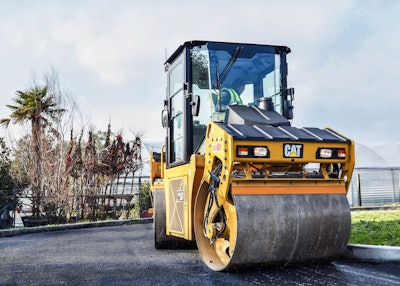
The paving industry relies on compaction to increase pavement density and extend pavement life. A study by Washington State concluded that the life of a pavement can be extended by two years for every 1% increase in final in-place density achieved. It makes sense then that most states incentivize contractors for achieving and exceeding density numbers.
“Density is not only a top quality indicator, in terms of how long the pavement will last, but it is also a top pay item in most state specifications,” Todd Mansell product application specialist for Caterpillar, Inc says. “In most states, contractors are paid incentive or disincentive (financial penalties), based on the final, in-place density of asphalt on the roadway. In extreme cases of low density, contractors may be required to remove and replace the new asphalt if it does not meet density specifications.”
This is why managing density is such a key issue at this year’s World of Asphalt conference in Indianapolis. Mansell says there are many factors that contribute to contractors having to “chase” density on a jobsite, but there are four main things you should pay attention to. If you can’t make Mansell’s session at the show, A Practical Approach to Managing Density on Wednesday February 13th at 9:30 a.m., we have you covered here.
1. Training
Training plays a big role in helping roller operators know what factors affect density. This includes how the settings of amplitude and frequency on steel drum vibratory rollers and tire pressures on pneumatic rollers affect the ability to achieve density (see sidebar).
“Knowing when to make changes and what changes to make are key to being successful,” Mansell says. “Training helps operators identify why they are not getting density. If it is paver speed, they know that, they can speak intelligently to their manager or foreman to slow down the paving operation.”
However, training is only effective if there are people in the organization who are willing to enforce what needs to be done, for example, slowing down the paver or adding more rollers to maintain a higher paving speed.
“The paver operator and crew must understand how their job affects compaction as well,” Mansell adds. “It’s a TEAM effort to be successful with density on the road.”
2. Temperature
Creating density is easiest when you’re at the highest temperature for the type of mix you’re using. Typically, asphalt comes out of the plant at about 300° F. At that temperature, it is relatively low viscosity and is readily compacted. As the mix cools, it sets up and compaction becomes increasingly difficult.
“Whether it is conventional hot mix or warm mix or any other type asphalt mix, it needs to be rolled and compacted while it is hot,” Mansell says. “Asphalt has a relatively short shelf life before sufficient compaction cannot be achieved.”
3. Proper Roller & Rolling Pattern
The rolling pattern affects density primarily as it relates to making the required number of roller passes while the mix is still HOT. The required number of roller passes is determined in a test strip or control section. Most times, this is simply part of the first day’s production. An efficient rolling pattern that covers as much of the paved area in as short amount of time as possible is generally the best approach to a rolling pattern.
First, you have the breakdown roller which develops the majority of the density in an asphalt layer. It works immediately behind the paver where the asphalt is the hottest and it must match the production and speed of the paver.
According to Mansell, steel drum vibratory rollers are most often used directly behind the paver as breakdown rollers and they will achieve the largest increase in density while the mix is at its hottest coming out behind the screed. .
Typically, pneumatic tire rollers are used in the intermediate position behind the breakdown roller, although pneumatics can be used very successfully directly behind the paver in the breakdown phase of compaction.
“Using pneumatics for breakdown directly behind the paver is more common in northern states where colder temperatures dictate achieving density as quickly as possible,” Mansell says. “It takes a skilled operator to run a pneumatic tire roller directly behind the paver while preventing mix from sticking to the tires.”
Steel drum rollers build density from the top down with successive roller passes, whereas pneumatic tire rollers build density ‘bottom up,’ making them VERY effective in the breakdown position. The kneading action of the rubber tires also aids greatly in achieving a more uniform density throughout the depth of the asphalt layer.
Lastly, there are finish rollers whose goal is to clean up marks left by previous rollers. Finish rollers may also achieve additional density gains, however, it should not be expected in most cases.Static steel wheel rollers are primarily used as finishing rollers because they produce the smoothest surface of any roller type.
4. Communication
Preparation, planning and training are key components of achieving optimal asphalt compaction, but they mean very little if none of the above factors are being communicated and implemented.
“Proper communication is essential to achieving density,” Mansell says. “As noted above, if the root cause of not achieving density is related the paver moving too fast and the rollers having to keep up, the roller and paver operators MUST communicate to each other and figure out the correct paver speed that allows the rollers to keep up with the paver and maintain 10 – 12 impacts per foot. This is just one example.”
Keep in mind that rollers are the last piece of equipment to touch the mat after it is placed and are the last opportunity to “undo” the smooth mat that the paver has placed. Mansell says always have a “Plan B” if density is not being achieved and a means to communicate that to the rest of the crew.
“Take pride in your work and work as a TEAM in order to accomplish a quality job that you can be proud of,” Mansell concludes.