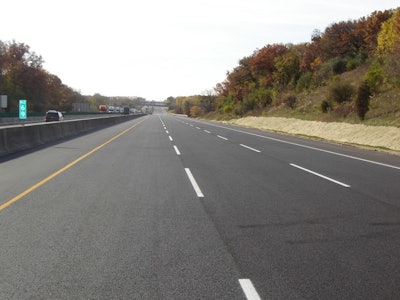
The Illinois Tollway carries more than 1.6 million vehicles per day. It is a user-fee system and no state or federal gas tax dollars are used for maintenance and operations.
The Tollway found that making changes with aggregates and asphalt mix designs could substantially provide economic, environmental and social benefits.
“The Tollway is a much smaller organization than a typical State DOT,” Paul Kovacs, chief engineering officer for the Tollway says. “Last year alone, we undertook the delivery of $1 billion in capital improvements with less than 20 in-house engineers. We operate under a very lean structure and rely on consultants to help deliver the program and provide innovative ideas. This allows us to expand and contract our professional services as needed and help implement cost saving measures.”
The Tollway began working with Applied Research Associates (ARA) vice president and principal engineer Bill Vavrik in 2000, a time when the agency was not using any recycled material, importing a good amount of aggregate for their high friction mixes and paying more per ton than necessary for asphalt.
“Researching best practices and working with industry to implement these innovative ideas helped the Tollway reduce costs and established the agency as an industry leader,” Vavrik says.
The Tollway has steadily implemented these best practices in construction over the past 12 years, producing new standards and policies for pavements, materials and recycling. The Tollway recently reviewed construction costs and found the adoption of more innovative and sustainable material specifications saved an estimated $247.5 million between 2004 and 2017.
Savings from the Ground Up
In 2005, the agency launched the first of two major capital programs that allocated the funds necessary to expand and reconstruct the 50-year-old Illinois Tollway1. These programs have included the $6 billion Congestion-Relief Program (2005-2016) and the $14 billion Move Illinois Program (2012-2026).
To maximize the return on these investments, the Tollway considered cost-saving methods that relied on established recycling practices. Existing aggregate subbases were reused and existing concrete was recycled through rubblization or crushing to create a new pavement base. Existing asphalt was also recycled for many applications.
Nearly 32 miles of concrete pavement was rubblized in place along the Reagan Memorial Tollway (I-88) for reuse as the new base for an asphalt pavement. Compared to the cost of total reconstruction of the mainline roadway, implementing this strategy saved the Tollway approximately $29.5 million.
The Illinois Tollway’s program management office, HNTB Corporation, confirmed that recycling pavements into the new bases of the reconstructed and widened roadways saved an estimated $73.5 million through 2015.
These aggregate-related initiatives alone saved a total of nearly $103 million.
Mixing it Up
To help the Tollway achieve sustainability goals, the industry helped coordinate research initiatives for asphalt mix designs and these were implemented fairly quickly based on findings.
“The Tollway has a very rapid innovation cycle,” Vavrik says. “If someone suggests increasing recycled asphalt pavement (RAP) percentages, we look at that in the lab and if it has the right material properties, we go to building test sections on a low-level mix in the field and see how it performs.”
“The Tollway seeks input on innovations, initiates research timely and quickly moves to test the results in a pilot phase," Kovacs says. "Our existing work and our contractors have provided a great opportunity to serve as a test bed for the most promising pavement innovations. If the innovation proves to be successful in the pilot, it is quickly adopted into standard practice. We want to be an innovator, and we understand that means learning from what works and what doesn’t.”
In 2006, the Tollway began field testing and analyzing pavements with ground tire rubber (GTR). It started with high-performance stone matrix asphalt (SMA) mixes with asphalt binder modified at the terminal. These mixes included shredded scrap tires at up to 12 percent of the mix. By making this change, the Tollway saved an estimated $7.50 per ton by eliminating the need for fiber reinforcement1.
The researchers studied the early age rutting potential of high asphalt binder replacement (ABR) SMA mixes with various warm mix processes. They found that in place, SMA surface mixes with low, medium and high ABR content maintained performance. The mix also competes with SBS modifiers to reduce prices further.
This change equated to a $2.2 million in savings for the 300,000 tons of SMA the Illinois Tollway produced from 2008 to 2011.
The Tollway also began investigating fractionated reclaimed asphalt pavement (FRAP) through research at the University of Illinois in 2007. Both hot and warm asphalt mixes with varied levels of FRAP were produced and tested for performance.
Researchers found asphalt mixes could contain an average of 15 percent more RAP with fractionation and the pavement would have the same high performance as RAP mixes previously used by the Tollway and by Illinois DOT.
Higher levels of FRAP reduces virgin aggregate needs and liquid asphalt quantities. The increased FRAP reduced the costs of the asphalt mixes by $10 to $15 per ton.
In 2009, with the help of a grant from the U.S. Environmental Protection Agency, the Illinois Tollway teamed with Iowa State University and the University of Illinois to study the combination of RAS with high FRAP in shoulder mixes. The up to 5 percent RAS allowable in asphalt mixes can reduce the need for virgin asphalt binder by approximately 20 percent. The use of RAS allowed for ABR levels to go higher and reduced the need for fibers in SMA.
The savings with RAS depend on the asphalt mix, but is estimated at $5 to $15 per ton. Approximately 2.6 million tons of asphalt mixes with RAS were produced between 2010 and 2015, yielding a savings of around $21 million.
Total savings since these initiatives were introduced in 2006 is approximately $74 million.
Future of Research
Because of the Tollway’s success with rapid field testing, a formal research program with local universities was developed to investigate even more sustainable solutions for future use.
Currently, the Tollway is investigating other options for ground tire rubber modifications and conducting research to find the best lab test methods to use with performance-based specifications for asphalt mix designs. It is also working on research relating to intelligent compaction.
“The Tollway has been fortunate to dedicate about $1 million a year on research initiatives,”Kovac Says. “We start by identifying a need or a challenge that we are facing, seek a research needs statements from interested universities and then implement research projects that will make a difference for the Tollway and hopefully the industry as well.”
References:
Steve Gillen, Implementing Sustainability Research Saves Illinois Tollway More Than $200 Million (TR News 308, March-April 2017)