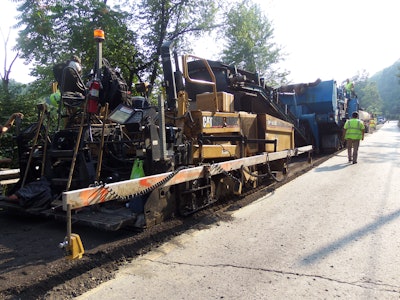
The state of West Virginia – with its rugged steep mountains, deep valleys and winding roads through scenic undulating countryside -- was made for driving and biking tours.
Drive on any of the Interstate highway system from I-68 and I-79 in the north to I-77 and I-64 in the south you find some breathtaking views.
Like many states, there are issues with its highways and roads. Faced with tighter roadway funding due to reduced gas tax and other revenue sources that have fallen short of expectations, West Virginia’s roads have had to last longer with fewer maintenance repairs being made.
Because of this, West Virginia’s Division of Highways (WVDOH) has searched for alternative processes for both rebuilding the aging highway system as well as preserving it.
“With the help of pavement preservation, the state has had great success in using micro surfacing and other pavement preservation techniques to maintain and preserve the integrity of its roadways,” says Michael L. Polak with E. J. Breneman, L.P.
For the roadways that have suffered the most deterioration and have been more difficult to maintain, the WVDOH is using cold in-place recycling (CIR). On very deteriorated roadways with subbase issues, full depth reclamation (FDR) is being targeted for use.
WVDOH has over 36,000 center-line miles in its system, which is the sixth largest state-maintained highway system in the country. It maintains virtually all levels of road in the state, including the lowest level local service routes (less than 500 ADT) up to interstates and other primary multi-lane routes.
“Within this system is a very large mileage of two-lane roads that serve as secondary trunk-line and feeder routes, where money seems to be really stretched, yet the types and depths of pavement distress are applicable to use of CIR,” says Thomas J. Medvick, PE, pavement engineer with the Materials Control, Soils & Testing Division of WVDOH. “We feel that CIR is a tool that can really help us long-term.”
Finding the best method
The WVDOH consulted with professional associations, highway industries, Pavement Preservation (FP2) experts and academia before setting out on a fact-finding mission into alternative methods of preservation and construction. The WVDOH also visited ongoing projects in other states and consulted with experienced industry experts.
“CIR underwent tough scrutiny,” says Polak. The WVDOH’s Contract Administration Division, along with approval from the Secretary of Transportation, placed a project out for bid in 2012. The project was won by Mountaineer Construction who was the low bidder and used sub-contractor E.J. Breneman, L.P. of West Lawn, PA.
Because the project was bid late in 2012 the project was postponed until 2013 construction season.
The first project: Fort Martin Road
Monogalia CR 53/Fort Martin Road is a two-lane, 22-foot-wide coal haul roadway with an ADT of 2,200 and 35% truck traffic. The road lies just north of Morgantown, WV. There are a number of coal breakers along the roadway and a staging area for un-loading and re-loading coal.
Some of the coal is also loaded onto barges on the Monongahela River that runs north to Pittsburgh, and parallels Fort Martin Road. Fort Martin Road sits wedged between the river and Norfolk-Southern Railroad on the north side.
The pavement of the tree-lined Fort Martin Road was oxidized and had been subjected to heavy loadings for many years. Large cracks, potholes and delaminating of the asphalt layers were evident along this section.
Using a design life of 18 years and based on approximately 9 million ESALS, a new pavement section was designed. As a result, the plans and specifications for the project called for the recycling of 6 inches of asphalt and the introduction of a dual additive -- asphalt emulsion and Portland cement.
During construction, traffic was allowed to travel along Fort Martin Road under the direction of traffic control. A pilot car was used because some areas the road narrowed to an 18-foot width.
“At no time was traffic kept waiting for more than three or four minutes,” says Polak.
Mountaineer Construction placed dozens of new catch-basins on the north side of the roadway with new pipes being placed under the roadway to take stormwater away from the shoulders.
Trenches where backfilled with concrete two feet thick and 24 inches wide.
“Because of the amount of drainage trenches, a decision was made to merely cut through them at the same depth as the CIR so the road had fewer areas with joints that where asphalt-to-concrete,” explains Polak. “The down-cutting mill sliced through these with ease.”
Cold In-Place Recycling
CIR is defined as “an asphalt pavement rehabilitation technique that reuses existing pavement materials.”
“Some of the best quality aggregates have been paid for and are within the roadway structure,” says Polak. “By reusing these aggregates, we are helping to stop depleting our natural resources and also help on reducing our dependency on foreign crude oil.”
CIR involves the processing, and treatment with bituminous and/or chemical additives, of the existing asphalt pavement without heat to produce a restored pavement layer. All work is completed in-line and on the pavement being processed.
There is some excess material that is exported from the project site; this material is only exported so as a new hot mix asphalt might be placed at the same elevation that meets all on site utilities and storm water inlets.
Laying the Portland cement
The mix design specified in the Fort Martin Road contract consisted of emulsion and Portland cement and was created by Ergon Asphalt & Emulsions Inc. E.J. Breneman laid the Portland cement ahead of the train for a distance of around 100 feet.
E.J. Breneman uses a Stoltz Mfg. dry additive spreader. The skirting on the auger and additive application area is full length and comes within four inches of the roadway surface.
“The skirting is necessary because Portland cement is light, and if not placed correctly, can become airborne,” says Polak. “It’s also advisable that even with the skirting, if the wind is moving at over 10 mph, it may be necessary to stop operation until the wind is more reasonable.”
The equipment is calibrated before the start of work each day. The cement is laid dry onto the surface of the roadway at a rate of about 12/15 lbs. (1.5%) per square yard.
To check on the application rate, a one yard square tarp is laid on the surface of the roadway. The application truck drives over the tarp in a certain gear and speed placing the Portland cement on the tarp. The tarp is then lifted off the roadway, and the tarp and its contents weighed.
“Depending on the weight adjustments to the gears and speed of the truck, adjustments can be made,” says Polak. “The calibration would take place until the correct pounds of material per square yard is obtained.”
The CIR train
In the Fort Martin Road project, while the train has three main components, it is referred to as a single-unit train.
First in line is the asphalt emulsion tank built by E.D. Etnyer & Co. to E.J. Breneman’s specifications. The tanker holds 5,000 gallons of liquid asphalt.
On this project, the emulsified asphalt was CSS-1h. The tanker was connected to the milling machine with a cutting mandrill of 10.5 – 11.00 or 12.00 foot.
“With differing road widths, it’s essential to have different sized cutting heads,” says Polak.
The emulsion is metered into the cutting mandrill and mixing chamber of the milling machine.
“This large mill uses a down-cutting action to size the material to 1.5 inch minus,” Polak says. “The forward speed of the milling machine and the down-cutting action provides the material sizing. If a greater size of material is required the machine is moved into a faster gear.”
The Portland cement is picked up by the cutting mandrill and is mixed with the emulsion and water into a homogeneous mix in the cutting chamber. The mixed material is then moved along the shaft of the mandrill to the “throw area.”
At this point, the mixed material is placed onto a first stage conveyor, which places the material onto the second-stage conveyor. The second-stage conveyor carries the material to the conventional bituminous paver.
The paver has an insert bin placed inside its hopper. All of the mixed material then goes into the insert bin and is conveyed to the augers and screed. The bituminous paver is fitted with a 40-foot leveling or averaging ski that has no contact with the roadway surface. The ski is controlled by sonic pulses from four units that are attached to the beam.
Compaction, prime & asphalt paving
Once the material is laid to the desired depth and cross slope, the compaction effort starts. Under the guide of a nuclear gauge operator, the CIR base is compacted to the desired density in the specifications.
E.J. Breneman used an 11- to 13-ton steel wheel vibratory roller and a 22.5-ton pneumatic-tired roller for the compaction process.
“On the projects we’ve used CIR, we’ve had the best results using the steel drum roller as the initial break-down roller,” says Polak. “Most of the density requirements are also obtained by the steel drum roller.
“The entire mat is rolled by the pneumatic-tired roller from edge of shoulder to inside edge of pavement, no area is left un-rolled,” he says.
Once the CIR was compacted, the total roadway surface received a prime coat. A 50/50 blend of emulsified asphalt and water is sprayed onto the surface using a distributor truck.
The prime-coat takes 15 minutes to dry. Traffic was maintained in one lane while prime-coat was sprayed in adjacent lane.
Mountaineer Construction first placed a new 3-inch Marshall hot mix asphalt (HMA) binder base course (NMAS 0.75 inches) on top of the CIR base material. A Marshall HMA wearing surface (NMAS 0.5 inches) with PG 76-22 binder, compacted 2 inches in depth, was placed for the driving surface.
“The reason for the heavy lift of hot mix asphalt was due to the tremendous amount of loaded and empty track trailer and tri-axel trucks hauling coal along the entire length of Fort Martin Road,” explains Polak.
Medvick with the WVDOH says the state feels the project was a resounding success. “It’s been more than 12 months since the project was completed and the road looks outstanding.”
Because of its strong outcome, more CIR projects are underway. “The local highway district (District Four-Clarksburg, WV) is very pleased and there are currently three more CIR contracts that have been let or are being advertised in that district,” says Medvick. “One of those was just completed last week and went well. There are also two more CIR projects for 2014 elsewhere in the state.”
As a matter of fact, the Fort Martin Road project has been tapped to be a part of a new CIR study that is being conducted jointly by the University of Maryland, VDOT, Colas Solutions and Wirtgen. “We recently obtained cores of CR 53 Fort Martin for inclusion in NCHRP 9-51, a study to develop pavement design inputs for CIR,” says Medvick.
Now that’s an efficacious first attempt at CIR!