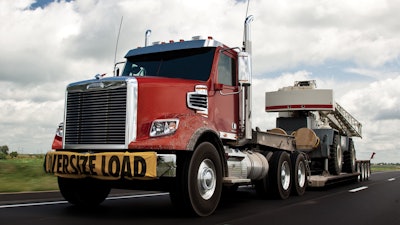
When spec’ing a heavy haul truck there is no single best solution. The weight of the load, distance traveled, amount of time spent off road and a host of other factors determine the proper choice.
“Heavy haulers that transport loads above 120,000 lbs. gross combination weight (GCW) must carefully specify their trucks for both durability and power,” says Patrick Dean, Kenworth chief engineer. “An over-spec’d truck may reduce fuel mileage and increase acquisition costs while an under spec’d truck may not be sufficient to move the load, or may increase maintenance costs. The challenge is to achieve the right balance between the truck’s job requirement and expected annual mileage to help produce the lowest operating cost per mile.”
Weight and terrain are driving factors. “First ask what is the weight you are going to be hauling and over what terrain,” says Chad Semler, director of product marketing for severe service, Navistar. Different loads and varied geography make it difficult to suggest a generic heavy-haul spec.
John Felder, Volvo Trucks North America, says, “The load will determine the number of axles in terms of configuration and capacity, truck suspension, engine, gearbox, driveline, braking capacity and truck frame strength. Another consideration is the location of the operation in terms of on-highway/off-highway ratio, terrain and geographic factors.”
Different weight levels require different components. “There are a number of levels of heavy haul applications,” explains Dean. “The first is 120,000 to 140,000 lbs., which can be met fairly easily with normal components. The next level is 140,000 to 180,000 lbs., which is more expensive, but nothing specialized. The 180,000 to 240,000-lb. level starts requiring dedicated components to do the job. The 240,000 to 330,000-lb. level requires planetary axles and an auxiliary transmission. As the GCWR goes up, vehicle speed comes down and the price of the chassis goes up dramatically, in some cases three to four times what a 120,000-lb. tractor would cost.”
Balance startability and top speed
Different loads and varied geography make it difficult to suggest a generic heavy-haul spec. You really need to understand your load and the terrain you will be hauling it over.
“We prioritize and optimize the powertrain first when spec’ing a truck,” says Brain Daniels, severe duty product manager, Freightliner Trucks. “This includes everything from the driveline, axles, transmission and engines. A good starting point is the desired road speed and startability. Knowing where and how a customer plans to operate a vehicle is essential in optimizing the powertrain. Freightliner’s powertrain partner, Detroit, has dedicated technical resources (TSRs) located in each region in the U.S. and Canada to ensure all of the requirements above are considered and optimized.”
GCWR impacts driveline selection and the torque capabilities of drivelines. Dean explains that the driveline serves as a fusible link, protecting the expensive items like transmissions and rear axles. “Drivelines must be capable of transmitting the torque required to do the job, though, so often, up-sizing drivelines is required in these applications. Most heavy axles rated 46,000 lbs. or higher are capable of some high GCW ratings, but gear ratios and transmission selections are key to finding low-enough gears to pull the heavy loads up grades as well as achieve top speeds as required to haul on the highway.”
Components need to be properly rated. “The rear axle configuration of the truck will need to safely support the weight placed on the fifth wheel,” explains Felder. “Then it is time to move the load down the road where the driveline torque requirements are addressed. Determine the maximum engine torque you can transmit through the transmission gearing and axles. Consideration and analysis of the terrain and geography needs to be performed because each will affect driveline torque. It’s important to balance engine power and driveline in terms of torque and road speed, where the top speed can be calculated. The tradeoff when spec’ing the driveline is to have an unloaded truck capable of highway speeds to get to the next job.”
Technology now makes it easier to perform the necessary calculations. “We now have programs where you can input your desired speed, your grade and your load and it will help you determine an optimum range of gear ratios,” says Semler.”
Make sure you understand the trade-offs with any decisions. “The rear axle ratio choice will affect startability, but choose it carefully to ensure a good balance between cruise speed and low gearing,” says Dean. “Kenworth recommends a startability of 15 or 20% for most heavy-haul applications. You typically don’t want to spec anything faster than a 4.11:1 ratio unless you are running a two-speed rear axle or an auxiliary transmission. In extreme applications involving bridge decks or oilfield equipment, you may see ratios upwards of 10:1 or even 14:1.
“For haulers running long distances at highway speeds, that ratio chosen should be as low as possible without undermining startability,” adds Dean. “As a rule of thumb, pick the rear axle ratio for efficiency on the highway and get the startability required from your transmission ratios.”
Prevent off-road slip
The ratio of on-highway versus off-highways use will have large influence on how you spec a truck. Automated Manual Transmissions (AMTs) are changing the equation with Mack claiming its 13-speed AMT offer startability and favorable on-road axle gearing.
“Kenworth recommends wheel differential locks or a cross lock on at least one drive axle,” says Dean. Automatic Traction Control is an option on antilock brake systems that control wheel spin on slippery surfaces, which can be a big help when stating a load on a muddy jobsite.”
Mack axles come standard with an interaxle power divider. “Automatically it will shift up to 75% of the power to the axle that has traction,” says Tim Wrinkle, Mack construction product manager. “There is no button to push, it does it on its own. There is also available inter wheel from side to side. You can do that as well if you are losing traction on one particular wheel and it will apply up to 75% of the power to the other one. We also have the differential lock available; if you are stuck you can lock those axles and walk out.”
Keep wheelbase short as possible
Don’t make the truck’s wheelbase any longer than necessary because it reduces maneuverability, which is critical for heavy haul tractors that need to negotiate crowded job sites.
“The desire would be to target the shortest wheelbase possible to maximize maneuverability while still meeting and federal or local regulations,” says Daniels.
“There are several advantages and disadvantages to longer and shorter wheelbases,” says Semler. “In tractors, a longer wheelbase may be desired for spreading the load. A longer wheelbase may also be required for accessories or additions you are going to have on the truck, such as headache racks, toolboxes and lift axles for added capacity. But a longer wheelbase does reduce your maneuverability and turning radius. A shorter wheelbase with a setback axle is your most maneuverable.
“Generally, you will get more front axle loading with a setback axle and a shorter wheelbase,” says Semler. “That may cause issues if you are off road in the soft soil. You want to keep your loading pretty equal so you don’t cause sinking in soft soil.”
Bridge laws and other legislative requirements need to be considered when spec’ing the wheelbase. “The tradeoffs to be balanced are the laws, application requirements and maneuverability,” says Felder. “Steerable lift axles may help balance the tradeoffs.”
An over-spec’d truck may reduce fuel mileage and increase acquisition costs while an under spec’d truck may not be sufficient to move the load, or may increase maintenance costs. The challenge is to achieve the right balance between the truck’s job requirement and expected annual mileage to help produce the lowest operating cost per mile.
Proper positioning of the fifth wheel is also critical to ensure full use of the rated capacity of all axles, especially the front.
Wider tires can help handle heavy loads and meet certain state requirements but come with a maneuverability penalty. Certain heavy haulers need wide-aspect front tires not only to handle the load, but also to meet some state’s tire-width requirements. “The rule is typically 600 psi of tire width, but it can be as low as 500 psi width,” says Dean. “Mounting 425/65R22.5 tires on the front will be good for up to 22,000 lbs. on the steer axle in most states. You can go to wider 445 section tires to maximize tire width and improve flotation over loose surfaces.
“Heavy haulers often find themselves on jobsites maneuvering at slow speeds, which places a lot of pressure on the steering system” says Dean. “This creates cooling concerns. Kenworth recommends an oil cooler on the steering system to maintain safe operating temperatures under demanding conditions.”
Engine considerations
Traditionally most heavy haulers use a 15-liter engine. But the truck industry as a whole has been ‘right-sizing’ engines for the specific demands. “In 2009, 56% of all the U.S. Class 8 trucks had engines of greater than 13 liters,” says Wrinkle. “Just last year in 2016 that was already reduced to about 40% for the entire Class 8 industry.”
As power densities have increased, the 13-liter engines now cross over ratings of many larger 15-liter products. “The industry is recognizing that you can do these heavy hauls with a 13-liter engine that you couldn’t do many years ago,” says Wrinkle. Mack claims its 13-liter MP8 is able to deliver big block power and durability. “It is up to 505 hp and 1,860 ft.-lbs. of torque.”
Freightliner trucks also offers 13-liter engines with up to 505 hp, but concedes that customer needs continue to drive their engine offerings. “We recognize that many heavy haul applications still require larger displacement and big torque to handle the task,” says Daniels. “We continue to offer customers a broad range of 13-, 15-, and 16-liter Detroit engines with up to 600 hp and 2,050 lb.-ft. of torque.”
Gear for success
“Heavy haulers typically choose an 18-speed manual or automated manual transmission (AMT) because of the super low ratios and close gear splits,” says Dean. “Allison automatic transmissions are also becoming popular with heavy haul customers, both for ease of operation and the initial torque multiplication provided by the torque converter. Two popular examples are the 4500RDS and 4700RDS.”
Two- and four-speed auxiliary transmissions and two-speed axles are needed for the heaviest loads. “In both cases, they double the number of available ratios, allowing improved startability and driveability,” says Dean. “A two-speed auxiliary transmission will double the reduction, while two-speed rear axle will increase the reduction by a third. A two-speed axle works well up to about 190,000 lbs. GCW. Above that, Kenworth recommends an auxiliary transmission with a 52,000-lb. tandem to give a GCWR of 240,000 lbs.”
AMTs are gaining popularity in the vocational market just as they have in line haul. “We offer Eaton MHP, MXP and VXP transmissions which have very high GCW specifications,” says Semler.
Volvo Trucks recommends its Volvo I-Shift AMT for heavy-haul trucks. “Powertrain integration and smoother shifting algorithms will reduce driveline shock,” says Felder. “The 13- or 14-speed Volvo I-Shift with crawler gears is a solution for GCW loads up to 220,000 lbs. The deep reduction of the crawler gears provides excellent startability, which reduces the need for a higher axle ratio. This allows a faster rear axle ratio to be paired with the I-Shift with crawler gears, bringing greater fuel efficiency to vocational and heavy-haul when at highway speeds by lowering cruise rpms. Volvo’s heavy-haul software package optimizes shifting for high GCW applications, allowing shifting to occur at higher revs, and enabling drivers to control downshifts.”
Mack has tailored its mDrive HD for heavy haul applications. “The mDrive can go up to 220,000 lbs.,” says Wrinkle. “We have specific software and shift modes for heavy haul. The engine, the transmission and the axles are all tuned together.” For instance, the Heavy Haul shift mode makes more aggressive shifts and with less skipping.
The startability and steps between gears of the mDrive HD 13-speed with creeper gear matches up favorably with an 18-speed transmission. The 13-speed mDrive offers a 17.5:1 low ratio. “With a standard transmission, typically a low would be around 10:1 and a low/low would go down to 14:1,” says Wrinkle. “With an 18-speed transmission there is about a 20% gap between each gear shift. So when you make that shift you are dropping about 250 rpms. It works, but that is a lot of gears to shift through.
“Ten-speed transmissions, on the other hand, have a 40% step between those gears, and that rpm drop is going to be 500 when you are shifting between them,” says Wrinkle. “So when you have a big, heavy load and you need to keep that momentum up, that rpm drop is hurting you in performance and efficiency.”
The 13-speed mDrive splits the difference. “It has about a 28% step in between the gears and it is automated so your foot is not having to do the clutch,” says Wrinkle. “The computer can do it a lot quicker than humans, so you are not losing those rpms and you are getting a lot better performance.”
Support the load
“Freightliner’s focus on Real Cost of ownership targets optimizations such as minimizing additional weight to a vehicle,” says Daniels. “Double frame rails are not necessary but are preferred by many of our heavy haul fleets for added durability on longer wheelbase vehicles. Load distribution and application (off road) are factors considered with frame specifications. Additional considerations for added strength would be axle or suspension related items.”
The amount of frame reinforcement will depend on the truck’s wheelbase and axle capacities. “An inserted 3/8-in. frame is usually required for most heavy haul tractors, but you can get two inserts,” says Dean. “The longer the wheelbase and the more axle capacity you add, the more rigid the frame needs to be.”
“Many people think they need a double frame rail regardless and they may not,” says Semler. “It depends on the fifth wheel load on the tractor. You may have a high GCW, but you don’t have that huge load on the fifth wheel. Most of it is back on the trailer. If you do have a very high fifth wheel load you may require a double frame.”
In some cases you may want to consider alternatives to a standard light weight frame. “There is the option of a taller single frame that gives you more strength without the weight of a double,” says Semler. However, you have other give and takes. As you go to a taller frame you have a higher fifth wheel, so you have a higher ride height for your trailer.”