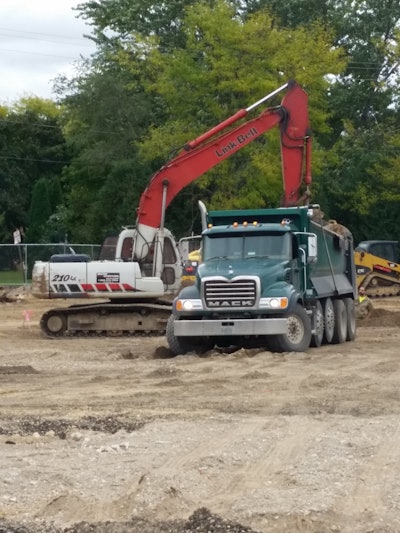
Modern trucks are packed with technology that helps monitor system health. “To maximize vehicle uptime, take advantage of the electronic monitoring systems available on vehicles today, like tire pressure monitoring systems, preventive maintenance (PM) schedulers and telematics reports that notify you of key fault codes that could provide advanced warning of a potential failure,” says John Crichton, director of fleet service, Navistar.Tires, brakes and lights should be checked as often as possible, and always during any type of maintenance activity. It is a good practice to set cut-off limits, such as when tires must be replaced.Staff
You should also perform daily walkarounds to identify potential trouble spots. “Daily walkarounds are commonly used to look for lube or coolant leaks, but it’s also important to listen for air leaks,” says Ray Hasting, Mack Trucks director of e-mobility and national vocational accounts. “Air leaks can be occurring at several different locations, including airline fittings, a bypassing brake valve, a loose exhaust clamp or a cracked exhaust flex pipe.”
A pre-trip inspection is a must for vocational commercial trucks. It is a CDL requirement and should be documented. Develop a list and routine to ensure critical items are not missed. When you approach the truck, check underneath to make sure there are no fluid leaks. Make sure the truck is not leaning or listing in a certain direction.
“Lights and tires are two big issues a driver can monitor that will increase uptime,” says Tom Bray, senior business industry adviser for J. J. Keller & Associates. “The downtime difference between having to fill a tire and replace one is significant, and the consequences of a required light being out can be serious. As an example, no right rear turn signal can result in someone trying to pass the truck on the right when the driver is trying to turn right.”
The worst place to discover a problem is on the road. “Tires, brakes and lights should be checked as often as possible, and always during any type of maintenance activity,” notes Bray. “A company should be scheduling safety inspections at least often enough that issues with these components are found in the shop and not on the road.”
Also make sure drivers understand how new technologies work to prevent unnecessary downtime. “When ordering new equipment, research the enhancements that have been made to the vehicle safety technologies, such as predictive cruise control and lane keep assist and other options that alert drivers when they need to be aware of a pending hazard,” says Crichton. Then, educate your drivers so they understand the changes and technology updates that have been made to the trucks and how the different systems work.
“For example, we have seen drivers bringing trucks in with a complaint of ‘low power’ only to find out that the monitoring system reduced the speed of the truck because the driver was driving too close to the vehicle in front of him,” says Crichton.
Take a proactive approach to DOT inspections. Most FMCSA violations can be avoided. Some of these include lights, tires, bolts, couplings, visible suspension conditions, exhaust leaks and visible mechanical concerns. Even a simple oil leak can result in an out-of-service order. The most common mechanical reason that DOT inspectors place a commercial truck out of service is due to braking system-related items. This is followed by tires and wheels.
Brakes Deserve Close Attention
The DOT brake inspections catch many issues overlooked during regular maintenance. “Many of the critical issues flagged during these inspections are maintenance related, and many are issues that could have easily been prevented with regular, thorough maintenance procedures,” says Fred Andersky, Bendix Director - demos, sales and service training.
Pre-trip inspections are a good starting point. First, look for visible brake system problems such as loose hoses or damaged brake components, including air chambers or push rods.Brakes, followed by tires and wheels account for the most common reasons commercial trucks are placed out of service during DOT inspections.Staff
Since brakes are critical to uptime and safety, it’s essential to inspect as often as possible. “Do a quick inspection when the vehicle is in the shop, even if it is not for a brake issue,” advises Kevin Pfost, technical service, Bendix. A quick visual check can prevent future problems. “Make sure all brake chambers have the rubber plug properly installed in the caging bolt hole to keep contaminants out of the chamber.”
While in the shop, Bendix recommends air brake inspections include the following:
- Conduct a 90- to 100-psi brake application and listen for leaks
- Measure chamber stroke at each wheel end to ensure proper brake adjustment
- Examine friction material for good condition and minimum thickness
- Measure/inspect each rotor and drum for wear and heat cracking and/or leopard spotting
On an air brake system, the slack adjuster is used to adjust the brakes. It takes up the slack in the stroke as the friction surfaces wear away. Modern trucks are equipped with automatic slack adjusters that adjust themselves during full brake applications, and should only require manual adjustments during installation.
“Always follow the manufacturer’s guidelines for slack adjuster operation and troubleshooting,” says Pfost. “When backing off a Bendix slack adjuster, it could take up to 70 lbs.-ft. to back off. Leave the wrench on the adjuster nut or mark the nut and slack adjuster body and cycle the brake a couple of times to see if the wrench turns in the clockwise direction. This will tell the tech if the slack is adjusting properly. If there is no resistance when backing off the slack, the slack adjuster is bad and should be replaced.”
Don’t Ignore Aftertreatment Systems
One of the most common reasons for mechanical downtime with today’s modern diesel trucks is a failure in the engine aftertreatment system. “The engine aftertreatment system is the most overlooked maintenance item, and its exhaust gas recirculation (EGR) system is often the most overlooked component of the aftertreatment system,” says Ray Hasting, Mack Trucks director for e-mobility and national vocational accounts.
Again, a proactive maintenance approach prevents unnecessary downtime. “The EGR system’s performance can be significantly improved through regular cleaning and pressure testing,” says Hasting. “The EGR cooler lowers the temperature of the exhaust gas before it reaches the engine’s air inlet. Cooling the gas maintains low intake air temperature, which adds to overall engine efficiency. Low temperatures make the exhaust gas denser, so it occupies less space. The gas then displaces a smaller amount of oxygen, which helps maintain combustion efficiency and a leaner air-fuel ratio.”Daily walkarounds should include checks of all critical fluids as well as condition checks to identify leaks or damaged/missing components.Staff
Other overlooked components include the air dryer and diesel exhaust fluid (DEF) pump filter. “The aftertreatment system uses air to purge fuel from the diesel particulate filter’s (DPF’s) hydrocarbon doser,” says Hasting. “Proper maintenance of the air dryer cartridge improves the aftertreatment system’s performance because it operates best when the air is dry. The DEF pump filter has an annual replacement interval that is often overlooked. The inexpensive DEF pump filter will improve performance of the SCR system and extend the life of the more expensive DEF pump.”
Also remember that engines need clean air and oil to maximize efficiency and longevity. “The lubrication and air intake system preventive maintenance practices are critical based on the severity of failures when both are not properly completed,” says Hasting. “Brake system, steering system and suspension system PMs are critical because of the safety implications.”
Establish a Tailored PM Program
Each vocational application is different, so a tailored PM program can be a good place to start.
“Systematic preventive inspections should be done regularly, not once a year (or every 90 days) when required,” advises Bray. “A good pattern I have seen used is a safety inspection of critical components (also referred to as a PM A, or preventive maintenance, schedule A) done weekly, bi-weekly or monthly, depending upon the service the vehicle is seeing. A PM B, which is a more in-depth PM inspection (and an oil change and lube), is then done in place of every second or third PM A. The PM B inspections are close to doing the periodic (annual) inspections required under the California 90-day inspection requirement and FMCSA’s periodic (annual) requirement.”
Establish a PM schedule and modify as necessary. “If your maintenance inspections are finding issues, this is telling you that you are not seeing the vehicles often enough or you are using cut-off thresholds that are too close to the limits,” says Bray. “Also, part of any PM program includes driver involvement. Training drivers on thorough pre-trip, en-route and post-trip inspections and following up the training with tracking is how you get the drivers involved. Immediately addressing any vehicle issue a driver points out following an inspection is how driver buy-in is secured.”
OEM recommendations serve as a starting point. “The more detailed the inspection, the greater the opportunity for enhancing vehicle uptime,” says Hasting. “Also, inspection results should be reviewed regularly to ensure they’re adding value and should be adjusted as needed, with a focus on maximizing vehicle availability.”
Start with the maintenance schedule recommended by the original equipment manufacturer and modify it to match your operation. “As an example, with trucks that are spending an excessive number of hours alternatively idling and working hard at worksites, you might want to reduce the mileage between inspections and maintenance accordingly,” Bray advises.
Make a checklist for all your maintenance inspections and other scheduled activities. “These serve two purposes,” says Bray. “First, they let the person doing the inspection and/or maintenance know what to do and what to look for when it comes to components and condition. Second, it documents the condition of the vehicle before and after the maintenance activity. This data can then be used to update the maintenance schedule, time allotted for maintenance and future equipment maintenance decisions.”
Finally, on your checklists, you want to include realistic cut-off limits for components. “As an example, you can use a tire until its tread is 2/32 in. on a drive axle,” explains Bray. “However, if you release a vehicle from the shop with exactly 2/32 in. on it, the tire will fall below the minimum before it’s back in the shop again.
“To paraphrase an old TV commercial, when it comes to maintenance, you either pay a little now or a lot later,” he continues. “Everyone has heard the argument for having a systematic and preventive approach to maintenance. It increases uptime; reduces costs by preventing expensive on-road repairs; reduces losses due to unscheduled downtime; prevents roadside inspection violations and out-of-service orders during roadside inspections; helps defend litigation following a crash; and improves driver morale.”