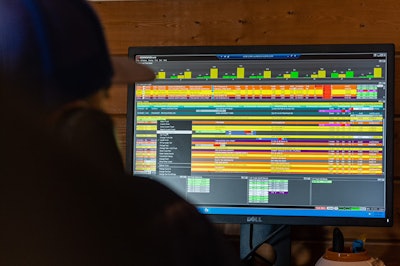
It is estimated that the IIJA (Infrastructure Investment and Jobs Act) will create 2 million jobs over the course of a decade. The “Everyday Counts: Innovation Initiative” issued by the U.S. Department of Transportation in 2017, combined eConstruction with so-called Construction Partnering (aka E-C&P), is an effort to accelerate the adoption of electronic processes. E-C&P calls for training and aid for decision-makers and other key stakeholders, such as State DOTs, contractors and consultants. Electronic material ticket management systems automate manual practices across the industry, eliminating tangible paper tickets and addressing the challenges created by outdated methods for tracking materials and truck assets.
Many successful pilots of eTicketing have occurred nationwide since the implementation of the “Everyday Counts” initiative, and the exchange of electronic ticket data has bridged the eConstruction gap that exists between public agencies and building materials suppliers.
These regulatory changes require the construction industry to change and adapt. Companies are notified of the standard operating procedure for transactions before the ground even breaks. During the bid letting process, one of the requirements spelled out is to submit a line item that specifies that that the company can adhere to eTicketing requirements if they win the bid.
From the time that the bid is awarded to the time that the project starts is usually plenty of time to get prepared and implement eTicketing capabilities. So, a company that is not currently set up for eTicketing might make the choice to bid and work on getting the processes put in place at that time. However, most companies are actively investing in and implementing solutions that enable them to exchange electronic tickets because the IIJA includes money for advanced digital construction management systems and related technologies. The program is funded at $20 million per year, for a total of $100 million, over five years. This funding is a clear indication of the critical role that technology will play in designing and building better, cost-effective infrastructure.
Looking to the Future: A Positive Outlook for Construction Productivity
eTicketing requirements, once seen as a regulatory necessity, have now shown to improve the visibility of trucking operations leading to more efficient hauler management and improved profitability. Stagnant productivity, low levels of digitization, and low profitability plagued the industry.
Now, with the combination of new sustainability requirements, rising cost pressure, skilled labor shortage, and new process approaches and digital tools, companies are realizing that in order to maintain business continuity and stay competitive, digital backbones must be implemented into their operations. According to McKinsey & Company, R&D spending among the top 2,500 construction companies has risen globally by approximately 77 percent since 2013. Additionally, more than 50% of respondents’ companies have increased their overall technology investments.
There’s been a productivity lag in the construction industry for decades – one that costs the global economy $1.6 trillion annually. Lack of technological advancements, lack of communication, coordination issues, and an inefficient use of time are all issues that serve as the gordian knot in construction productivity. Technology can cut through the complexities.
Within supply chain processes, communication is key to success. If materials show up to the jobsite and construction personnel are not ready to receive or use the materials, work can be delayed or come to a halt. If materials arrive on time but do not meet the project specifications, additional deliveries have to be dispatched and construction teams will be idled as they wait on replacement materials. With improved communication through eTicketing, materials are easily located and on track for use at the right place for the right operation; and clear visibility into traceability of material properties and orders ensures that products arrive in the best possible quality, reducing delays and productivity lags.
Businesses can ensure complete delivery and materials traceability and uncover smart insights for decision-making with connected logistics solutions. Drivers have the information they need at their fingertips, including their next ticket, so they can be back on the road to their next job as soon as their current delivery is made. To create more efficient fleet operations, companies are using tracking solutions to map the location of trucks in real time, as well as telematics devices to monitor truck performance parameters, such as engine speed and coolant temperature. These devices provide visibility into fleet operations, monitoring the unloading and loading of trucks and wasteful idling while in traffic or at the jobsite. Once management understands the cause of nonproductive hours in their operations, they can revamp processes for greater efficiencies, including using route planning and mapping solutions to avoid traffic delays.
Combating Inefficient Data Exchange and Mismanagement
Paper tickets end up in a place where data goes to die, so construction companies are approaching solutions providers to enable digital workflows for better management and real-time access to project data.
A range of solutions are available for contractors with flexibility in terms of the eTicketing options that they have to meet requirements, depending on the state and the way that the construction business is set up. For example, if a company owns all of their own trucks, uses third-party trucks, or a mix of both, eTicketing solutions exist that would work well in all of these scenarios. Solutions will vary depending on whether the contractors have control over the paving equipment or not. If they do, some companies provide a set of solutions that could make sense for them as well in that situation.
Depending on the solution the construction company signs up for, they can be up and running in a day or two. Other solutions might require a couple of weeks, depending on the requirements for that project by the state and which approach they want to take in meeting those requirements. Some of these solutions require hardware inside of the truck or on the paver, while other solutions are just an application that can be downloaded to the driver’s smartphone. Procuring hardware might take a little more time upfront, but it can deliver more convenience on an ongoing basis. The application-only solutions can be up and running right away, but it may lead to some additional manual work depending on the scenario.
A good technology partner will offer support throughout the onboarding process, but then also on an ongoing basis as projects progress and evolve. Some solutions require more extensive training for the drivers or the paving crew, so these companies will aim to serve as an extension to the team to ensure that each constituent is properly trained and is capable of fully utilizing the technologies at use.
Tarun Nimmagadda is the VP of Product Strategy at Command Alkon. Before being acquired by Command Alkon, Tarun served as the CEO and Co-Founder of Ruckit.