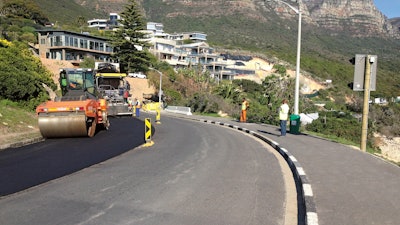
At the Ndabeni Roads and Stormwater Depot in Maitland, the Wirtgen cold recycling mixing plant KMA 200 quickly and reliably produced the BSM mix.Wirtgen
The South African metropolis has large volumes of Reclaimed Asphalt (RA) stockpiled from numerous maintenance works undertaken around the city. This material has generally been used for hard stand areas and shoulder construction, In order to reuse this high quality material, WorleyParsons was tasked to investigate a more efficient and sustainable use for this material. For this reason, the use of a foamed bitumen technology was investigated, and the base layer on Camps Bay Drive was constructed using 100% RA as a foamed Bitumen Stabilise Base (BSM) base layer.
Wirtgen KMA 200 mixes high quality recycling material
Originally, the project consisted of localized road widening to accommodate the proposed MyCiti buses; however, due to the large volume and sizes of the proposed buses, a geometric analysis resulted in the entire portion of the road being widened by 4.6 feet. The proposed pavement design involved a light rehabilitation with the widening area requiring full depth construction however during construction, numerous weak horizons were discovered along the road. The pavement design implemented for construction involved the following:
- 2-inch (50mm) AE-2 Asphalt Surfacing
- 8-inch (200mm) Foamed BSM 1 Base
- 6-inch (150mm) G5 Subbase, natural gravel
- 6-inch (150mm) G7 Selected Subbase, pioneer rock layer
- In-situ
The project was divided into three construction sections. Section 1 from Geneva Drive to Prima Avenue, Section 2 from Prima Avenue to Rontree Avenue and Section 3 from Rontree Avenue to Houghton Road.
In order to ensure more uniformity and better quality of the mix, a static mobile mixing plant was specified for production of the BSM.
Proper recipe is decisive
Power Construction was appointed to carry out the construction of the works with Milling Techniks carrying out the production of the BSM using their Wirtgen KMA 200.
During construction, the stockpiled RA was sent for technical testing at BSM Laboratories in Durban. The design was carried out on three design options using the two dedicated stockpiles of materials from two sources which were created for the project by the city. The design options included:
- 100% Reclaimed Asphalt
- 100% Reclaimed Asphalt with 10% crusher dust
- 100% Reclaimed Asphalt with 25% G4 gravel material
Based on the results obtained, the most cost effective option to yield a BSM 1 was the 100% Reclaimed Asphalt mix design using 2.1% foamed bitumen with 1% cement.
The proper recipe and professional BSM producing of the Wirtgen cold recycling mixing plant were the key factors for a successful project. Immediately after paving with a Vögele paver and compaction with Hamm rollers, parts of Camps Bay Drive could be reopened to traffic.Wirtgen
In order to ensure an adequate quality of the BSM and consistency within the mixing process, Power Construction, Milling Techniks and WorleyParsons created a quality system tailored for the BSM production using the KMA. This was implemented to ensure the mix met the BSM 1 specification throughout the project. Once the BSM was produced, the material was either placed on site immediately or protected and stockpiled at the Ndabeni Depot.
BSM quality check before paving is mandatory
The BSM was paved using a heavy-duty tracked paver from Power Construction in two 4-inch (100mm) thick layers in the same process.
The process used to get the required 100% Minimum Dry Density (MDD) compaction was as follows:
- Paving 4-inch (100mm) thick BSM layer and allowing for bulking of 1.1 to 1.6 inches (30 to 40 mm)
- Applying primary compacting using a 12-tonne tandem drum roller
- Paving the second 4-inch (100mm) thick BSM layer on to the lower half of the layer
- Applying primary compaction using a 12-tonne tandem drum roller
- Applying final compaction using two pneumatic tire rollers (27-tonne PTR) until compaction was achieved.
Before starting with paving and compaction, a testing of the BSM was undertaken by Soillab who established a testing rig in accordance with the TG2, 2009 specification. Acceptance control was carried out on the Indirect Tensile Strength (ITS) and MDD taken from the batching plant and site samples.
After the rehabilitation project, Camps Bay Drive in Cape Town presents itself 4.6 ft. broader and therefore much more secure to accommodate a constantly increasing traffic volume.Wirtgen
Project provides important insights for cold recycling applications
The Camps Bay Drive rehabilitation project allowed for numerous lessons when dealing with BSM’s and more particularly 100% RA BSM’s. The following lessons were learnt during the project:
- Static mobile mixing of BSM’s should be undertaken in the summer months in the Western Cape region due to the weather conditions. Low temperatures and high moisture contents result in a poorer quality product.
- An impact crusher should be used to crush the oversized RA. This may create more fines in the mix as well as reduce the need for stockpiling of the oversized RA.
- Planning and training of the operators prior to the trial section is crucial as this product is not an asphalt material and different placement and compaction methods apply.
- The 100 RA BSM has voids within the mix and hence when inclement weather is eminent, the BSM should be sealed to prevent the ingress of water.
Cold recycling with foamed bitumen: top quality at reduced cost
The following positives were established during the product when using the 100% BSM:
- The design is very versatile and minor changes to the RA and mix design do not have a significant effect on the quality of the BSM.
- The material behaves extremely well under early trafficking.
- There is a large cost saving when using the 100% TA which amounted to approx. 2,95 Euro per m². This cost only includes the material cost saving and not additional traffic accommodation and time cost savings.
- The cost could be further reduced by producing the material closer to the site or mass producing the material as the greatest cost component of the BSM production is the haul of the RA and BSM to the site.
Overall, the project was a major success. During the project, approximately 8,150 tonnes of RA (4,200 cubic meters) was processed using 165 tonnes of bitumen and 78 tonnes of cement. Using the RA within the pavement structure provides a much more cost effective and sustainable solution for the future with depleting aggregate resources.