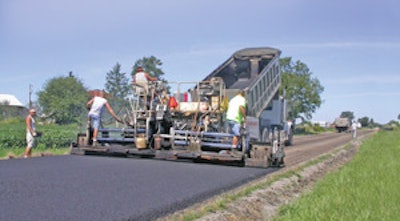
Much of the almost two million miles of asphalt roadways in the United States are severely distressed and in need of repair or replacement. Over the last few decades increasing traffic demands combined with decreasing funding for repairs, environmental concerns and an emphasis on safe, efficient, transportation systems have stimulated research and field demonstration projects to explore methods to reuse and recycle pavement materials.
In response to this need, the Department of Civil and Environmental Engineering and Geodetic Science at Ohio State University (OSU) has partnered with the two fastest growing counties in Ohio (Delaware and Warren) to construct and monitor two pavement sections in which sections of failing asphalt pavements were recycled in 2006 using Ohio coal-generated fly ash as a cementing agent.
"The value of this technology and demonstration project to the contractor is at a minimum two-fold," says Chris Anspaugh, construction manager, Base Construction. "With the price of cementitious additives continuing to rise in price due to the substantial energy costs involved in producing them it would be of value to the contractor, from a competitive standpoint, to have alternative products available that will achieve the same end results.
"Secondly, the contractor needs testing data available that can be submitted to the owner to assure them that the product will perform as we are claiming," he continues. "This research will go a long way in providing that information." and lime-activated Class F fly ash
On this Full Depth Reclamation (FDR) research preservation project, the complete depth of the flexible pavement section consisting of the asphalt layer, base, subbase and a pre-determined amount of the underlying existing subgrade soil were uniformly pulverized, blended with chemical additives (Class F fly ash in combination with lime or lime kiln dust), and compacted to construct a new stabilized base course.
An asphalt overlay was then placed over the stabilized base. Class F fly ash in itself is not self-cementing. It needs additional lime to undergo a cementitious reaction. It's important to note that fly ash, when used in combination with lime or lime kiln dust, performs two important functions in FDR work:
- Fly ash provides the silica and alumina needed for cementitious reaction with lime to increase the strength, stiffness, and durability of the stabilized base layer
- Fly ash acts as a mineral filler to fill the voids in the granular pulverized pavement mix, reducing the permeability of the FDR stabilized base layer. Lime or lime kiln dust by itself will not provide adequate stabilization for pavement materials deficient in silica and alumina. The addition of fly ash is necessary for cementitious reactions to occur.
Objective and goal
The overall objective of this work is to demonstrate the effective use of Class F fly ash in combination with lime or lime kiln dust in the FDR of asphalt pavements.
The goal of the proposed program is to establish field-verified relationships for the service performance, structural and environmental behavior of FDR pavements constructed using lime-activated fly ash.
The project goal is being pursued with four interrelated activities. In the first, laboratory studies specifically designed to investigate the physical, chemical, and engineering properties of fly ash FDR mixes were conducted. This allowed the research team to determine the optimal material mixes that were implemented in the two pavement preservation projects.
In the second activity, two highway pavements were constructed and instrumented in 2006, and will be monitored for two years. The purpose of this activity is to obtain robust field results on the structural, service and environmental performance of field constructed FDR bases.
In the third activity, existing flexible pavements constructed in Ohio using FDR will be investigated. This will allow for evaluation of the performance of existing projects for which no performance data has been collected to date.
Lastly, the existing outreach and technology transfer efforts of the Coal Combustion Products (CCP) Extension Program at OSU will be focused on county, state, and federal transportation officials and other end users of the technology.
This project will demonstrate that when non-concrete quality fly ash in combination with lime or lime kiln dust are properly incorporated into FDR reconstruction of a flexible pavement, the use of fly ash can be economically attractive while offering increased structural and service performance, and should not lead to a degradation of environmental quality.
"One of our objectives in this research is to demonstrate the many potential environmental benefits associated with the use of fly ash in the FDR of asphalt pavements," says Associate Professor Harold Walker of OSU's Department of Civil and Environmental Engineering and Geodetic Science.
Delaware County pavement
Delaware County (just north of Columbus) is the fastest growing county in Ohio. In collaboration with the Delaware County Engineer's Office, Section Line Road between State Route 42 and Home Road was selected for FDR reconstruction in 2006.
The section of the road selected for study in this county measured 4.1 miles in length, 20 feet in width with minimal shoulders, and had a ¼-inch cross-slope consisting of an asphalt surface with thickness ranging from 5.25 to 14 inches (average of 10.28 inches). The original pavement was underlain by a base course ranging from one to 11 inches (average of 5.18 inches) thick.
The pavement sampling and design was to be carried out by EDP Consultants under the supervision of OSU. A total of nine sections were constructed using the following six mixes:
- 4-percent lime with 6-percent fly ash, 8-inch stabilization depth (0.7 mile)
- 5-percent lime kiln dust with 5-percent fly ash, 8-inch stabilization depth (0.6 mile)
- 3-percent lime kiln dust with 1.4 gallons per square yard emulsion, 8-inch stabilization depth (0.7 mile)
- 5-percent cement, 12-inch stabilization depth (0.8 mile)
- 2-percent cement with 1.6 gallons per square yard emulsion, 8-inch stabilization depth (0.3 mile)
- 5-inch mill and fill (two 0.1-mile sections at the north and south ends of the project, and a 0.7-mile as well as 0.1-mile sections near the middle of the project).
The FDR rehabilitation of the section Line Road was completed in five phases. Beginning in August, Strawser Paving first milled and removed 5 inches of the existing pavement asphalt surface. In the second phase, Base Construction pre-pulverized the remaining pavement materials to various depths as listed above.
The third phase involved treating the pulverized pavement materials with admixtures as outlined above. Water was then added to the mix and it was compacted immediately. The last phase involved resurfacing the pavement with 5 inches of hot mix asphalt and was completed by mid-October.
"All construction has been completed and our office believes that the construction portion of the project has cost-efficiently improved the structural strength and has allowed for the existing roadway materials to be homogenously stabilized by integrating fly ash, lime, and lime kiln dust," says Jerry Ungashick, project manager, Delaware County Engineer's Office.
Warren County pavement
Warren County, just South of Cincinnati, is the second fastest growing county in the state. The Long Spurling Road (County Road 171) located in the southeastern part of the county in Harlan Township was chosen by the Warren County Engineer's Office for FDR construction between SR132 and the north driveway to the LM Animal Products Plant.
The failing pavement was 0.4 miles in length, 20 to 21 feet in width with minimal shoulders and had a 2-inch asphalt layer on top of 4 to 6 inches of chipsealed pavement.
The pavement sampling and design was carried out by EDP Consultants under the supervision of OSU. Two sections were constructed as follows:
- 4-percent lime with 6-percent fly ash, 12-inch stabilization depth (0.32 mile)
- 5-inch mill and fill (0.08 mile)
The FDR rehabilitation of the Long Spurling Road was completed in five phases. Beginning in July, Strawser Paving milled and removed 4 inches of the existing pavement asphalt surface.
In the second phase, Base Construction pre-pulverized the remaining pavement materials to a depth of 12 inches. The third phase involved treating the pulverized pavement materials with lime at an application rate of 4 percent and allowing the material to mellow for a 24-hour period.
After the mellow period, 6-percent fly ash from Zimmer power plant of Duke Energy was blended into the mix to a depth of 12 inches. Water was added to the mix and it was compacted immediately. The last phase involved resurfacing the pavement with 4 inches of hot mix asphalt and was completed by mid-September.
"Our office is glad to be a partner with Ohio State University, the Ohio Coal Development Office and Base Construction (as well as many other private suppliers) in this FDR project using fly ash," says ," says Kurt E. Weber, P.E., P.S., chief deputy engineer, Warren County Engineer's Office. "Using FDR to repair Long Spurling Road was much more cost-effective than the alternative method of total full depth reconstruction. We're anxious to see the long term results of this project and how this method can be utilized in repairing county and township roads in the future."
Pavement instrumentation and monitoring
During construction, the Delaware and Warren pavement sections were instrumented with the following structural and environmental monitoring devices:
- Strain gauges at bottom of asphalt layer
- Pressure cells at bottom of stabilized base layer
- Pore pressure devices at bottom of stabilized base layer
- LVDTs for measuring vertical deflections of pavement
- Lysimeters installed within the stabilized base to monitor leachate quality.
Data collection from the above monitoring devices is being carried out on a quarterly basis.
Falling Weight Deflectometer (FWD) tests (to measure pavement load deflection behavior, resilient modulus of pavement layers and subgrade soil, and base structural layer coefficient) are being carried out by the Ohio Department of Transportation.
The FWD tests carried out on the pavement before and immediately after completion of rehabilitation show that FDR of the pavements with fly ash (and lime or lime kiln dust) increased the elastic modulus of the base layer. The fly ash sections exhibited elastic moduli of base layers similar to cement and cement plus emulsion sections.
FWD tests will continue to be carried out twice a year to determine the longer term elastic moduli of the various sections constructed in this project.
Benefits
The project findings will enable the users of the technology to reap significant cost savings when compared with the common practice of removing old pavement and rebuilding the roadway.
In addition, the technology addresses a very important environmental issue, says Professor William Wolfe of OSU's Department of Civil and Environmental Engineering and Geodetic Science.
"Since the production of one ton of cement produces about one ton of carbon dioxide, which is then released into the atmosphere," he says, "the widespread replacement of cement with fly ash in roadway reconstruction will result in significant reductions in the generation of this greenhouse gas."
This three-year project at OSU, totaling over $2 million, is funded primarily by the Ohio Coal Development Office of the Ohio Air Quality Development Authority with additional support from the Delaware and Warren County Engineers Offices, Base Construction, Carmeuse NA, Headwater Resources, and others.
"Last year, two counties in Ohio used Ohio coal-generated fly ash in reclaiming failed asphalt pavements," says Mark Shanahan, executive director of the Ohio Air Quality Development Authority, which manages the Ohio Coal Development Office. "This resulted in more durable highway infrastructure and promoted the recycling of pavement materials and coal combustion byproducts, both of which would otherwise have been landfilled."
Greg Samios, project manager of EDP Consultants Inc. adds, "The unique opportunity of a comparative mix design study has enabled EDP Consultants to increase our knowledge and understanding of how different chemical additives may benefit the recycling industry."
About the author: Dr. Tarunjit S. Butalia, P.E., is a research scientist and coal combustion products coordinator for the Department of Civil and Environmental Engineering and Geodetic Science at Ohio State University.
According to Dr. Butalia, an important component of this project is the technology transfer of research findings of the technical investigations of the research. Information about the results of the long-term monitoring program will be shared with members of the Asphalt Recycling and Reclaiming Association. You can reach Dr. Butalia at [email protected].