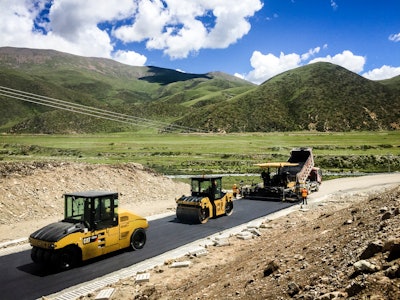
Rubber-tired rollers or pneumatic rollers can help asphalt contractors achieve a better base, better density and an improved product appearance, still many paving companies don't have these rollers in their fleet.
"Pneumatic rollers are avoided by some due to challenges with tires picking up asphalt and preferred by others due to their ability to get great compaction," Brian Nagel, global sales consultant at Caterpillar, Inc. says. "However, many state specs actually require a pneumatic roller because of its ability to get great compaction. Their weight flexibility makes them versatile in different roller positions as well as mixes designs."
Pneumatic rollers use static pressure in both vertical and horizontal directions to reduce air voids in material which creates compaction. This is often referred to as kneading or manipulations and helps bring compaction to materials differently than traditional static rollers or vibratory rollers.
"Pneumatic rollers offer a different type of compaction and that's more of a bottom up style compaction as opposed to a top down," Brad Belvin, sales & marketing manager at Sakai says. "The way a vibratory roller works is they go over the mat and then build the compaction from the top down. When pneumatic rollers get on the mat, they knead the material and they'll build compaction from the bottom up so it gives you a more uniform compaction when used in combination with everything else."
By having a horizontal aspect to the pressure, aggregate can be moved more than just vertically helping decrease air voids. This movement also help to seal a surface creating a tighter finished compaction layer.
During soil compaction, pneumatic rollers are particularly helpful in creating a uniform surface.
"Often you use these large rubber tire rollers in conjunction with a smooth drum soil roller to ensure that there is no bridging and you've got uniform compaction across the full width for the material," Richard Evans, HAMM product manager at Wirtgen American says. "These machines are also used as a finish roller during full-depth reclamation projects due to the advanced water system on these machines. With the water system on the tires, we can keep that surface moist, then we can pull the fines to the surface and it help seal that surface so no moisture gets in after we're done compacting."
When not used for soil applications, pneumatic rollers are used in an intermediate roller position in an asphalt paving train. This position works well because a double drum roller has already completed the breakdown phase and the material is still hot enough to keep tires warm and prevent material pickup. Pneumatic rollers are ideal for applications where vibration should be avoided such as next to buildings, on bridges and thin lift asphalt overlays.
These machines are also proving to be an asset when obtaining compaction along longitudinal joints and around manhole covers as they knead materials into these tight areas while removing air voids.
"If you've got a manhole cover and you're running this with a with a steel drum roller, you will bridge it and it will sit on that manhole cover," Evans says. "You're not going to get compaction right around the edges with a steel drum roller where a tire is a little bit more manipulative."
Pneumatic tire rollers are also well-suited for obtaining compaction in the tricky "tender zone."
"Temperature is always is a big concern when you're running asphalt and you want to get on the mat as close to the paver as you can to get that initial path," Belvin says. "The quicker you can get into rolling, the better, but then there's a period of time called a tender zone, depending on the mix, where you kind of have to get off of the mix and you can't do anything. Well, the only thing that you typically can do during that time is use a pneumatic tire roller because it doesn't displace the mix like a sealed drum machine would do.
"Not all asphalt mixes are going to be the same and because of that, you're going to want every tool in your bag to solve all your compaction needs," Belvin adds.
Upgrades Improve Performance
Over the years equipment has improved to better meet the needs of the challenging jobsites contractors are experiencing while also improving accountability.
"Caterpillar focuses on reliability and durability while maintaining a low owning and operating costs when making upgrades," Nagel says. "This combination provides the most value to our customers and ensures that they can maximize their uptime. One area not to be taken lightly is the use of Cat engines in our pneumatic rollers. By using a Cat engine, our dealers are truly the one stop shop when it comes to servicing the machine."
A properly weighted machine will also improve performance which is why manufacturers have focused on improving ballast systems.
"Cat pneumatic rollers have ballast compartments that are water tight and internally baffled which means there is a lot of flexibility in what materials can be used for increasing the machines weight," Nagel says. "From the factory a customer can choose to go with steel blocks or they might choose to purchase a machine without ballast and then add sand or water as need be. When no factory ballast is installed, it’s important to maintain equal weight balance between the front and rear of the machine which will aid in uniform compaction."
For this reason, manufacturers are working to make it easier to change out the ballast on their machines.
"On the new HP Series rollers, the weight can be simply and flexibly adjusted using prefabricated ballast bodies," Evans says. The ballast spaces can be filled with a combination of concrete, magnetite and steel materials enabling the overall weight to be varied in precisely graduated stages. The weights now are also all centrally mounted and easily accessible by means of a forklift to be able to change the weights in the middle of the machine."
Some manufactures are even trying to move away from the ballast system.
"At Sakai, we have a vibratory pneumatic roller which gives you a 10 ton static weight roller, but then there's a centric weight that's variable placed and will give you different compaction levels," Belvin says. "With this feature you don't have to have multiple machines or ballasts, it's just a simple knob on the operator dash that they can change to get those different levels. It's like having four or five different pneumatic tire rollers built into one and the only thing that needs to change at all is just a simple switch on the dash."
Intelligent compaction (IC) is becoming required on more and more jobs not only to help improve the quality of the final product but also to document what was done and that technology has made its way to pneumatic rollers.
"Intelligent compaction gives an operator the ability to see where they've gone onto the mat, how many times they have rolled the mat and a screen that changes colors with each path," Belvin says. "This allows you to take an inexperienced operator and get them rolling to great compaction levels and not missing any spots right away because they can see a direct visual representation of where they've compacted so far by how many passes, and if they've missed anything."
IC is also becoming a requirement for contractors on DOT jobs as it gives project owners access to compaction data once a job is complete.
"Caterpillar has been offering this technology on their pneumatic rollers for over five years and it consists of a display mounted conveniently in the operator’s field of view and displays both mat temperature and pass count mapping," Nagel says. "Data can be viewed real time or offloaded to the cloud for further analysis or documentation purposes."
Tires Make a Difference
While most operators are familiar with servicing a steel drum roller, operating a machine that runs on tires is a bit different.
"All of our machines are eight wheel rollers and they offer twin pivots steering on the front so even in a tight turn, all four wheels remain under the frame of the machine for stability," Evans says. "And if you were to drop over a curb, or uneven ground, the hydraulic suspension on the front will balance the machine so it always stays level and stable."
"Cat pneumatic rollers are designed to be simple to maintain and service," Nagel says. "The most important aspect of the machine are the tires and specifically that they have uniform inflation pressure which will translate to uniform compaction. One low tire will cause different ground contact pressure and lead to uneven compaction. Caterpillar has a solution to this maintenance task called air on the run. It is a system that automatically maintains the tires air pressure to an operator specified value via an onboard air compressor. This eliminates the need to manual check pressure ensuring even compaction."
HAMM also has this feature on their machines which allows operators to continue rolling even if there are changes in tire pressure during use.
"As any tire warms up, air pressure increases and air on the run allows you to monitor that pressure from the operator seat," Evans says. "With the push of a button, operators can ensure their tires are maintaining constant contact with the mat for a more uniform compaction."
Avoiding "pick up" of the mat on to the tires is another operation difference with these machines as opposed to steel drum rollers and it needs to be avoided at all costs. If the mix is hot and the tires are cold, you have a higher likelihood of picking up asphalt on the surface of the tires.
"You want to make sure your tires are warmed up before they hit the hot mat," Belvin says. "Many operators will run the machine for 20-30 minutes before it hits the mat to get the tires hot. Sakai pneumatic rollers also have vibratory options and you can turn on that vibration and that generates more friction onto the tire and builds up heat at a quicker time."
Many operators avoid pick up of the mat by spraying down the tires with an additive. Often too much water is sprayed on tires which causes them to cool down and stick even more which is why some machines now have an adjustable spray system to provide just the right amount of spray.
"The additive tank allows you to mix additive directly into the same injectors you spray the water in to," Evans says. "The dosage from the large additive tank with level monitoring can be controlled from the operator's platform in various addition levels. The roller doses and mixes the additive during the compaction in accordance with the specification."
HAMM pneumatic rollers can also be equipped with infrared heating system in extremely cold climates.
Once the tires are hot, you will want to keep them that way which is why many pneumatic rollers feature skirt kits.
"Skirt kits are installed around the machine and they help to retain heat around those tires," Evans says. "This is especially important in cooler climates because you do not want those tires to get cold and pick up asphalt off the mat."
Operators Benefit from Machine Advancements
As with many new machines today, upgrades have been made with the operator in mind. In many construction companies, operators are hard to find and manufacturers are working hard to simplify machines to help flatten the training curve for new workers.
"One thing we've always done and it's a huge selling point that we notice is we keep everything very, very simple," Belvin says. "All of our dashes are just simple knobs and switches that are very easy for operators to understand. If an operator is starting to get into heavy equipment from say working the shovel or rake, we try to keep all of the dash controls very simple, intuitive, and non confusing for these operators."
HAMM has also improved the operator experience with the Easy Drive system.
"All of the machines operate now with the Easy Drive platform which means that all of our machines have common instrumentation and joystick control so an operator can freely move from one machine to another without a big education curve," Evans says. "All the controls and the icons are similar across the range of all our products."
Where the operator sits is also important.
"For safety purposes, the operator sits right in the center of our machine, both forward and backwards," Evans with HAMM says. "This means the sight angle forward and backwards is greatly reduced so they can see a lot closer around the machine."
And visibility is important.
"We moved over from a dual operator station to just a one single operator with a 180° swivel seat," Belvin says. "That gives operators better visibility to the tire edge to the frame so they get a clear line of sight there."
"Cat pneumatic rollers come standard with an operator station and controls that rotate to help give the operator good visibility to the tires as well as job site. An air suspension seat reduces operator fatigue and helps them be more alert," Nagel says.
Finally, while these machines are relatively low maintenance, manufactures have worked to improve serviceability access points as well.
"At HAMM we attached importance to efficiency and safety when it comes to maintenance," Evans says. "For example, all daily maintenance items are situated on the right-hand side of the engine. Engine access has also been intelligently and safely designed on the HP series: the steps are integrated in the outer contour and are opened outwards in one easy operation. Because they visually protrude in this position, the operator cannot forget to retract the steps on conclusion of the maintenance work."