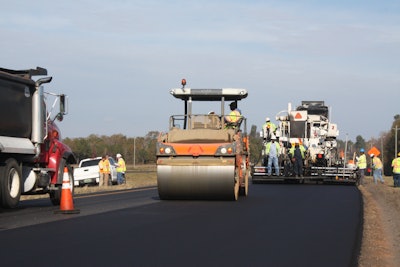
The Alabama Department of Transportation(ALDOT) is conducting an experiment on a four-lane highway involving an advanced, non-toxic asphalt rejuvenator in a pavement mix containing a high percentage of recycled asphalt pavement (RAP).
ALDOT is collaborating with the National Center for Asphalt Technology (NCAT) at Auburn University and contractor Midsouth Paving Inc. on the design, production and installation of a trial resurfacing course for a section of US Route 431 in the Troy area of the Southeast Region of Alabama. The applied research project involves a 0.7-mile segment of the slow-lane in the northbound roadway that was paved with a high-RAP mix dosed with Delta S, a newly commercialized, sustainable asphalt rejuvenator.
The research project stems from ALDOT officials’ concern that early cracking may occur in its pavement containing significant amounts of RAP.
For a number of years it has been standard practice for ALDOT maintenance projects to incorporate 20% RAP in resurfacing mixes as a way to preserve pavements economically. Many other DOTs across the nation have similarly adopted the use of RAP to cut costs while extending the life of asphalt pavements. This is corroborated by the extent of asphalt recycling now taking place. In 2016, more than 79 million tons of recycled materials — mostly reclaimed asphalt pavement and recycled asphalt roofing shingles (RAS) — were put to use in new asphalt pavements according to the latest survey of asphalt producers' by the National Asphalt Pavement Association (NAPA) and the Federal Highway Administration. Furthermore, the survey revealed that reclaiming and reusing the asphalt cement in RAP and RAS saved more than $2.1 billion in 2016 compared to the use of virgin materials, and also saved nearly 50 million cubic yards of landfill space that would have been used to dispose of demolished asphalt product.
A Remedy For High-Rap Mix Cracking
The substantial use of RAP in pavement mixes underlines the widespread recognition of its benefits, among them, according to NAPA: it reduces cost and bid prices of hot mix asphalt materials; for design purposes, RAP mix is structurally equivalent to conventional mix containing all-virgin materials; and long-term performance is at least equivalent to virgin mix.
However, industry experts warn of a major problem associated with using large amounts of RAP in pavement mixes, i.e., the higher viscosity and lower ductility of embedded asphalt due to long-term aging in the elements can lower the resistance of new pavement to cracking. A remedy for this problem is the use of an asphalt rejuvenator to restore the original properties of asphalt binder. Again, experts caution: conventional asphalt rejuvenators may contain derivatives of benzene, a toxic substance.
Delta S remedies this problem, since its chemistry is derived entirely from organic plants and is harmless to humans and the environment, according to producer Collaborative Aggregates LLC. An affiliate of Warner Babcock Institute for Green Chemistry (WBI), Collaborative Aggregates LLC manufactures, markets and sells engineered construction products developed by WBI labs, where more than 20 scientists are creating sustainable (green) technologies for all industries producing or employing chemicals. A team of these scientists invented Delta S to help prevent premature cracking of high-RAP content asphalt pavement.
NCAT Gets Involved
ALDOT decided to take a close look at the new non-toxic rejuvenator.
“We were looking for a solution to the early cracking that has been occurring in our standard maintenance resurfacing mix, which contains 20% RAP,” Christopher Huner, P.E., Troy area materials engineer for ALDOT’s Southeast Region says. Huner discussed the problem with Raymond “Buzz” Powell, PhD, P.E., the assistant NCAT director and manager for the Center’s 1.7-mile oval test track.
Located in Opelika, AL, the research track consists of up to 46 sections of sponsored experimental pavements that undergo accelerated performance testing to simulate the effect on pavements from up to 15 years of interstate highway truck traffic.
“Dr. Powell has experience with Delta S used in test sections at the track and with lab analyses of the rejuvenator, and he suggested we try including it as part of one of our regularly scheduled maintenance resurfacing projects. He also indicated that the information gathered from this application would be useful in augmenting what they had learned about Delta S from the test track experience,” Huner says.
ALDOT approved the suggestion and authorized the rejuvenator trial for a segment of US Route 431 that was part of a resurfacing contract with Midsouth Paving, an Old Castle company. It was further agreed that Dr. Powell would manage the design, production, and paving for the project.
Experiment Goes Forward
According to Alexander Murphree, Midsouth Paving’s quality control manager, they produced liquid asphalt binder for the trial by adding 83 gallons of Delta S directly to 6200 gallons of PG 67-22 liquid asphalt, resulting in a 1.37% rejuvenator/binder blend. In the Astec control room of the 200-tph drum mix plant, operator “Buster” Hicks combined the modified liquid asphalt binder with sufficient RAP and virgin aggregate to yield the 450 tons of 20% RAP mix required for the road test. Hicks maintained materials quantities and temperatures to produce a final dense-graded asphalt mix with a maximum size aggregate of ¾-in. and temperatures averaging about 320°F.
The experimental mix was earmarked for inlaying a stretch of US Route 431 not far from the intersection with US Route 82 near Eufaula. At the test site, where 1-1/2 in. of existing pavement had been milled off and a tack coat of CSS-1h (cationic slow set) emulsion applied, haul trucks arrived from the 12-mile trip carrying asphalt mix with temperatures averaging 300°F.
Midsouth Paving used a Roadtec SB-2500D Shuttle Buggy (material transfer vehicle) to pass asphalt mix from the trucks to the company’s RoadtecRP 190E paver. A HAMM HD+120i roller in vibratory mode performed initial breakdown compaction in three passes right behind the paver, while a Volvo HD118HF roller in static mode provided finish compaction in a single pass.
More Workable, Greater Density
Midsouth Paving’s Murphree said he noticed a difference in workability on the job between the Delta S-modified RAP mix and that of regular RAP mixes installed on adjacent highway lanes.
“The Delta S made the RAP mix more workable for the crew than the regular RAP mix. And we saw a difference in the materials’ densities,” Murphree says. “The cores we took of the regular RAP pavement averaged 93.2 density, while the cores of the Delta S RAP mix averaged a 94.5 density. In addition, lab tests confirmed that the Delta S mix bulk specific gravity was higher than that of regular mix, indicating it had fewer voids
NCAT To Monitor Results
The test paving was concluded in December 2017. Dr. Powell and NCAT personnel under his supervision are monitoring the performance of the Delta S modified RAP pavement, and will provide data gathered on the experimental mix to all stakeholders every six months for two years. The data will focus primarily on pavement ride quality and any occurrence of cracking.