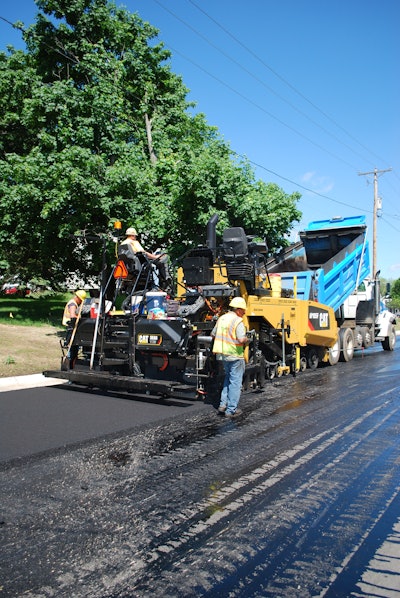
By Todd W. Mansell, Product Application Specialist, Caterpillar
Meeting or exceeding density specifications in the field is a challenge for many paving crews. In most highway paving operations, the ability of the rollers to keep pace with the paver and still meet or exceed density requirements is the limiting factor in achieving daily production goals. Consequently, more often than not, tonnage goals are met and density suffers.
Here we'll present a practical approach to managing density based on keeping up with the paver without sacrificing density. It's possible to place the desired number of tons of mix and meet or exceed density specifications with a little upfront planning. The best part of this process is that it costs NOTHING other than a commitment by management to support and execute the paving and compaction plan through good communication to all team members.
1. Know your lines of communication
It’s difficult, if not impossible, to maintain an effective rolling pattern that achieves density if there is no communication protocol in place. It should be clear who is directly responsible for managing the roller operators, whether it be the paving foreman, quality control (QC) technician, or another.
A communication protocol should be known in advance of the project starting. It should clearly define who's in charge of making changes to the rolling pattern. Is it the paving foreman, QC tech, roller operators themselves, the project manager? It varies from company to company and maybe from job to job.
At a minimum, each crew member should know and understand what the lines of communication and action are. When things are going bad, it's not the time to be deciding who's in charge of a situation! There should be a list with every person’s name, on-site phone number and the order in which they should be contacted when it’s necessary to make changes or report passing, and more importantly, failing densities during production.
2. Know your mix design properties, job specifications, targets
Ask yourself if you have a choice of mixes or mix designs to submit for this project. Mixes with a history of achieving good density are always a good choice.
Is it a harsh mix or a tender mix? Expect delays compacting a tender mix, especially on a thin overlay project where paver speed is higher.
The target density is usually higher than the minimum density requirement on a project. For example, the minimum required density might be 92%, but due to inherent variability and the nature of statistical-based specifications that use Lots and Sublots, or Percent-Within-Limits (PWL), we may target a higher number such as 94% to ensure a “safety net.”
Statistically, a higher average (mean) percent compaction target should essentially eliminate any percent outside limits and pay reductions. To achieve this, we need the average compaction target set at 94% or higher – so many companies will target an average of 94% to account for variability in compaction. Higher target ensures the lower readings do not fall below the minimum required.
Estimators typically bid the job based on a certain number of tons of asphalt mix placed each day. There is pressure to meet this daily tonnage and if you don’t - you risk losing profit on the job and are under more pressure to exceed production on a future shift to make up for the loss. This pressure further exacerbates the ability to meet the density target as paving speed increases and the rollers are pressured to increase their speed, even though the mix or paving window has not changed.
The daily tonnage greatly influences paver speed which in turn influences roller speed. This is where the planning is critical to have the proper number and type of rollers to meet the production and density targets established in the pre-paving planning.
Targets also need to be set and communicated. Target paving speed based on placing the tonnage of mix expected per shift that provides for a continuous paving operation.
The Caterpillar Paving Production Calculator app, available for iOS and Android devices, and the National Asphalt Pavement Association’s publication IS-120 (www.asphaltpavement.org) are two tools that can be used to determine the required number of trucks and paver and roller speeds to consume the planned tonnage for a paving shift.
Once the planned paving speed that will consume the required tonnage is established, the target roller speeds can be determined.
3. Establish an effective rolling pattern
Above all else, the temperature of the asphalt mix at the time of breakdown rolling through finish rolling will determine how successful the compaction operation will be.
It's important to understand how mix temperature is related to compaction and how you can manage it in the field. The hotter the mix is when the first roller hits it, the easier it will be to achieve density in the field.
Maintaining mix temperature from the plant through the paver to the rollers is always a challenge. As the mix cools, it becomes more and more difficult to get density. For example, starting breakdown rolling at 290°F could require one less roller pass than starting breakdown rolling at 270°F to achieve the same density. As the mix cools further, it becomes exponentially more difficult to achieve the same level of density than if compaction had started at a high temperature.
As long as the asphalt cement can flow, the compactive effort of the rollers can force the mix into a compacted, stable configuration with good aggregate (rock and sand) interlock. When asphalt cement becomes more viscous as the temperature of the mix drops, it behaves more glue-like and the aggregate in the hot mix cannot be properly compacted by the force of the rollers.
Mix temperature is the single most critical factor to achieving sufficient compaction. The time available for compaction (TAC) defines the total amount of time that rollers operators have to achieve density before the mix cools too much and becomes too stiff to compact.
MultiCool is one computer software tool that is available for free (asphaltpavement.org/multicool) that provides accurate estimates of the TAC. For maximum efficiency, breakdown rolling should begin at temperatures above 290°F for most conventional mixes. When breakdown rolling begins at temperatures lower than 290°F, the risk of not achieving sufficient compaction is greatly increased.
It is extremely difficult to achieve maximum compaction if breakdown rolling has not started before the mix cools to 280°F. Warm mix asphalt (WMA) behaves similarly in terms of compaction, only at lower breakdown rolling temperatures and lower finish compaction temperatures. Because breakdown compaction of WMA starts at a lower temperature, there is often a slightly extended Time Available for Compaction when using WMA.
Understanding that compaction is directly related to the mix temperature, extra effort should be put forth to maintain sufficient mix temperature during production, transportation, placement and compaction of asphalt.
Roller speed is equally important. Empirical data tells us that maintaining a vibratory roller speed that is within the range of 10 to 14 impacts per foot will achieve both density and smoothness results.
What are impacts per foot, and how is roller speed and impacts per foot related? Before answering these questions, an operator should understand that steel drum vibratory rollers have two basic settings when it comes to compaction – amplitude and frequency.
Amplitude – can be thought of as how ‘hard’ the drum hits to impart compactive effort to the mat, or the compactive effort transferred from machine to mat. A rule of thumb is that most rollers will be set in a low amplitude setting for lift thicknesses of 2” or less. Typically, less than 1” thick would be static rolling, meaning vibration is turned off completely. For lifts 2” or greater in thickness, generally a higher amplitude setting provides the most effective and efficient breakdown compaction.
Frequency is how often the drum hits the mat as the roller travels down the road. In vibratory mode, the drum is moving up and down at a certain number of vibrations per minute as the roller moves forward. Thus, the speed of the roller will determine how many impacts will be made per distance traveled. The optimum target is 10-14 impacts per foot. If the roller is going too fast for the speed of vibration, or frequency, there will be ripples in the mat. These ripples are indications that density is not likely to be achieved and they are a sure sign that smoothness specifications will not be met.
Always remember that higher amplitude settings are associated with lower frequency settings on rollers equipped with multiple selections for amplitude and frequency. Always consult the operator’s manual for settings.
When it comes to roller speed, the operator must know what frequency the machine is running at in order to determine the roller speed that will deliver 10 impacts per foot. Some rollers are equipped with gauges that indicate impacts per foot, however, these gauges are generally not very accurate and often become non-functional over time.
A simple calculation to determine the proper roller speed is to first know or measure the frequency setting of the roller. The operator’s manual should state the frequency settings. Alternatively, there are various tachometers on the market that can measure frequency in the field, more expensive reed tachometers, or inexpensive, but sufficiently accurate, dial tachometers. Once the frequency is determined in vibrations per minute (VPM), simply divide that number by 10 to determine the roller ground speed in feet per minute.
There are three phases and a common arrangement for a typical highway job rolling pattern. The first phase is the breakdown phase, which is followed by the intermediate phase and then finish rolling. Any phase of compaction can involve one or more rollers. The goal is to achieve the majority of density during the breakdown phase of compaction when the mix is hottest.
Intermediate rolling should meet or exceed the final density requirement while the goal of finish rolling is to remove any roller marks left by the breakdown and intermediate rollers. Rolling trains can be all steel drum rollers or a combination of steel drum and pneumatic (rubber-tire) rollers.
In order to balance the roller speed with the paver speed, divide the roller ground speed by the number of breakdown roller passes required to cover the full width of the mat the required number of times to achieve the target density for the breakdown phase of compaction. For example, if the roller frequency is set at 2,500 VPM and we divide by 10 to calculate a roller ground speed of 250 feet per minute (FPM), divide 250 by 5 to get an EFFECTIVE ROLLER SPEED of 50 FPM.
Effective roller speed refers to the roller’s ability to keep pace with the paver. Remember, the paver is continuously moving forward, whereas the breakdown roller must travel back and forth on a specified number of times determined during a test strip. Since the roller must change direction at the end of each pass, we use an efficiency factor of 80% to determine an effective roller speed of 50 x 0.80 = 40 FPM. In this example, the paver speed cannot exceed 40 FPM for the breakdown roller to keep up and maintain 10 impacts per foot.
Two essential things to remember for compaction and establishing a rolling pattern are the TAC and a roller speed and frequency setting that results in 10-14 impacts per foot. When calculating the TAC, consider these points:
- Can we reasonably expect to roll this mix before it cools too much? Do we need more rollers, or a wider roller to get coverage faster?
- Based on the job conditions of lift thickness and expected air and base temperatures - what will be our time available for compaction? Use charts, past experience or software programs (MultiCool) to estimate a starting point. Always verify results in the field by measuring temperatures.
- At what mix temperature should we ask the production facility to load trucks?
- Do we need to tarp trucks?
- How should we modify our rolling pattern based on the expected cooling rate? How much do we need to shorten the length of roller passes to cover the mat before it cools?
On a typical project, paver speed often dictates how fast roller operators will go. Roller operators want to keep up with the paver where the mix is hotter. This is why it's critical in the compaction process to establish a paving speed that will allow the rollers to maintain a speed that gives them 10 impacts per foot and allows them to complete their number of passes and stay with the paver.
If production requirements of tonnage per day don’t allow such a slow roller speed, consider adding more rollers to keep up with the paver and maintain 10 impacts per foot, otherwise, density and smoothness will suffer. It's usually more economical to add another roller and to keep up with the faster paver speed. The cost per ton of compaction is relatively small compared to the bid price per ton (in-place), the material cost, and almost every other aspect of the laydown operation.
Caterpillar’s Paving Production Calculator, available free download from iTunes Store, takes user inputs such as tons per shift, different roller sizes, lane width and thickness, roller settings of amplitude and frequency, to calculate a balanced paving operation.
Check your numbers. It’s a tough balancing act between tons per hour placed by the paver and the ability of the rollers to keep up with the paver, but with a solid understanding of how to figure out roller speed, we can make sound decisions on what equipment and people we need on the job.
4. Identify root causes when density is not being achieved
When density is not being achieved in the field, take a systematic approach that starts looking at the most likely and easiest to check possibilities and progress towards less likely and more difficult things to check. Some common troubleshooting situations are:
- Mix temperature
- Paver speed and roller speed (10-14 impacts per foot)
- Verify roller settings of Amplitude, Frequency, Speed Equipment not working as expected (low VPM, no vibe)
- Nuclear gauge not calibrated/out of calibration
- Sand changes at plant can affects theoretical maximum density, VMA
- AC content, fines return at plant, gradation
5. Plan for unplanned events
Always have a Plan B ready to go. Know ahead of time what your options are instead of losing valuable time and quality trying to make a decision on what to do when problems arise. What if the plant breaks down and it will be at least an hour or more? What if there is an equipment failure? There are many other “what if” examples to plan for, and spending time beforehand investigating options will provide you with actionable plans to execute at a moment’s notice. These situations are when the communication protocol discussed earlier becomes extremely valuable.
It doesn’t take long to develop a paving plan. Just remember, time available for compaction (TAC) is based on mix cooling rate and always maintain at least 10 impacts per foot with your steel drum rollers. Take the time to develop a paving plan and communicate it with your crew. Be clear on who is responsible for each aspect of managing density and enjoy the success that comes with working as a team and taking pride in your work.