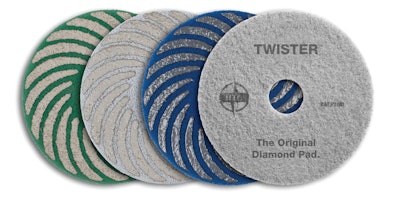
Proper ongoing maintenance of a polished concrete floor is the single most important factor in a floor owner’s long-term satisfaction with his floor. However, instead of simply providing the maintenance guidelines and technical knowledge to the floor owner and/or his building service contractor to carry out once a contractor turns the floor over, why shouldn’t the savvy contractor leverage his position with the owner to develop an ongoing revenue stream from periodic maintenance?
The advantages of this are manifold. Not only does this strategy provide for recurring revenue that requires little in the way of capital expenditure, but it also provides less tangible benefits to the polishing contractor, including:
- ensuring that proper periodic maintenance procedures are carried out by skilled technicians, as well as observing the day-to-day upkeep of the floor.
- putting the contractor in a position of trust and partnership while giving a place first in line for further work
- adding value add and a point of differentiation from other polishing contractors.
Of course, as with all maintenance programs, such a plan would have to be tailored specifically to the needs of each individual customer. The suggested ideal structure of any such arrangement would split maintenance into two tiers:
Regular or daily maintenance. Should be performed by either a building service contractor or by in-house staff. This consists of:
- Spill cleanup
- Dust mopping
- The regular cleaning of the floor with a neutral cleaner/conditioner or with a specialty soap that has compatible chemistry with the guard product
- Autoscrubbing with a diamond-impregnated, non-woven floor pad to micro-repolish the floor surface
Periodic maintenance. This is the maintenance niche contractors can fit into. It should be performed monthly, quarterly or as needed. These maintenance requirements consists of:
- Stain remediation - Contractors can repolish areas that have been etched by acidic or caustic spills with a high-speed burnisher and sequentially finer grits of diamond-impregnated, non-woven floor pads for light stains, or with sequentially finer grits of flexible-backed, hard-diamond-resin tools on a slow-speed floor machine for more difficult stains.
- Dye touch up - On a floor that has been dyed as part of the polishing process, a contractor can perform dye touch up in areas where the pigment has migrated out of the floor.
- Reapplication of guard - In areas with heavy foot traffic or under significant chemical attack, this will preserve the underlying gloss.
- High-speed burnish - Use a diamond-impregnated, non-woven floor pad for an immediate rejuvenation of gloss.
While it may be outside of many concrete polishing contractors' comfort zones to consider getting into the ongoing maintenance of the floors they create, it is worthwhile to look into. In any economic environment, but most especially in an unsure one, having steady, recurring revenue streams is of the utmost importance.
Many traditional building service contractors or in-house maintenance providers lack the technical know how, skill level or dedication to properly maintain a polished concrete floor to the satisfaction level of demanding floor owners, which creates problems for the contractor and unhappy end users as the life of the floor progresses. These two realities indicate that while it might require new ways of thinking and logistical issues to overcome, expanding into the care and maintenance of the polished concrete floors they produce makes sense for many contractors.