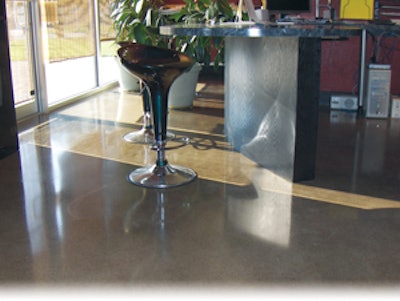
When James and Brook Schwartz, owners of CONCRETEWORKS Design out of Norman, Okla., got into the decorative concrete business in 1995, acid stain floors were all the rage. The company still specializes in that application today, but over the years as James and Brook learned about environmentally friendly products they began using more water-based and low-VOC products and materials whenever possible.
So when the couple sat down to plan their new company headquarters, they made a point to make greener choices when they could. The result is a 4,000-sq.-ft. design facility and showroom with 9,000 sq. ft. of decorative concrete on the property. The building is in the process of being certified through the U.S. Green Building Council's LEED program and through Green Globes, a green certification program managed by the Green Building Initiative.
James, who is currently pursuing a degree in architecture and who designed the building and the green aspects that went into it, says, "I didn't really do anything that different or difficult to build this building. Green construction was something I was interested in - I read about green building and took some extra steps. I would think all and all, the building cost us 5 to 7% more to construct just by going through these type of guidelines."
Schwartz says he expects to recoup that extra 5 to 7% within eight years.
The LEED checklist
The LEED system is based on points. Building certification is accomplished when a building earns a certain number of points for one of four levels - Certified, Silver, Gold or Platinum. James expects the CONCRETEWORKS headquarters to achieve a Certified rating.
When designing the building, Schwartz followed the sections in the LEED project checklist to find what he could do to earn points. For example, the first topic in the checklist is Sustainable Sites. "USGBC likes you to be situated near a certain level of density, near a community or city so employees and customers won't have to drive so far and burn fossil fuels," Schwartz explains.
CONCRETEWORKS is located within two miles of downtown Norman, there's a bus stop within 100 yd. of the building and CONCRETEWORKS offers employees bicycle parking and storage along with changing rooms and showers. In addition, Schwartz made sure to excavate only the space needed for the current building project and leave open space equal to that of the building's footprint. Choices such as these will earn Schwartz points toward LEED certification.
Another section of the LEED checklist is Water Efficiency. Schwartz hopes to earn points in that category for planting drought-resistant landscaping and setting up a system for capturing rainwater for irrigation.
Energy & Atmosphere is the category in which a building can earn the highest number of LEED points. Schwartz chose energy systems in his building that would garner him points, including radiant heat floors, CFC-free air conditioning and heat pumps. The building is also set up for wind power. "Once I switch over to wind power, my building probably won't use any utilities except for water," he says.
Under the Materials and Resources category, Schwartz hopes to garner points for using local materials, including concrete and the locally manufactured red iron steel which makes up the exterior of the building. In addition, recycling earns points in this category. "Nothing went to a landfill, everything was recycled off the project - all steel, roofing, plastics and even insulation was able the be recycled," Schwartz says. "When we're in this business we see so much construction material being thrown away. Being able to recycle is something that's really important to me."
Schwartz took advantage of several opportunities for points in the Indoor Environmental Quality category, including the utilization of day-lighting. Carbon dioxide monitoring, use of certified lumber, choosing environmentally friendlier versions of gypsum board and drywall, and utilizing low-emitting sealants, adhesives, paints, coatings and so on also helps gain points.
Schwartz says that he'd like to see more people use the LEED guidelines to see what changes they can make in their work processes to create a more environmentally responsible company, even if they don't go through the process of having a job certified.
"What I learned through following these LEED guidelines is just how to be more responsible on a jobsite. When you leave a jobsite you don't leave your trash there, you take it with you. If you've got solvents you don't take them to the dump you secure them and have them safely collected and disposed of properly," he says.
A decorative 'LEED'
The CONCRETEWORKS design facility and showroom includes 9,000 sq. ft. of decorative concrete. Schwartz plans to earn points through the decorative work on site through a local materials credit and by using polished concrete and water-based sealers and stains.
Schwartz says polished concrete, in which a contractor grinds rough concrete with a planetary grinder using a series of diamond disks generally from 100 grit up to 3,000 grit, is going to be a big part of green building for the decorative industry.
"When it comes to interior spaces, I see the green building movement pushing a lot of polished concrete," he predicts. "Number one, you don't have to maintain it with acrylic-type sealers all the time. It's a tight surface so it's smoother and is a little cleaner to maintain. And the products used in polished concrete are densifiers, not top coats or sealers, and the densifiers are (non-petroleum) oil-based and much more environmentally friendly."
Schwartz adds the water-based products will also play a major part in the green building movement. "In the last year or two, manufacturers have produced some pretty savvy water-based stuff," he says. "We all got bit about a decade or so ago with water-based - it just wasn't durable. But that's changing."