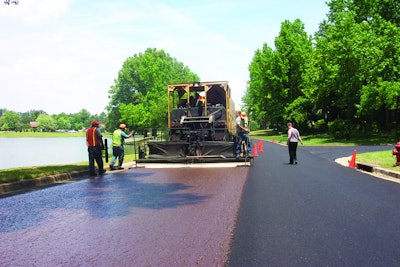
An independent standards development organization has verified the findings of an eco-efficiency analysis (EEA) of asphalt pavement technologies, which shows microsurfacing to be more economical and to cause less environmental impact than mill & fill.
NSF International, a not-for-profit, non-governmental organization that develops national standards and provides third-party conformity assessment services, has verified a report submitted by BASF Corp. detailing the methods and findings of its “Micro Surfacing Eco-efficiency Analysis.”
Microsurfacing vs. Mill & Fill
The BASF EEA compares total life cycle environmental impacts and costs of a 2-in. mill & fill asphalt overlay with those of a cold mix, polymer-modified asphalt emulsion-based microsurfacing, with a defined customer benefit as a goal. For purposes of establishing a common unit of comparison between the alternatives, the customer benefit is developed and defined as the pavement preservation of a one-mile stretch of a 12-ft. lane on an urban road using the two technologies to produce similar profiles and performances over a 40-year period.
Microsurfacing is a pavement preservation method employing cold mix slurry made on the job site by mixing aggregate, mineral filler such as portland cement, water, and a polymer-modified asphalt emulsion. The polymer used for the analysis is styrene-butadiene-rubber (SBR) latex. Suitable for heavily traveled roads, microsurfacing can accept traffic in an hour, and is used for wearing courses, leveling surfaces and filling wheel ruts. For the analysis, International Slurry Surfacing Association (ISSA) quantity guidelines, i.e., 20 pounds of material per sq. yd. for wheel rut filling and 25 lbs. per sq. yd. for surface treatment, were used. Microsurfacing was assumed to have a durability of six years.
Mill & fill consists of removing existing surface pavement with a milling machine and hauling the milled material to a storage site. New asphalt plant mix, often containing some recycled asphalt pavement (RAP), is installed to replace the milled out material. The EEA assumed RAP content to be 10% for the primary study case, but also examined another scenario where 40% RAP was assumed. A 2-in. compacted depth was assumed for the overlay with a durability of 11 years. At a thickness of 2 in., mill & fill is considered a structural pavement fix. The EEA also studied a second scenario, one assuming a durability of 17 years for the same thickness.
Life Cycle Costs
The life cycle costs analyzed in the EEA were those occurring in manufacture, delivery and installation of each product over the life cycle of the road together with disposal costs. The study considered the time value of money and calculated the net present value of all future costs.
In general, mill & fill uses about 2.5 times as much aggregate, and more than twice as much asphalt binder, than microsurfacing in order to produce the same customer benefit over a 40-year life cycle. These facts contribute to the finding that microsurfacing has the lowest overall material and labor costs. Life cycle costs for microsurfacing were more than 25% lower than mill & fill despite the fact microsurfacing lane striping costs were higher due to more frequent applications. The accompanying table shows the component costs:
Insert mill & fill chart
The Environmental Burden
The EEA examination of life cycle environmental impact, or “environmental burden,” concluded these findings:
Energy and Resource Consumption: Since mill & fill requires hotter production and application rates and uses more asphalt and aggregate than microsurfacing, microsurfacing consumes about 40% less primary energy than mill & fill over the life cycle. Even when considering the use of RAP in the asphalt mix overlay, the study found that microsurfacing uses over 50% less resources by mass.
Air, Water and Solid Waste Impacts: Greenhouse gasses (GHG), which trap heat in the atmosphere, include carbon dioxide and methane entering the atmosphere primarily through the combustion of fossil fuels such as oil, natural gas and coal. The highest carbon fingerprint determined in the EEA occurred in the mill & fill alternative, with microsurfacing GHG emissions lower by almost 45%. It was higher for mill & fill because that alternative requires over twice the amount of material to be shipped to and from manufacturing and job sites.
With regards to water emissions, microsurfacing has the highest critical water volume requirement, attributed primarily to the manufacture of lane striping materials. Excluding the impact of road markings, the remaining water emissions for each alternative are about the same.
Solid waste emissions included those from municipal, special, construction and mining wastes. They are principally the result of sending materials to landfills for disposal. Even when considering the perpetual use of RAP content, the study finds that mill & fill still has the highest impact in this category due to the much greater quantity of materials.
Land Use: With respect to the impact caused by the two technologies on the biodiversity of our ecosystems, the EEA found that energy required to produce and apply mill & fill is the largest contributor to land use. Mining wastes as generated from aggregate production, as well as solid waste disposal of unrecycled materials, also contribute to the impact on land use.
Summation of EEA Findings
Evaluating the individual environmental impact categories, the EEA finds that mill & fill has the highest environmental impact on a weighted basis in all main categories. Microsurfacing performs best in all main categories on a weighted basis because it requires less than 50% of materials than that for mill & fill, while maintaining the desired customer benefit.
Furthermore, although applied more frequently, microsurfacing scores lowest in resource consumption—the most relevant environmental impact for the study—because of its significant reduction in the amount of binder and aggregate used. This materials reduction also benefits micro surfacing in toxicity potential and risk potential.
Microsurfacing also scores lowest in energy requirement—the second most relevant environmental impact—because of its lower overall consumption of asphalt binder, lower manufacturing and application temperatures, and reduced logistical impacts due to shipping less material to and from the job site.
Tim Harrawood, manager of Vance Brothers Inc. and past president of the International Slurry Surfacing Association, was a member of the study group that prepared this report. This is a synopsis of the overall analysis. The full report is posted online by NSF at
http://www.nsf.org/business/eco_efficiency/Micro_Surfacing_EEA_Study_Verification_Final.pdf.