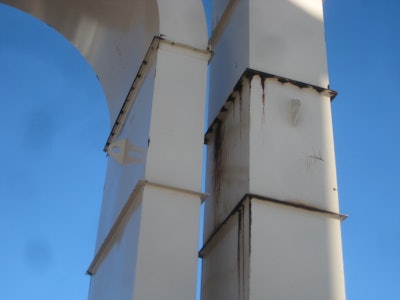
As I travel around our great country visiting asphalt plants some very important questions arise. One question I am often asked is, “What is the best burner fuel to use in my plant?” In reality, the answer to this question is complex. So I will rate the fuels "Best to Worst" in each category:
EMISSIONS Reason Result
1- Natural Gas Very Clean Burning Easy to be DEQ Compliant
2- Liquefied Natural Gas (LNG) Very Clean Burning Easy to be DEQ Compliant
3- Propane Very Clean Burning Easy to be DEQ Compliant
4- Diesel Not Clean Burning Harder to be DEQ Compliant
5- Reclaimed Fuel Oil (RFO) Very Dirty Burning Very Hard to be DEQ Compliant*
COST per TON Reason Result
1- Reclaimed Fuel Oil (RFO) Cheapest Fuel to acquire. Fuel of Choice for Bean Counters*
2- Natural Gas Cheap & Clean Best Choice for Owners
3- Liquefied Natural Gas (LNG) Cheap & Clean Choice of Owners who can’t get NG
4- Propane Cheap & Clean Choice of Owners who can’t get NG
5- Diesel Expensive & Dirty Choice of almost no one
COST LONG TERM Includes Maintenance
1- Natural Gas Very LOW Long Term Operational Costs
2- Liquefied Natural Gas (LNG) Very LOW Long Term Operational Costs
3- Propane Very LOW Long Term Operational Costs
4- Diesel Higher Long Term Operational Costs
5- Reclaimed Fuel Oil (RFO) Highest Long Term Operational Costs*
* RFO is a very dirty fuel. It is composed of re-refined motor oils, transformer oils, gear oils, literally any oil that the refiners can put into it. Sometimes this can include components that simply can’t be burned. Things like antifreeze often get included.
So you ask, what problems are associated with RFO?
1. Very dirty fuel. Sulfur content is high.
A- High sulfur content causes bags to rot in baghouse.
B- Sulfur also corrodes the tube-sheet and walls in your baghouse.
2. Almost impossible to pass an EPA Method 202 test during a stack test.
A- High particulate content readings in Method 202 test for Condensable.
B- Dirty components in fuel are read as particulate emissions in the "back half." If the
emissions limit for particulate is .02 and your baghouse emissions are .015, a high
reading on the "back half" will cause you to fail a Stack Test. Not good!
3. Every plant operator who’s used RFO has stories about when they couldn’t light the burner.
A- Contaminated fuel is common. Many hours of production is lost due to bad fuel.
B- Ancillary equipment like fuel oil heaters occasionally cause failures.
C- Life of fuel pump and regulator is shortened due to heat and contamination.
4. Burner maintenance is also increased. Dirty fuel eats filters and plugs nozzles in the burner.
If you take these issues into consideration, initial cost is the only reason to use RFO.
Personally I have never been a fan of RFO, but it takes a lot more than my opinion to get companies to move away from it. Especially in portable plants. Cost drives everything in asphalt production. Following this train of thought, I would ask that plant managers consider the long-term costs of RFO. Maintenance costs. Air quality costs in terms our kids’ future. Our future.
These things are why I really believe that after critical analysis, plant owners should move away from RFO and on to cleaner burner fuels. Portable plants have options these days that weren’t available to me when I was running plants on a daily basis. Now LNG is available, and propane. These fuels were much more difficult to get just fifteen years ago. But now those options are easily attainable.
It is my opinion that the best over-all fuel for any asphalt plant is natural gas, LNG or propane. These fuels are the cleanest operating and require the least maintenance to operate over the long term.
At CM Consulting we convert plants from RFO commonly. As one of the largest Hauck Burner Dealers in America we can arrange for all the components for the conversion to be delivered to your facility. Should the reader wish to do a cost analysis on converting their plant to LNG or propane, feel free to call or text 541 490 4269.