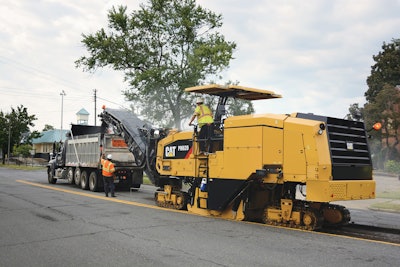
It’s a well-shared sentiment that paving companies do not like to see another companies’ machine in front of them running the mill while they’re doing the paving. Add that to the fact that many paving companies are at the mercy of the milling contractor’s schedule and it makes sense that many paving contractors want to be their own source, but be careful before jumping all in.
“Contractors want to have control over their own operations and if they sub-out their milling, that can be a complexity within their business,” A.J. Lee, product manager for milling machines with Caterpillar, Inc. says. “But there is math at play that contractors need to be aware of before buying their own machine.”
Many companies are contracting out milling services on an annual basis. Is what you’re paying for these services annually, over multiple years after costs and inefficiencies, more than what it would cost to own and operate a mill? That’s where contractors need to look long and hard.
Whether you’re a dedicated milling contractor or a paving contractor looking to bring this service in-house, there are many things to consider before making a purchase. Understanding the full cost of ownership before jumping in to any large purchase decisions is the best place to start.
Can You Staff It?
There is a reason nearly 40% of the industry are dedicated to just milling. This is a specialty business that requires experience and dedication to get the job done right. Whether your company has 15 milling machines in its fleet or you’re considering purchasing a mill for the first time, you first need to consider if your company even has the staff to run this new piece of equipment.
“If you’re going to be going out and actively bidding milling jobs, you first and foremost need to decide if you have the crew to run it,” A.J. Lee, product manager for milling machines with Caterpillar, Inc. says. “A mill is a big complex machine that requires an operator that can run the machine efficiently in order to win business repeatedly is key.”
And it today’s competitive labor market, it can be hard to find quality operators that can complete this specialty work.
“The first thing contractors need to understand is if you don’t have a quality crew, it won’t matter who makes that machine, it’s not going to what it’s designed to do,” Tom Chastain, milling applications specialist at Wirtgen America says. “That’s the biggest things contractors need to understand right out of the gate when considering any equipment purchase.”
Work Load Determines Size
Once you’ve determined you have the staff to run the machine, you need to make sure you have the work to continually feed it. There is nothing worse than a huge piece of iron sitting idle for days without the work to keep it busy.
“This is not a machine you bring out and use once a month,” Lee says. “In order to manage your costs, you need to be really aware of the business in order to keep the machine running. Crews that are running their mills continuously are putting 1,000 hours on their machine easily with many of them putting up to 1,800 hours on it.”
One you decide you have enough in-house work to keep a mill busy for a few years and make it a part of your internal services, then you can look at size.
“Paving practices, the common applications and project requirements will help in selecting the proper machine,” Kyle Hammon, product manager for mills, stabilizers and brooms at Roadtec says. “What cut width, cut depth and production levels will be necessary from the machine most often? These factors will also help determine the most suitable horsepower and size class of the machine.”
Smaller commercial mills are often used for parking lots, shoulders and patching. The cut width of these machines ranges between 2-ft. and 5-ft. These machines are nimble and capable of reaching more confined areas. However, they can be limited in overall production due to cut width and horsepower.
Half-lane machines have the benefit of versatility. They have more mobility than the full-lane machines, but also more horsepower than the smaller mills.
Full-lane machines are large, high horsepower units designed for high production milling of highways and interstates. Niche contractors who really have the time to use them are going to be more apt to purchase these machines.
“Smaller units are versatile in tighter areas such as parking lots and neighborhoods, but can require more passes to accomplish the same amount of work (4-ft drum vs. 7-ft. 3-in. drum.),” Matt White, product manager with BOMAG says. “Half-lane units are extremely popular because they allow for easy transport, powerful and efficient operation and versatility to maneuver in reasonably small areas. Large, full-lane units can easily remove large sections of pavement very rapidly.”
But, the larger the machine, the more support that equipment is going to need.
“Many times, the old adage “bigger is better” does not always hold true,” White adds. “Many times contractors can comfortably use a 600-700hp mill just as effectively as a 900-1000hp unit due to availability of dump trucks. A larger machine will require fleet of trucks to handle the large amount of freshly milled material. If the job site does not allow, due to traffic or distance from the dump site for example, the bottleneck will certainly not be the mill. I have seen many times where the mill waits 45 minutes on trucks to return.”
In addition to relying on haul trucks, a full-lane machine is also more difficult to transport from job to job.
“In a lot of states, full-lane mills are hard to transport fully-assembled because they are considered super-loads,” Chastain says. “It might be difficult to gain that permit so you really need to just consider what that machine is going to be doing. If the machine is just going to sit on the interstate and go, then you can consider a full-lane. But if you’re milling residential street, a full-lane will be overkill and you might damage that thin asphalt with the weight. Half-lane machines are great all-around versatile machines where you can do city streets, parking lots and interstates as well”
The Five C’s
The basic systems on the milling machine will get the job done for you every day. The components you choose will help the machine to live up to those tasks that you’re putting before it.
Crawlers/tracks
Many milling machines are configured with either three or four tracks. The difference between the two is essentially preference.
“Track configuration is an important consideration,” Hammon says. “Both 3-track and 4-track configurations are available. In a 3-track configuration, the rear steer function is more effective as the single rear track is free to turn without interference from the side wall of the cut.”
Cutter System
Application will also determine the cutter system. Standard milling will only require a standard drum, but you need to understand the specifications that you’re working under and the wear those systems go through.
Key attributes of the cutter drum are tooth spacing and lacing pattern. Tooth spacing can range anywhere between the industry standard (5/8-in.) and a micro-mill pattern (0.2-in.).
“Drum configurations can vary from 6mm tooth spacing (with 15mm standard) to 25mm, so this must be a consideration,” White says. “Generally, the application will determine what options and size of machine will be needed.”
“Some projects will have a smoothness specification, or the spacing of the drum itself can be specified,” Hammon says. “Micro-mill drums are used exclusively for shallow cut depths that are often followed by a thin overlay of asphalt. The lacing pattern can also be modified to provide a “double hit” drum. This is a more versatile option that will also provide a smooth surface pattern with more flexibility in cut depth.”
“All the abuse happens inside the cutter housing,” Chastain adds. “Having a durable and well-designed system will help improve job quality and productivity.”
Conveyors
“Conveying capacity is huge,” Chastain says. “If you don’t have the conveying capacity then you can’t get the material out so the machine is going to struggle more. You want to make sure you have ample capacity so you can do those deeper cuts and keep your production numbers up.”
“Most modern milling machines are equipped with a front-loading conveyor system, tracks and grade control as standard,” Matt White, product manager with BOMAG says. “Only with smaller units is there a choice between a tracked or wheeled unit, conveyor or windrow. This will come down to application and cost.”
Controls
“The controls on the machine, whether it be grade control or other integrated systems that the machines may have, will help you get the most out of the machine,” Lee says. “As the shortage of labor becomes more prevalent, it’s going to be more important for controls to have common platforms so operators can easily fill gaps on different crews. Controls should be easy to understand so that you can potentially pull an operator from a paving crew and have him be able to easily pick up what they need to do on a mill and vice versa.
Comfort
Operators are the key to the success of your jobs and making sure they’re happy means they are going to be productive for more hours in a day.
“Milling isn’t typically seen as a glorious job,” Chastain says. “Standing out in the sun for 12-14 hours a day starts to take a toll on people. Making the machine easy and comfortable to operate are big things to consider before buying."
Vibration can also wear on an operator so consider choosing a mill that where the operator platform is isolated.
"It's important that the entire operator platform is isolated from machine vibration," White says. "The BM2200/75’s entire operator platform is isolated from machine vibration. By utilizing the weight of the entire platform onto large isolation dampeners, vibration is nearly eliminated for the operator. This fights against long-term nerve damage that can occur from consistent exposure to vibration."
Seats, canopies, cabins and easy to understand controls will also play a factor in increasing the comfort of your operators.
“Careful consideration should made to look at all aspects when choosing the right mill,” White says. “Ease of operation and operator comfort is a tremendously important portion to consider. I’m a firm believer that if the operator(s) job is made easier, that will translate into better overall care of the machine, increased production and decreased down-time!”