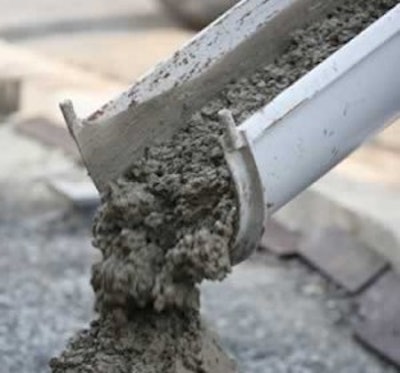
Cement is everywhere. The foundations of our buildings, the driveways that lead beyond suburban garage doors, the walls of our schools, and the mortar joints between every brick we lay contain a binding substance we call Portland cement. Cement is the binding agent used to hold together the tough aggregate (rocky gravel) in the concrete we can use for just about everything in modern construction. It seems harmless enough. We don't have to cut down trees to build with it. It isn't particularly full of toxins, and is incredibly durable and long lasting, but the environmental cost of concrete is astronomical.
The basic process for making cement heats limestone (calcium carbonate or CaCO3) in a kiln to well over 2550F. This process not only requires enormous amounts of fuel, but also releases literal tons of CO2 as it separates the limestone into its constituents, lime and carbon dioxide. The manufacture of cement releases a terrifying 9kg of CO2 for every 10kg of cement produced, but if building with wood is not as strong or durable and involves all the sticky business of cutting trees and building with concrete is nearly an environmental abomination. What is the world to do?
Our hope may lie with Brent Constantz and his California company Calera. Calera is creating cement that actually reduces the amount of CO2 put into the air by power plants. Their location, across the street from a major Californian power plant, siphons smoke stack emissions from the power plant, runs the gas through oil rig or brackish water, and the salts and minerals from the water bond with the carbon dioxide in the gas to precipitate out limestone in much the same way that mother nature does it. What he gets is cement, hard aggregate for making concrete, and water that is already a step toward being purified for drinking thus reducing the time and energy needed to return it to a potable state. The cement can be used just like Portland cement, for new buildings or even just patch jobs.
The process is actually quite complicated, but at its heart is the same thing that happens naturally over millions of years to produce the limestone we use for all of our building needs. Constantz claims that for every pound of CO2 produced by the production of regular cement, his process removes three. Will the process be as elegant and efficient when operating at full scale? Is the cement really the same as our time-tested Portland cement? Will it be affordable? Calera insists "yes" is the answer, but only time will tell.
Calera is expanding its production and preparing to subject its products to concrete industry scrutiny. Meanwhile the energy sector, environmentalists, and polar bears alike all hold their breath hoping for a happy conclusion to the story. Cement may eventually become the new boom in green building materials, but we're a long way from knowing just how this battle is going to end. Super green or not, Calera has to demonstrate that this process for producing cement is practical and affordable to be able to be competitive in the concrete industry, and that will be the true test that determines whether or not green cement is real or just a dream.