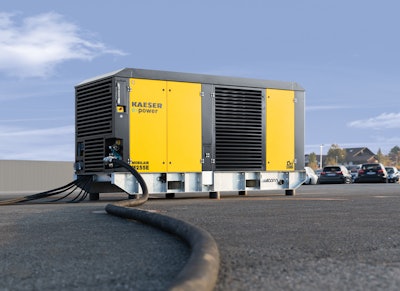
Smart compressors are another piece of construction equipment being added to the lineup of technological advances on the jobsite, which enables better performance through less work. There are several options on the market, including Atlas Copco’s smart compressors, which are designed for advanced connectivity that transcend the days in which an operator had to walk the production floor to take compressor readings and adjust parameters. They serve as one of several examples of how connectivity paves the way for easier jobsite management and monitoring, leading to greater efficiencies, reliabilities and sustainability through adaptable performance and intelligent features.
There are three main ways in which compressors have become ‘smarter,’ noted Paul Humphreys, vice president communications and branding, Atlas Copco Compressors.
“First, they offer advanced connectivity,” he pointed out. “For many people, connectivity is what comes to mind when they think of ‘smart.’ But for a compressor, the ability to adapt and optimize its operation to its working conditions might be even more important. Finally, compressors become smarter as their individual features become intelligent.”
Speaking to the benefits of smart compressors, Humphreys noted that advanced connectivity, adaptive operation and intelligent features allow compressors to boost air system reliability and efficiency.
They also offer new, remote control and monitoring options, allow for a connected production, and adapt to ambient conditions, he added.
Addressing the role smart compressors play on a jobsite, Humphreys pointed out that smart compressors adapt their performance to their operational conditions and to the air system demands.
Variable Speed Drive Technology
A key innovation is variable speed drive (VSD) technology, which goes beyond pre-set operations to enable compressors to adapt their performance to their operational conditions and to the air system demands.
“Introduced more than two decades ago, VSD still belongs in this chapter about important innovations. That’s because the technology has been refined in that time,” said Humphreys. “A VSD air compressor of the latest generation can now offer energy savings of up to 60 percent compared to fixed-speed models.”
Atlas Copco’s newest VSD compressors also feature the Smart Temperature Control system. It adjusts the oil injection temperature to the actual running conditions.
“This real-time optimization ensures maximum compression efficiency and eliminates the risk of condensation to boost reliability,” said Humphreys. “Algorithms are increasingly making the difference. The new GA VSDS, for example, comes with an intelligent Boost Flow Mode and a limp mode.
“The former lets you meet peak demand by exceeding the compressor’s maximum capacity for a certain amount of time without harming the compressor. Limp mode ensures the compressor keeps working even when something is wrong.”
On the fixed-speed side, the smart unload algorithm in the latest generation of Atlas Copco GA+ optimizes the compressor’s time to unload to reduce energy use, Humphreys added.
Even mechanical components are getting more intelligent, Humphreys pointed out.
“Smart water drains, for example, ensure the automatic removal of condensate, auto-cleaning, and the detection of potential issues. Consumable sensors continuously monitor the pressure drop in the inlet filter, the oil filter and the oil separator to optimize performance,” he added.
Remote monitoring plans such as SMARTLINK allow the operator to monitor the performance of an air compressor from a computer, smartphone or tablet.
“SMARTLINK also presents you with insights to identify opportunities for optimization. And it shows you service timelines and maintenance alerts,” Humphreys said.
Atlas Copco pointed out that management of facilities these days always involves remote monitoring and control. In the 4th Industrial Revolution (Industry 4.0), machines should be able to send information which can be analyzed by the system and the people who manage the units and is only possible if machines are connected.
Advanced Connectivity
Advanced connectivity is achieved through controllers. The Atlas Copco Elektronikon, for example, offers a host of control and monitoring options and algorithms such as customized timers and efficiency controls.
For those using more than one unit, the Atlas Copco Equalizer can coordinate up to six compressors and distribute the workload in a way that is balanced between all units or operators can choose to primarily run the newest machines to maximize efficiency. It also can set two pressure bands for different times of day, such as day and night shifts.
The Optimizer is the controller for a setting of more than six units. The device is designed to optimize the compressed air and blower system operation while set pressure and flow are being met.
It is designed to maximize energy savings and keeps units in good running condition with a proactive approach to maintenance through online monitoring. The central controller is ready for Industry 4.0, or the Internet of Things, and is designed for smart factories.
The Optimizer 4.0 compliments the efficiencies of Atlas Copco compressors and blowers by enabling multiple units installation to run with optimum pressure or flow band while prioritizing machines that will have more efficient combination.
The central controller is designed to realize the full energy saving potential of VSD units by regulating the VSD to cope with varying demand while avoiding fixed speed machines to run unload whenever possible.
Combining multiple units with the Optimizer 4.0 leads to an even load distribution among compressors and blowers to equalize their running hours, enabling planning and operation of the preventive maintenance.
Compressors and blowers operating with Atlas Copco’s central controller will have fewer load/unload cycles and operate at the lowest possible pressure/flow to extend a machine’s lifetime.
Humphreys pointed out that those running a connected production will want to know about OPC UA-enabled compressors – OPC UA stands for ‘open platform communications unified architecture’.
“In technical terms, it is a machine-to-machine communication protocol that was developed for industrial automation,” he said. “In layman’s terms, it is a universal language that allows different machines in a production facility to ‘talk’ to each other. This ensures that industrial processes run much more smoothly, efficiently, and reliably.”
Speaking to the importance of having smart compressors on a jobsite to integrate with a connected jobsite, Michael Camber, marketing services manager, Kaeser Compressors, noted that “like other construction equipment makers, some portable compressor companies offer models with more advanced controls. As technology costs for small computers and sensors declines, these controls can track and respond to more operating data.
“This information is used to ensure the equipment operates within design parameters with the goal of ensuring longer life and reliability,” he added. “In the case of diesel-driven compressors, these conditions include fuel, DEF and oil levels, motor and air end temperatures, battery voltage.”
Further, newer machines may offer options to remotely monitor equipment conditions and location via telematics services that enable access from PCs, laptops, tablets or phones from across a large jobsite, across town or in another state, Camber pointed out.
There are significant benefits in doing so.
“The biggest benefits are being able to monitor equipment operational and maintenance status,” said Camber. “These newer communications capabilities allow fewer people to manage greater numbers of assets and keep them productive with minimal manpower and interruption.”
Examples include knowing if fuel or DEF levels are getting low and being alerted to upcoming service intervals so that preventative maintenance can be scheduled at a convenient time and place, he pointed out.
Another benefit is being alerted to shutdowns or conditions that could lead to shutdowns if not addressed, and communicating the codes that enable service teams to prepare for the specific problem before dispatch, Camber added.
“It allows the asset owner, renter or even the manufacturer to monitor the equipment and dispatch service teams as needed,” he said. “Construction and equipment rental companies with fleets can better manage service scheduling, and in some cases monitor asset location. Pre-set geofencing will prevent operation of assets that have been moved from assigned locations.”
Across its entire Mobilair product line, Kaeser has been steadily advancing the capabilities of its onboard interfaces to provide more condition information and more convenient and intuitive controls, Camber pointed out.
“In particular, Kaeser's 1600CFM M500-2 oil free units driven by CAT C18 diesel engines and our brand-new e-power M250E and M255E with electric motors have these communications features,” he said.
The Mobilair M500-2 was designed to provide reliability, fuel efficiency, and flexibility, delivering up to 1600 cfm with a pressure range of 60 to 150 psig. Its 600 hp Caterpillar C18 diesel engine meets Tier 4 Final exhaust emission standards.
M500-2 is designed for heavy industrial, processing, and manufacturing operations including chemical, refinery, midstream/pipeline, food and beverage, pulp and paper, shipyards, mining, and large construction sites.
The machine can be rented or purchased to supplement plant air during peak production, provide backup for critical applications, or support annual maintenance shut downs and turn arounds.
The M500-2 features a fold-up tow bar and steerable front axle for onsite maneuvering. It also features fork pockets and lifting eyes for full flexibility. It is designed to run continuously for 12 hours without the need to refuel; the external fuel connection and external DEF tank further extend operating hours if needed.
The onboard Sigma Control Mobil is incorporated into the machinery to match air flow to meet varying air demand while maintaining steady pressure. With standard Proemion telematics and GPS/GSM-modem, operating status and maintenance conditions can be remotely monitored via laptop, smart phone, or tablet. The M500-2 can be started remotely while the geofencing feature can be used to prevent unauthorized use.
New to the market, Kaeser’s MOBILAIR M250E and M255E compressors offer the advantages of electric compressors in weatherproof, skid-mounted packages.
The fully electric M250E/M255E skid-mounted compressor is designed for outdoor operation without the need for additional weather protection. It provides 565 to 990 cfm with pressures from 87 to 200 psig, enabling them for use as either short-term or long-term rentals, back-up for industrial applications, or as a permanent installation in challenging environments.
The M250E/M255E compressors feature a compact design with lashing and lifting eyes and forklift pockets for ese of transport and placement on site.
Standard equipment includes the Sigma Control Smart offering intuitive control with maintenance reminders and real time operational data from a lockable, protected control panel.
The pressure is adjustable to suit the application’s specific requirements. Additional features include Super Premium IE4 efficiency drive motor, standard modulation control, and a built-in aftercooler with condensate separator. Internal heaters extend standard operating temperature range from 14° to 104°F.
Kaeser offers services to monitor the equipment remotely and to inform the user/owner so they can address refueling, preventative maintenance or troubleshooting and repair.
Camber sees no challenges in using smart compressors, only benefits.
“These smarter machines with communications capabilities decrease downtime, increase equipment reliability and leads to more productive jobsites,” he said. “They allow those using the compressed air to focus on doing productive work rather than babysitting equipment they may not be very knowledgeable about or qualified to tend.”
Humphreys pointed out smart compressors have the same needs as any mechanical equipment.
“They need to be serviced and maintained,” he said. “The good news is they will let you know directly when they are experiencing or about to experience problems. There is no real downside, apart from learning some of the app and controller technology if this is new to you.”