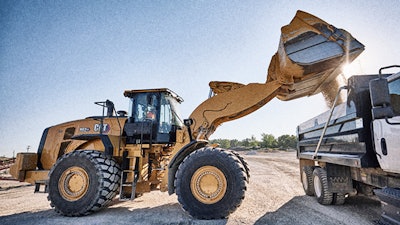
This blog was updated on 6/6/2023.
They say nothing is certain in life except death and taxes — but if you’re like many contractors, you may feel like “rising operating costs” belongs on that list, too.
Good news: There is a simple way to reduce waste, increase efficiency and get operating costs under control — and it’s readily available and easy to use on your loading and hauling equipment. Onboard payload measurement systems like Cat® Payload provide accurate, on-the-go weighing along with real-time operator feedback. Here’s how this technology can help your loader operators control costs:
1. Eliminate Unnecessary Cycles
Being able to meter the final bucket load lets operators avoid making an extra trip from the stockpile, reducing loading times and saving fuel. Because operators know exactly how much material is needed to reach the target payload weight — and can see exactly how much is in the bucket — they can quickly make adjustments to the final bucket load at the stockpile before traveling to the truck.
2. Adjust for Changing Material Weight
The volume of material in a loader bucket may look the same every time, but actual weight can vary significantly based on material density and moisture content. Wet sand, for example, can weigh almost 8% more than dry sand. Experienced operators might be able to make an educated guess at the difference in weight, but a wrong estimate can be costly.
Payload measurement eliminates guesswork. When trucks get loaded to the correct, target weight more often, that means fewer reloads or returns for top-off — which in turn translates into less time and money wasted and a more efficient overall site.
3. Lower Equipment Maintenance and Repair Expenses
Making fewer cycles to load a truck should result in less wear and tear on the loading tool. And eliminating truck overloads should decrease suspension and frame stresses, excessive transmission wear and tire wear. Studies show regularly overloading off-highway trucks results in as much as a 50% reduction in tire life.
4. Keep Overweight Fines at Bay
Simply loading wet sand versus dry sand can add almost two extra tons to the payload of a 24-ton on-highway truck — extra load that can easily result in fines. Payload measurement helps you get a payload on board that’s as close as practical to the maximum allowed for that hauling tool. It also eliminates the need to underload to avoid penalties. If you routinely underload by 10%, that means you’re using 11 trucks to do the work of 10, resulting in lost time, increased fuel usage and reduced profitability.
5. Make Better Pass-Matches
Tracking payload-per-pass data helps you make better decisions about fleet makeup and load/haul configurations. If your payload measurement data shows an operator is two-and-a-half-passing most trucks, it may pay to use a larger loader. A loader that can consistently two-pass those trucks eliminates that extra half pass — reducing time, wear and fuel usage.
Want to get a quick idea of how much payload measurement could save your operation? Just plug a few simple numbers into our Payload Calculator. You’ll get an estimate of savings per year resulting from the elimination of reloads, plus an estimated payback time for the Cat Production Measurement System.
This blog was updated on 6/6/2023.