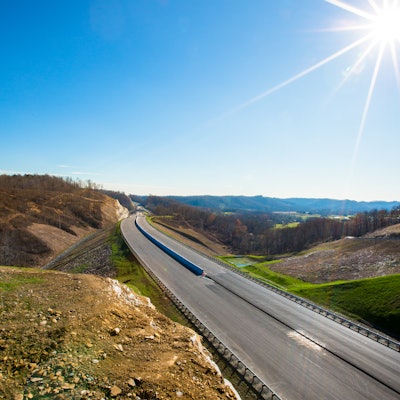
The John R. Jurgensen Company made history by helping complete the Ohio Department of Transportation's (ODOT) massive Southern Ohio Veterans Memorial Highway (State Route 823) project. And they helped make it happen in less than four years —three years and eight months, to be exact.
Finished in November 2018, the Portsmouth Bypass helps drivers avoid approximately 26 mi. of U.S. routes 52 and 23 through the City of Portsmouth in Scioto County. By avoiding 30 traffic signals, 80 intersections and 500 driveways, ODOT estimates a travel time savings to be 16 minutes.
This massive project was able to be completed in such a short amount of time due to the Public Private Partnership (P3) ODOT entered with the Portsmouth Gateway Group (PGG). While many asphalt contractors may not be familiar with P3 projects, Jurgensen successfully navigated the complex P3 environment and looks forward to more projects of this massive scale.
Bid & Build
The Portsmouth Bypass has been a gleam in ODOT’s eye since the 1960’s (see sidebar) but they were only able to move forward with the full scope of the project when the Private Public Agreement (PPA) was completed with PGG. The agreement paired ODOT and PGG with a highly detailed project, cost and time commitment – bringing the best value to the public via private expertise through an effective partnership.
With a P3 project, many project developers insist on receiving multiple requests for qualifications (RFQ) before the request for proposal (RFP) stage hits. The RFQ for this project went out in June of 2013 and the project was bid in September of 2014. Financial close, which served as the award for the bid, happened in April of 2015. For the project's 20 million cu. yds. of earthmoving, Beaver Excavating was averaging 1 million cubic yards of excavated material a month with six Hitachi machines running. The project's “earthmoving” consisted of 97 percent rock — sandstone, shale and limestone — that was blasted every day. Beaver Excavating also made cuts as deep as 200 ft. and used the material for fill on other parts of the project which included 3-ft. of shot rock placed for a roadbed layer prior to paving.
Jurgensen was invited to be a part of a joint venture that included Dragados USA and Beaver Excavating. The project consisted of excavating twenty million cu. yds. of rock, paving sixteen miles of four-lane divided highway, constructing twenty-one new bridges and five new interchanges. Construction activities began during the summer of 2015 while the design was still in process. Mainline paving occurred between April of 2017 and November of 2018.
“ODOT is our largest customer traditionally, so when they wanted to build this, their largest project to date, we were very interested,” Chris Kunz, Jurgensen director of project management says. “Our local ties to the area with both asphalt production and aggregate capabilities, as well as our local workforce, made us a key part of the group.”
For the project's 20 million cu. yds. of earthmoving, Beaver Excavating was averaging 1 million cubic yards of excavated material a month with six Hitachi machines running. The project's “earthmoving” consisted of 97 percent rock — sandstone, shale and limestone — that was blasted every day. Beaver Excavating also made cuts as deep as 200 ft. and used the material for fill on other parts of the project which included 3-ft. of shot rock placed for a roadbed layer prior to paving.
Intricate Paving Process
After the excavated rock bed was placed, it was Jurgensen’s turn to work. The company brought in their Astec Six Pack Portable Plant to service this project.
“Our company purchased the property adjacent to the project where the plant is now located,” Kunz says. “We installed 3 silos at this site in order to achieve both high production and high quality. Another Jurgensen Company, Valley Asphalt, supplied the mix.”
The base was a typical ODOT 302 bituminous mix placed in a 4-in. lift. 230,500 tons of mix was placed for the base. The intermediate and surface courses were both ODOT 448 mixes. The intermediate layer consisted of 94,500 tons of Ty 2 placed 1.75-in. thick. 63,000 tons of surface course was paved 1.25-in. thick.
“Since this project was constructed with a 3-ft. shot rock road bed layer under all of the pavement, it allowed a thinner than normal pavement section,” Kunz says.
During the paving process, it was very important to Jurgensen and the project owner to minimize longitudinal joints and specifically to not have a joint between the traveled lanes. By not creating a longitudinal joint between the lanes, the developer, who is maintaining this pavement for the next 35 years, is expecting a much longer service life than with a normal paving process.
“In order to accomplish this, we purchased a special, heavier screed from Caterpillar,” Kunz says. “This allowed us to pave 24-ft. wide for the vast majority of the 16 mile roadway on the surface lift. The benefit to our team was the education that we acquired doing this. We are now able to utilize this method for other customers in other locations.”
99% of the mix was placed with a Caterpillar AP1055F paver with the specialized high density screed and most of the rolling was done with Caterpillar CB54 XW rollers. The intermediate and surface mixes were installed with the use of a Roadtec SB-2500 Shuttle Buggy to prevent segregation. The company also rented a Vögele Super 700-3i paver to pave the 4-ft. shoulders on the project.
“The smoothness tolerances on this project were tighter than a typical ODOT specification and this paving technique worked well in achieving the goal,” Kunz says. “The project had very strict surface tolerances due to the anticipated and desired long life. These tolerances were far superior to typical work and required greater oversight. Our crews learned to adapt to the standards quickly.”
Like any project, Jurgensen encountered challenges with schedule, tolerances, yield and access to the areas.
“Access to work areas was very difficult during the placement of the base and even the intermediate courses,” Kunz says. “Paving was happening in some areas where bridges were still being constructed and earthwork was taking place. We had to work out strategic ingress and egress points in this geographically challenging area. This required out of the box thinking at times to get areas covered.”
The aggressive schedule on the project required Randy Westendorf, Jurgensen’s project manager, to constantly formulate a long range plan. Weather and other factors continued to make this planning process very complicated for the team.
“Jurgensen was able to use and enhance our relationships with ODOT Central Office staff as well as the local District 9 personnel to partner and make tough decisions throughout this project,” Kunz says. “ODOT has embraced the partnering concept and this worked well with the P3 model. Situations arose that required give and take on both sides but through good communication and partnering, we were able to keep the project on track.”
With a P3 project, the private sector is looking at what’s the cheapest cost to build and operate this piece of infrastructure for an extended period of time. The challenge then is getting the contracts right so every team member gets what they want. Since this project was a P3 and Jurgensen needed to ensure they met their contract goals, they had a self-imposed yield goal that was very tight in order to minimize any overruns. Kunz says his crews worked diligently to surpass their goal by the end of the project.
Kunz adds that even though this may have been the most complex project due to the P3 environment and the quality standards needed for such a long life pavement structure, they are looking for more opportunities to work in the P3 realm.
“This was our first P3 project and with the experience we gained, we are looking forward to the next opportunity,” Kunz concludes.