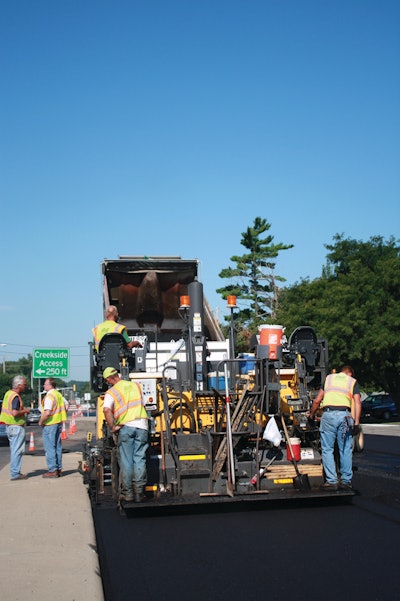
With an eye to cost-effective construction, a Minnesota city has placed substantial sections of pavement containing highly modified asphalt (HiMA) mix in an effort to fight the effects of weak subgrades and heavy traffic.
Bloomington, MN – population 84,000 – may just be a suburb within the Twin Cities region – but it has big-city problems when it comes to water-saturated bases and the heavy traffic that comes with its prime location south of Minneapolis and St. Paul, adjacent to the international airport there, and with the sprawling Mall of America within its city limits.
There, in two projects beginning in June 2012, 400 tons of HiMA was placed for a 6-in.-deep mill-and-fill reconstruction over a saturated subbase on Normandale Service Road at 84th Street, and then 900 tons of HiMA were placed on West 98th Street from Logan Ave. South to Penn Ave. South, abutting 1,400 tons of conventional PG 58-28 binder asphalt placed on West 98th Street as a control.
“Highly Modified Asphalt is a new SBS polymer technology for asphalt paving,” says contractor Bituminous Roadways Inc., Mendota Heights, MN, on its website. “The polymer loading is over twice the typical modified asphalt; however it is easily workable and very manageable in the field.”
Bituminous Roadways Inc. has been researching materials and methods to improve pavement durability and service life in Minnesota. “Our search brought us to Kraton Performance Polymers. Kraton had the right product at the right time for us,” the company says. “We believe that this is a product that will become much more commonplace in coming years and are excited to be at the forefront, providing it as a solution.”
The contractor has been working with the City of Bloomington on its street contract for 11 out of the last 12 years. In 2011, Bituminous Roadways was the prime contractor for work that was spread out over 13 different areas within Bloomington, involving 17,000 tons of asphalt in addition to removing and replacing curbs, sidewalks, sewer lines and water mains.
HiMA pavement mix should help the city place durable asphalt pavements with reduced pavement depths, or rebuild pavements above questionable subsoils without having to remove and replace the subsoil. Either way, the city may save road program funds, which can enable an even wider resurfacing program.
Precluding subgrade rebuild
“We had two projects that involved HiMA, a reconstruction and a mill-and-overlay,” says Dusty Ordorff, quality control/materials manager for Bituminous Roadways. “On the reconstruct at 84th and Normandale Service Road, adjacent to a high-traffic area near an extremely busy gas station, we placed asphalt mix that failed prematurely due to excessive moisture in the subgrade. We put two 2-in. lifts of asphalt down, but the upper two inches started sliding on us as water came up through the mat. We ended up tearing out the new asphalt, doing a sub cut and rebuilding it a second time.”
Bituminous first learned about HiMA in 2011. “MnDOT let a research mill-and-fill project in which one lane was highly modified, and while we did not build that project, we learned that HiMA is an alternative material that we could use,” Ordorff says. “We did quite a bit of research early in 2012 and when this opportunity presented itself we felt it was a good application for HiMA.”
The city was willing to give it a shot on the reconstruct project on Normandale Service Road. On Normandale Service Road, 6 in. were milled out, and replaced with three 2-in. HiMA lifts of 9.5mm nominal maximum aggregate size (100 percent passing 0.5-in. screen).
“The street reconstruction of Normandale Service Road north of W 84th Street was the smaller of the two HiMA projects,” says Bob Simons, P.E., civil engineer, City of Bloomington. “It was about 400 feet in length and approximately 25 feet wide and part of a larger reconstruction project in the area. It was a full street reconstruction and we were having issues with the subgrade materials, as there was peat and clay ground in the area. We already had reconstructed the north bound side of the section and paved the first couple of lifts of asphalt, but were still having trouble with the subgrade being too soft and wet.
“We ended up having to reconstruct the northbound side a second time,” Simons says, “but as we were putting it back together, Bituminous Roadways mentioned the Kraton polymer product at 7.5 percent loading, and asked if we would consider that for the southbound side, as there already was an existing pavement section of 12 to 18 in. there. We knew the subgrade materials on the southbound side may also have issues, so we thought we could save some money overall – while ultimately still having a great pavement – if we milled down 6 in. and put three lifts of HiMA back. We also would have a comparison opportunity between the HiMA mix on the southbound side where we did not totally reconstruct the pavement, and the conventional asphalt reconstruction, including subgrade, on the northbound side.”
Bloomington did not have a spec for HiMA use, but worked with the Bituminous Roadways, Kraton and MnDOT to get the confidence it needed to have the material placed. “Engineers at MnDOT had experience with HiMA and agreed with us that we should give it a shot,” Simons said. “It is a fairly new material, but other areas in the Midwest and the United States have found that it is holding up really well. Its use appeared to be cost-effective for us based on the existing conditions that were found during reconstruction.”
Battling loads on 98th Street
Success placing HiMA on the high-trafficked area above that saturated subbase on Normandale Service Road led to its use on an ongoing mill-and-fill operation on a busy thoroughfare with 16,000 ADT just a few weeks later.
“West 98th Street was scheduled to be a mill-and-overlay with conventional asphalt mix,” said Justin Ernst, P.E., civil engineer for Bloomington. “We realized just a week after Normandale Service Road that we’d like to try it there.”
There, abutting placement of both mixes will provide an apples-to-apples comparison of the durability of a thinner overlay of HiMA compared to a conventional overlay of asphalt under the same climate and traffic conditions.
“West 98th Street was slated for a 2-in. mill-and-overlay, and we took a segment of the project and went with an inch-and-a-half mill-and-overlay using HiMA,” Ordorff said. “Elsewhere on the project we kept a 2-in. mill-and-overlay with PG 58-28 as a control section. With the 25 percent reduction in thickness in the HiMA segment we were able to offset the increased cost of using the HiMA.”
About 1,200 ft. of HiMA were placed there, four lanes, two in each direction, with 2,600 feet conventional, Ernst said. “Both the contractor and Kraton suggested we could reduce the lift depth with HiMA, and they undertook calculations based on ADT to recommend just how much less it could go. By reducing the thickness of the lift, we were able to offset the cost of the more expensive HiMA and achieve better durability while reducing reflective cracking.”
Highly Modified Asphalt
In Bloomington, the single, highly modified binder was used for both projects at a rate of 6 percent by weight. Typically the HiMA binder in such mixes will contain more than twice the amount of SBS (styrene-butadiene-styrene) polymer used in conventional polymer-modified binders.
Polymer modifiers optimize asphalt pavement performance. Modification of liquid asphalt binders with polymers improves resistance to rutting and raveling of asphalt mixes, but there has been a practical limit to polymer concentration. Usually, as polymer concentration exceeds three percent, the viscosity of the binder increases such that the mix becomes more difficult to produce in the plant and less workable for the paving crew.
However, the polymer used in the two Bloomington projects was Kraton D0243, a new SBS product manufactured by Houston-based Kraton Performance Polymers Inc., which can be used in significantly larger quantities than conventional polymer modifiers.
From his viewpoint as QC/materials manager, HiMA behaves like a typical polymer modified asphalt, Ordorff said. “There is nothing unique about it from that standpoint and we don’t have to take any extra precautions handling or pumping the liquid, making the asphalt mix, or hauling or compacting it,” he said. “HiMA is business as usual.”
The 9.5mm nominal maximum aggregate size HiMA mix – with 100 percent passing 0.5-in. screen – was produced at the plant with a water injection system making foamed warm mix asphalt at 300 deg F, and it was being placed at about 265 deg F. “Normally, we’d be well above 300 if it were a typical hot mix,” Ordorff said. “At another facility we’ve produced HiMA using a warm mix asphalt additive. It’s worked great with these two different WMA technologies.”
On Bloomington’s HiMA overlays, Bituminous Roadways attained a minimum of 92 percent of maximum density, according to city engineers, which mirrors MnDOT’s specification for a wearing course. As state aid figured into the projects’ funding, use of HiMA for these municipal projects had to be approved by MnDOT. Density was confirmed by cores taken by the contractor.
Battling against cracking
Bituminous Roadways did not have to mount a vigorous sales job on behalf of HiMA. “They knew they had a problem, and we felt we had the right solution,” Ordorff said. “We provided the city with literature on the HiMA research projects that were ongoing, and Kraton personnel were communicating with them. They had confidence in trying HiMA and knew they were getting a premium product that in theory should perform better than a conventional polymer modified asphalt for those applications.”
HiMA in Bloomington should quell pesky reflective cracking, Ordorff said. “In Minnesota, reflective cracking is common for mill-and-overlays,” he said. “Whether a neat or polymer modified asphalt is used, when we overlay a road, existing cracks below will reflect through the new mat within the first year. That’s why we proposed using the HiMA; we feel that this product has the ability to reduce the amount of reflective cracking that is going to occur, especially in a thick section as on Normandale Service Road, and even on the thinner lift on West 98th Street.”
HiMA is forcing a new look at how asphalt mixes are structured, Ordorff said. “With HiMA, we have gone from a conventional polymer modified asphalt, to an asphalt modified polymer,” he said. “With that degree of polymer loading, a polymer network is created, providing an extremely flexible and highly elastic binder. It will bend, but it won’t break.”
In the meantime, Bloomington engineers will be comparing as-built images and video to field performance – especially as it pertains to cracking – over the coming months and years. “We’ve documented construction thoroughly and it will be a few years before we see a benefit,” Simons said. “Reflective cracking and thermal cracking is an issue in Minnesota. In the course of a winter we can see several freeze-thaw cycles. That poses real issues for our pavements. We’re told HiMA helps to resist thermal cracking so we will wait and see.”