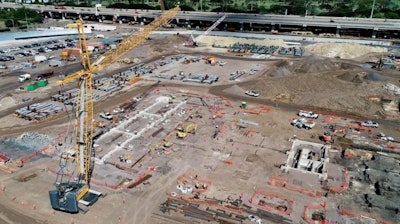
Hensel Phelps used drone surveying and Propeller’s 3D site surveys to track, map, and measure the project to demolish and replace a terminal at Honolulu’s Daniel K. Inouye Airport. The contractor has embraced virtual reality in managing airport projects, and drone data, marshalled by Propeller’s online processing and presentation platform, became the next step in updating construction status digitally and communicating work plans.
“We started using [drone data] in smaller chunks, really identifying areas we knew we were going to be working in.”
Overlaying CAD files on current project images in daily planning meetings gave crews real-life landmarks to help orient their work. (click on this image to see a larger view)Propeller
Done right the first time
By 6:30 each morning, all the superintendents, field engineers, and foremen on site would meet in front of aerial imagery and brief each other on the day’s work. “We could see real-time how the site’s changed and the different areas people are going to be working on,” said Project Superintendent Brian Holm.
The drone imagery helped operators keep people out of hazardous areas of the site, and Hensel Phelps now uses the aerial images to do better safety briefings with up-to-date visuals.
“When I’m going on a job walk, it’s pretty hard to say that you’ve walked every piece,” said Adam Cotton, regional director of safety and health for Hensel Phelps. “Propeller eliminated that risk. You’re seeing what your project is, you’re not having to physically go into situations [or] down in trenches. It gives you that knowledge without stepping foot on site.”
The Inouye Airport job team quickly learned the value of inputting layers to Propeller’s online platform in order to overlay utility drawings – existing ones to avoid and new ones to build – on current site images.
“We were able to survey in those positions prior to pavement demolition,” says Johnson. “So we had the CAD files with the location of the existing utilities, which were then able to overlay with our excavations.
The information became a new key element in issuing “dig permits,” which Hensel Phelps issues for all excavations on job sites.
“It's part of our Hensel Phelps process that we do dig permits,” says Johnson. “The document for that didn't normally include a drone image, but it did include a map of the area with utilities. Because we were able to utilize the drone flights in Propeller, we were able to overlay the existing utilities that we shot in along with the new utility installation (plan), with accurate, up-to-date drone flights as the background, which really helped communicate with the operators during that stage in the project.”
Operators can double check their location using the landmarks currently visible on the site surface.
“Obviously, we still marked them out in the field with spray paint and such, but the overlaid plans gave us an added advantage of knowing where work is at.”
Overlaying utilities drawings on site images delivered big benefits by showing Hensel Phelps significant utility conflicts. A 16-in. water main and the main power feeds for the airport cut through the site in a location that was not indicated on the drawings.
“We used Propeller to identify those impacts,” says Holm. “We had the drone snapshot and overlays of where the existing utilities used to be and where the existing utilities ended up being.”
Drone imagery was essential to safely and efficiently communicate those surprises and revise the work. It would also prove useful in addressing changes to the contract.
“If you show the owner, or anybody who isn't directly involved with all the details associated with the work, a line marked on a drone-flight image and say, ‘Hey, this is where it said it was supposed to be, but it's actually over here.’ You don't have to know a lot about the work for it to make sense,” says Johnson.
Weekly flights
“We flew just about every single week from when we started the project back in 2018,” says Johnson. “Towards the end of the week, the site started changing and by the next drone flight, [site management] would really be looking to utilize the new images in the meetings, so that they could have an accurate representation of the field when they were communicating where the work was going to be.”
Northing, easting and elevation information in the drone survey extends the value of the data into quality control.
Aerial images were amended with plan data and used extensively in coordinating work.Propeller
“Typically, we go out and survey sites for as-builts or quality control if we install a footing or utility line and we want to double check that we installed it correctly. The superintendent can overlay the utility CAD file from the contract documents on the current data set from Propeller and see that, ‘Okay, we're excavating in the area where the new utility is supposed to go. QC all good.’”
They kept discovering value
Drone data was uploaded to Propeller with ground-control points after each drone flight. The vendor is building 3D maps with the data in less than 24 hours, now. Propeller organizes the data and makes it easy for contractors to find current images, and previous images for comparisons. The 3D survey can be simplified to a 2D survey and orthomosaic photo image.
The data is available via the cloud-based interface and allowed Johnson and the Hensel Phelps crew to experiment with downloading point clouds and other ways to present and use the data.
“It's another Hensel Phelps process that we do model coordination. There's a 3D model for the building, MEP and underground utilities. So we were able to export the point cloud that was generated from the Propeller survey, bring that into our 3D BIM model. This allowed us to show our subcontractors in the BIM coordination meetings what the field conditions are in relation to the 3D model of their scope. In addition, we also utilized it to QC and efficiently plan the Hensel Phelps self-performed concrete work.”
Johnson ticks off some additional ways Hensel Phelps benefitted from drone data that the company now incorporates into its jobs:
- Initial site flights to document existing conditions prior to starting work
- Manage and monitor the project schedule
- Communicate site logistics and route planning
- Communicate to a client, such as an airport, changing road access dedicated to their operations
- Record unforeseen conditions
- Quick stockpile measurements
- Easy detailed documentation of a job from start to finish
“They are very valuable tools,” Johnson proffers to contractors considering using drones. “It was hard to see that value until we started using them. Now that we've been using drones, it's kind of hard to be without them.”
“What we’ve realized is that they [drones] are tools for conveying our plan,” says Holm. “If you understand the value of that tool and how simple it is, and use it to what it’s capable of, it’ll save you time and money out in the field.”Propeller