates, the better. If you can't limit the amount of dust, then you need to take that in to consideration when selecting your emulsion."
5. Aggregate Toughness & Soundness
The aggregates you select for your chip seal should be abrasion, degradation and polishing resistant. They should also be selected to weather freeze-thaw cycles.
"You want to consider having a Los Angeles abrasion, British Wheel or requirement in your specification that helps you make sure you have a nice tough aggregate," Tomkins says.
6. Aggregate Absorption
The final consideration when choosing an aggregate is absorption. The more absorptive the aggregate you have, the more binder that will need to be applied. Tomkins says that pre-coated aggregates may also be used to address the absorption of the aggregate.
"If aggregates are absorptive, like limestone, and I place them on top of the emulsion and it sucks up some of the binder into the aggregate, I might not have enough to keep the aggregate in place and I want to take that in to account in my design," Tomkins says. "Hot-applied chip seals usually do have pre-coated aggregates which adds a little more cost however it definitely helps out."
Choose the Right Binder
The binder or emulsion that you select will need to have good coverage, adheres to the aggregate and stays in place, and seals minor cracks. The material should be fluid yet viscous, develop adhesion quickly and not bleed when applied.
"You do not want the binder to run off the roadway when applied and you want to be able to get traffic back on it quickly," Tomkins says. "There are a few different types available and you want to select the one that will work best for your application bases on these advantages and disadvantages."
Hot Applied Asphalt Cement:
- Little to no curing period
- Quick return to traffic
- Better aesthetics by utilizing pre-coated aggregates
- High application temperatures
- Sensitive to moisture in aggregate
- Increase cost to pre-coat
Emulsified Asphalt (Cationics/Anionics):
- Lower application temperatures
- Not as sensitive to moisture in aggregates
- Pre-coated aggregates are not needed
- Longer curing period required
No matter what type of binder you choose, you need to make sure you are putting the material down in ideal conditions. Before beginning the sealing work, prepare and clean the existing surface. Fill any potholes, level the ruts and seal large cracks. Weather conditions during construction also have a direct influence on performance so the weather should be warm and dry to promote proper binder setting and curing. Make sure the surface temperature is also warm enough to accept the material. Monitor the weather forecast to avoid potential weather problems and avoid possible chip loss.
Traffic volume needs special attention once the material is placed. The traffic speed should be reduced/controlled until the binder sets, the rolling has been completed and the first brooming has occurred. Take particular care to avoid scuffing and hard braking on the new surface.
Chip Seal Design
Now that you have the proper aggregates and the right binder, it's time to put them together in a system that works.
"In years past, there have been a lot of people that have done chip seals for a very long time. They knew what worked and what didn't work," Tomkins says. "As the older generations retire, this information has not been passed down as well as it should be and the new people don't really know where to start. A chip seal design will give you a good start on what you need in terms of application rates."
If your specification doesn't have a chip seal design requirement, Tomkins says it's a best practice these days to add one.
"Just because you specify a type of aggregate or a size, if you have a range built in and they go with the smallest or largest size, that will impact the project significantly," he says.
There are two common methods for chip seal design:
1. McLeod Method
The McLeod Method is mainly used with emulsified asphalt and is based on the principles that aggregate will be one-stone thick and that there will be 70% embedment for good performance.
"We're more worried about aggregate staying in place in climates where there is snow and where snowplows could be picking up some stone," Tomkins says. "We definitely want higher embedment rates in the north whereas we may be able to get away with 50% embedment in the south."
Aggregate application rate in the McLeod Method is dependent on gradation, shape and specific gravity.
"Gradation and shape are huge when deciding how much aggregate you should place on the ground," Tomkins says.
Binder application rate is dependent on aggregate gradation, absorption and shape, traffic volume, the existing pavement condition and the residual asphalt content.
"If your traffic volume is really high, I might not put as binder out there," he says. "If I have a real porous surface, I also need to take that into account when I'm putting my binder down."
2. Modified Kearby (AASHTO Method)
The Modified Kearby Method was designed originally for hot-applied asphalt cements.
Aggregate application rate is calculated based on the dry/loose unit weight, bulk specific gravity and the board test.
"The board test is used to find the quality of aggregate on a board of known size such that full coverage, one stone in depth, is obtained," Tomkins says." A one-half square yard area is typically used and weight of the aggregate applied in this area is obtained and converted to units of pounds per square yard."
Similar to the McLeod Method, the binder application rate on the Kearby Method is calculated based on embedment depth, bulk specific gravity of the aggregate, traffic volume and existing surface condition.
Traditionally, chip seals have provided a quick, reliable and economical surface treatment that seals out water, improves rideability and preserves a pavement for years. When a chip seal is applied to a pavement in good condition, six to eight additional years of service is a typical expectation when done correctly. Technological advancements in testing and design procedures, materials and equipment have significantly reduced the dependence on experience and judgment associated with chip seals of the past. Today’s chip seal can be reliably placed on a variety of pavements under a wide variety of conditions and should be considered for your pavement preservation projects.