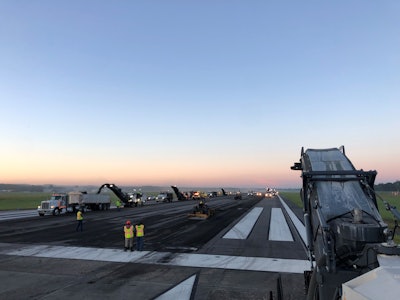
Runway reconstruction projects are not known for being easy. They require extensive planning, extra coordination and an acceptance of risk for delays that might happen during tight timelines. Dunn Roadbuilders knew all of this heading into the reconstruction of Runway 1-19 on Key Field at Meridian Regional Airport and prepared accordingly.
The town of Meridian's Key Field Airport is home to the longest public runway in the state of Mississippi. It had been 20 years since the runway had been worked on and the Airport Authority knew shutting it down for reconstruction needed to happen, but they needed closure time to be minimized. For two years, the Meridian Airport Authority had been planning the rehabilitation of the runway and they knew they had to get it right.
The runway consists of 8,000 feet of asphalt with 1,000 feet of concrete at each end. Dunn Roadbuilders was hired as the prime contractor on the project. They were tasked with coordinating the extensive work that needed to be done.
"The asphalt runway was to be milled, then a stress relief layer was needed to eliminate reflective cracking," Teresa McDonald, project management coordinator at Dunn Roadbuilders said. "Then asphalt leveling was needed to correct the cross slope. This was followed by an asphalt overlay, shoulder material, runway light adjustments due to the leveling, joint sealant on concrete sections, asphalt grooving and striping."
On August 16th 2021, the runway was closed and work began. For 7 days, 24 hours per day, crews worked and flights resumed as usual on August 24.
Milling in Echelon
In order to maximize their time, Dunn worked with a team of subcontractors to execute the project. Milling of the existing asphalt was done in one shift to expedite the work. There were six milling machines on site, working from 7 pm until 8 am the next morning to remove 145,000 square yards of material.
To move this much material in such a short time, Dunn worked with two other milling subcontractors, Huey P. Stockstill, LLC and Mill It Up, LLC, to bring a total of six Wirtgen 220i Milling Machines to the jobsite.
"A lot of effort went into pre- planning the project and coordinating milling and trucking," McDonald said. "We ultimately started milling at the center and checked thoroughly to maintain the correct cross slope. A second machine followed behind on the opposite side of the centerline. All of the other machines followed behind and matched the initial first pass cross slope to maintain the correct slope across each side of the 150-ft.wide runway."
Each machine had multiple dump trucks assigned to it and the material was stockpiled on site to improve logistics. In all, almost 600 truckloads of material were removed for a total of 14,000 tons in one night.
“It was very intense work for those 14 hours,” Jason Wooten, Vice President of Operations at Dunn Roadbuilders adds. “We milled 145,000 square yards and stockpiled it on site to keep our trucks close which allowed our operations to keep moving all night.”
Milling was immediately followed by the stress relief layer, which was performed by another subcontractor RJM McQueen Contracting.
“The project owners knew there needed to be some repairs done due to cracks in the existing pavement, so we recommended a stress layer,” Wooten says. “That would seal the cracks and after the stress relief layer was performed, it would give relief so the cracks would not reflect through to the new surface. This layer would perform double duty, sealing the cracks and not letting them reflect back to the surface course.”
That was completed Tuesday morning and paving of the leveling course began that night.
“The pavement was 170-ft. wide, but the actual runway was 150-ft. Wide,” Wooten says. “The shoulders on the outside were not at a continuous cross slope so we needed to correct that first and now we have a Continuous Slope all across the runway.” The leveling course was a FAA P403 non-polymer mix.
Paving Between Raindrops
As with any project, work has to happen around the weather. This is particularly worrisome when your timeline to complete the work is one week. After the stress layer was installed, crews immediately began the process of paving. August 18th, the second day the runway was closed, crews paved 30-ft. of the 150-ft. wide runway.
“We used a 60-ft. contact ski for the centerline with the milling machines and followed that same design on the first pass with the paver,” Wooten says. “That allowed us to achieve smoothness more easily and we did not have any ride disincentives. The contact skis gave us a smooth ride”
The crew encountered challenges however, when rain showers popped up throughout the paving days.
“We had three or four rain delays that cumulatively were 20 to 24 hours," Meridian Airport president Tom Williams says. "We lost a day due to rain because they couldn't pave on a wet surface. The contractor was phenomenal though. They came into this with the right can-do attitude. Everyone has worked together. They coordinated beautifully.”
“Once we got in on Monday, we never left until the work was done the following Tuesday,” Wooten adds. “All we did was stop and wait for the rain to pass, broom and dry the area and start back up. We had crews working on the project every hour of the 7-day shut down. Dunn operated two paving crews, one day shift and one night shift, who put down around 2,000 tons each shift using only one paving train for the runway surface course. The highest tonnage in a 24-hour span totaled just over 7,000 tons on Saturday which allowed us to make up time due to rainfall the previous days.”
Dunn also made sure they would be able to keep working if any unforeseen breakdowns were to occur.
“We did have backups ready for any breakdowns just in case,” Wooten says. “But reliable and dependable equipment is key to these projects.”
In all, Dunn put down 25,506 tons of asphalt on the runway, finishing the project on time, despite the weather and logistical challenges. The surface course was a standard FAA P401 Polymer mix supplied by APAC of Meridian.
“APAC was geared up and they gave us their plant for the week because we were running day and night,” Wooten says. “Our whole company was dedicated to this site and there was a lot of coordination. The preparation and coordination with the Meridian Airport Authority, Engineering Plus, suppliers, subcontractors and crews in the beginning is what set the stage for this to be a successful project. I am really proud of our team that worked on this project; hard work, commitment and teamwork made this success possible. It was an honor to be a part of a team that was able to execute such a large project in a very short amount of time.”