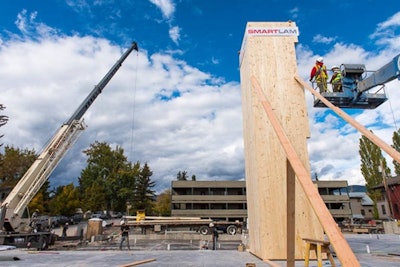
History’s timeline of structural innovations – from ancient Roman aqueducts to cathedrals with soaring rooflines, castles to neighborhoods of mass-manufactured buildings – reads like a primer of Buildings 101. Each has helped us refine our construction methods and building efficiencies, but over time that progress has cost our planet precious resources.
Typical structural building components like masonry, concrete and steel have large carbon footprints and require great amounts energy to produce. Concrete production alone represents roughly 5% of world carbon dioxide emissions, the dominant greenhouse gas. Weighted with data from the US Green Building Council that 40% of national CO2 emissions come from buildings, it is more than clear that we must re-examine our go-to for construction materials.
Rather than reinvent, though, consider a return to our construction roots. A product called Cross Laminated Timber (CLT) has been used in Europe for a couple decades now, and has proven to be a green alternative to traditional “industrial age” building materials. This engineered wood building system is made from several layers of solid lumber boards, stacked crosswise and bonded together, providing dimensional stability, strength and rigidity.
One great example of how CLT saves on time and money with a reduced carbon footprint can be found in Whitefish, Montana. A multilevel building currently under construction selected a CLT elevator shaft. If the construction team was using concrete masonry units (CMU), the common and traditional method, they would have to budget for a process involving 8-12 people, several inspections, added equipment to stack and cure the shafts, and allow 3 weeks for the entire process. Compare that to a CLT shaft, prefabricated in the SmartLam facility with zero impact from weather conditions, that can be assembled on site with just 3 people and a crane operator in just a matter of hours. The cost of a CLT modular structure is in the neighbourhood of 70 to 75% of conventional methods and saves nearly 3 week’s time in the overall project schedule.
Replacing concrete and steel with wood as a building material can have a significant impact on reducing greenhouse gas emissions. Starting with the product source, wood is the only structural building material with third-party certification programs in place to verify a product’s sustainably managed origins. At SmartLam, we procure all of our lumber from sawmills practicing certified sustainable forestry practices.
Wood building systems like CLT also bring the advantage of low embodied energy. Embodied energy refers to the energy needed to extract, process, manufacture, transport, construct and maintain a material or product.
For green building, wood is an obvious choice. Unlike other products that deplete the earth’s resources, wood is the only major building material that grows naturally, is renewable, and requires less energy to produce. In fact, wood is the ONLY renewable building material. Using CLT in place of the old standards like steel or concrete is one way to reduce the environmental impact of your structure without compromising on the advances we’ve made in modern structural integrity. It’s a solution for the future.
Casey Malmquist is the President and General Manager of SmartLam. For more information visit www.smartlam.com