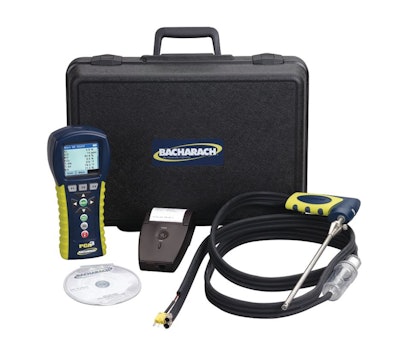
One of the most expensive consumables around your plant is burner fuel. I’ve talked a little bit about how keeping your stockpiles and RAP dry with covers can help reduce fuel costs. I talked last month about the usefulness of Daily Records Keeping at your asphalt plant. Now I want to talk about how burner tuning can optimize fuel consumption.
But first I need to talk about what you need to properly analyze the performance of your burner. There are many combustion analyzers on the market. I will not pretend to have an opinion on which one is better. Instead I will just talk about the one I use, the Bacharach PCA-3 235.
This analyzer will test CO, CO2, O2, NOx and burner efficiency. You will want to buy the whole kit which will cost about $2,800 + shipping. Alternately you can go to Grainger and order part number 12J896 which is the whole kit for about $2,600 + shipping.
I also use a Dwyer Handheld Manometer to figure exhaust stack air velocity. The cost for this unit is around $475 + shipping. Alternately you can go to Grainger and order part number 1XFW5 which is the whole kit for about $500 + shipping.
These tools seem expensive until you realize, if you use them to maximize your fuel efficiency you could potentially save that much in the first week.
Goals of testing
This month I will just talk about our general goals. Next month I help the reader understand how to use the readings from these two instruments to properly tune your burner. For now our interest is in knowing our plant’s fuel consumption. The following strategy works whether you burn natural gas, propane, diesel or recycled fuel oil.
Working on a well-tuned asphalt plant, in the summer with approximately 5% incoming moisture, I expect to see about 179,000 BTU used per ton of asphalt produced. I expect to see the air velocity in the stack equate to around 155 cubic feet per minute of air. These things are easy to check.
If you are burning #2 diesel with a Hauck burner, most of them have a fuel flow meter you can read in real time. Some of my clients have even added fuel flow meters to their other brand burners. With natural gas, it is as simple as reading the gas meter, waiting 10 minutes then reading it again. Multiply by 6 and you will know your fuel consumption per hour in real time.
You can figure out the BTUs your plant is using per ton by figuring the number of tons divided by the amount of fuel used per day. This data should be readily available to you on those Daily Plant Reports I’ve been yapping about. To convert the fuel use data to BTUs, here are the industry standards for the amount of BTUs in each kind of fuel.
#2 Diesel 138,000 BTU per gallon
Waste Oil Appx. 142,000 per gallon at 90 SSU
Nat. Gas 1,000 BTU per cubic foot
LP 91,044 per gallon
You can use these numbers to figure out how many BTUs you are using to make a ton of hot mix. Simply use the data above to convert the amount of fuel you use per ton into BTUs. It should be roughly 179,000 BTUs. If it is a little higher or a little lower then you are probably fine. But if you are WAY off this number I suggest you get out your PCA-3 235 out and get some combustion readings.
Cliff Mansfield Inc. is the Northwestern Regional Sales and Service Center for Hauck burners. We get to do a lot of burner tuning. So if anyone needs help before next month when I describe burner analysis and adjustment procedures, please feel free to call or email for assistance.
You can find the Bacharach at mybacharach.com and the Dwyer Handheld Manometer at dwyer-inst.com.