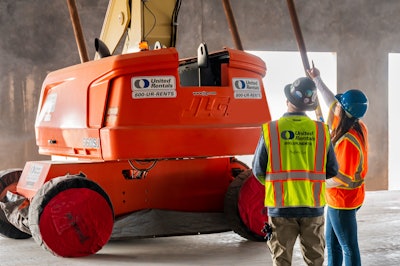
The efficiency and safety of rental providers matter customers. These factors have significant impact on their experience, affecting the condition of the equipment they rent and perhaps even the price customers pay. Being 5S certified is one way to signal to rental customers that your company is committed to operational efficiency and their well-being.
A look at 5S
5S is defined as a methodology that results in a workplace that is clean, uncluttered, safe and well organized to help reduce waste and optimize productivity, according to ASQ.
5S was pioneered by Toyota in Japan for keeping a workplace clean and organized to make it more efficient, safe and enjoyable for employees and customers. The quality tool is built on five principles: sort, set in order, shine, standardize and sustain (or self-discipline). The 5S process creates order, cleanliness and standardization in a work environment to drive safety and improve the bottom line.
To engrain a 5S mentality throughout a company, some organizations require 5S certification for employees, from upper management to service and sales support. Certification usually involves a blend of online and in-person workplace training, regular audits and self-assessments.
How 5S benefits rental providers and customers
Here are a few examples of how the 5S philosophy can be applied to equipment rental customer engagements.
Equipment ready for rent
Time is money, and downtime adds up. Customers need to have tools and equipment in good working order with zero defects. Rental companies with a 5S culture clean items routinely and perform regular preventative maintenance to ensure the items that are rented will not disappoint customers or cause delays. For example, if a customer has equipment failure during a rental, a 5S-certified vendor is more likely to repair or replace the item quickly so the company can get back to work sooner.
Enhanced efficiency
A more efficient workplace provides employees with more time to focus on customers. Equipment inventory that is organized, sorted and easy to find means less time processing an order and faster equipment delivery. Better inventory management also reduces storage space and lost or misplaced equipment—hidden costs that can impact the price of a rental.
Stress-free transactions
The rental process should never be demanding on customers. An uncluttered shop with clear signs showing where to pick up and drop off equipment results in smoother checkouts. Customers experience an easy transaction, without delays or hassles.
Safety for everyone
A clean, organized environment is safer for employees and customers. Fewer trips, falls and other accidents may reduce a rental company’s healthcare and insurance costs, providing savings that could potentially be passed on to customers. Healthy, happy employees are more likely to provide a better overall customer experience. In addition, rentals that are well maintained and checked for defects result in safer end-user experiences.
5S at United Rentals
At United Rentals, 5S is not a one-time activity to clean the shop. It is a component of the company’s “safety first and always” culture, which is instilled in every employee.
Here are some examples of how United Rentals puts 5S into action.
Sort
United Rentals removes scrap iron, used parts and other junk to create cleaner, safer shops, parts areas and yards. Because unneeded or broken items are segregated and tagged, employees can easily find equipment and tools so they can fulfill customer orders quickly and efficiently.
Set in order
United Rentals employees operate by the mantra, “A place for everything and everything in its place.” For instance, all shop tools, such as hydraulic presses, grinders and welding equipment, are put in designated places clearly marked on the floor so all shop employees know where they are. Frequently used parts, such as oil filters, may be stored in the middle of the shop versus the end, reducing the time it takes mechanics to locate and reach them. When items are “set in order,” repairs are faster.
Shine
A clean environment is a safer workplace. Keeping items off the floor, including mud and dirt, reduces accidents. Directional signs for customers returning equipment streamlines the return process. Delivery, sales and service trucks are clean, organized, stocked and checked for defects before leaving a branch to ensure they are in good condition for the customer.
Standardize
United Rentals documents its methods and procedures to maintain consistency at every location. The appearance of every branch is standardized, too. Pictures posted in the showroom and counter area define what each area should look like. Shop walkways, storage areas, tools and emergency exit routes are clearly marked. Branches are audited quarterly and annually using a 5S compliance checklist.
Self-Discipline/Sustain
5S is a team effort at United Rentals. Employees at just about every level, from senior managers to dispatchers and drivers, are committed to the process. Nearly all are certified in 5S principles using a combination of online learning and workplace training. Branch safety champions work with employees to promote safe practices and perform monthly inspections. Along with scheduled audits, these checks help maintain a culture of continuous review and improvement.
Companies that adopt a 5S culture are dedicated to the principles of zero defects, zero accidents, cost reductions and safety. Being 5S certified informs your customers that they can count on consistent, hassle-free, smooth transactions and rental-ready equipment when they need it, every time.