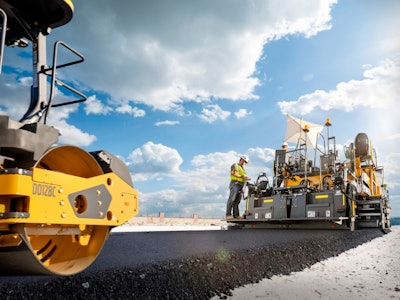
There are many different types and styles of rollers available for compaction, but not every roller is right for every job.
Factors that you should consider when choosing the right roller for your job include:
Type of material that will be compacted (dirt, sand, gravel, asphalt, etc.)
Budget
Size of area
Site layout (open area or confined areas)
Transportation to and from the job site
Take a look at the types of rollers available and decide when, where and how to use them on your projects.
Soil Compaction
When a new road or structure is being built, the foundation will need to be compacted before final construction can begin. The new surface is often loose and unstable, and needs to be compacted before structures are built upon it.
There are two main types of soil compactors to accomplish this task.
Smooth Drum:
These rollers consist of large, smooth steel drums that use a combination of impact, vibration and static pressure to compact materials such as sand, ballast and gravel. They are the most effective in compacting silty or sandy soils with the fewest passes.
Sheepsfoot or Padfoot Drum:
This style of rollers have many raised lugs called "feet" on the roller drum. The feet provide a tamping action and change the surface area of the roller drum, which enables the roller drum to apply more pressure per square inch.
The roller operator can increase the pressure on the feet as needed by filling the drum with wet sand and other materials. Typically sheepsfoot rollers are used with silty or heavy clay or cohesive soil surfaces.
Single or Double Drum Style:
Soil compaction rollers can either be tandem (double drum) or single(three-wheeled) depending on the project needs.
Tandem rollers have drums in both the front and the back for additional power and faster compaction times. However, the lack of tires results in less stability and traction than single drum versions.
Three-wheeled or single drum rollers have a drum in the front and specialized tires in the back, allowing them to roll over almost any surface.
Asphalt Compaction
Many times asphalt roadways are put down over soil and there are many specialized rollers to use during different phases of asphalt compaction. These can come in single drum configurations, but you usually see tandem rollers operating during asphalt compaction.
Smooth Drum Rollers:
These styles of roller are most commonly used for asphalt compaction but have varying styles and technologies that make them more suited for different applications.
Static Rollers:
Static rollers are used to compact many different types of material, but are used on some jobsites for asphalt compaction. Static rollers are sometimes seen as the final roller in the paving train, used for finish rolling. The primary purpose of finish rolling is to obtain the last little bit of density and to remove the marks, if any, left by the first and second rollers. When needed, finish rolling should be accomplished with mix surface temperature above 175° F.
Vibratory Rollers:
Vibratory rollers are almost identical to smooth wheel rollers except they feature a specialized vibrating component. As the roller compacts and flattens the surface, it will vibrate and increase the compactive effort. Double drum vibratory rollers operate close behind the paver to obtain the initial compactive effort while the mix is still hot.
This “breakdown” rolling, completed with a vibratory roller, should be completed before the surface temperature of the mix falls below 240º F. The breakdown roller should be operated at the highest possible frequency level available for the particular make and model of roller and at an amplitude setting that is dependent on the thickness of the asphalt concrete mat being placed.
Intermediate rolling is usually done with a vibratory roller as well and must be accomplished immediately after the initial rolling is completed.
Oscillating Rollers:
Oscillation is a technology developed to help increase compactive effort even further. With these vibe systems, the drum stays in constant contact with the material allowing the roller to deliver dynamic compaction energy to the asphalt layer as an alternative to traditional vibration. Instead of vibrating the pavement up and down, oscillating rollers stay in contact with the surface, and there are no repeated impacts to the surface for compaction.
This provides more compaction force than static rolling but less force than traditional vibration. Tandem rollers with one oscillation drum and one vibrating drum achieve at least the same degree of compaction as double vibrating drum rollers, but with fewer passes.
These types of rollers are suited for compacting thin lifts, tender mixes, joints, bridge decks or when working near structures. Oscillation is also useful for joint compaction as most asphalt contractors have to deal with hot and cold lanes when they pave.
Pneumatic Rollers:
Pneumatic rollers use smooth pneumatic-tired wheels that overlap instead of steel drums for compaction. Pneumatic rollers use static pressure in both vertical and horizontal directions to reduce air voids in material which creates compaction. This is often referred to as kneading or manipulations and helps bring compaction to materials differently than traditional static rollers or vibratory rollers.
These compactors are mainly used as one of the last steps for compacting both soil for road work and asphalt for sealing purposes.
When a pneumatic tire roller is used as an intermediate roller, it is necessary to keep the tires at the same temperature as the mat being compacted — otherwise the rubber tires will pick up some of the mix from the mat. So when using a pneumatic roller, don’t allow the roller to sit and wait for long periods of time as the tires will cool.
Compaction for All Sizes
Road rollers aren’t the only construction tools used for compaction work. Other types of compactor equipment include the rammer and the vibratory plate.
Rammers are handheld and are best used for small jobs in tight areas. Due to their comparatively lightweight, they can be hand or machine operated, which allows deep vibratory compaction.
Vibratory plate compactors are used to increase the density of a variety of soils and fill any voids. Because they are walk-behind compactors and are smaller in size, these compactors are best used for tight spaces where large equipment can’t reach.
Trench rollers, also called multipurpose compactors, perform well in cohesive soil types that can be very difficult to compact (such as clay). Trench rollers can compact high moisture content in clays by utilizing powerful compaction energy and the kneading effect from their padfoot drums.
Trench rollers get their name because they are often used to compact the soil in trenches. Trench rollers are popular because they are maneuvered by using a remote control - the operator does not stand or sit on the machine while it moves.
Compaction is an important part of any project. Understanding the benefits of each roller can make choosing the right one for your project more efficient. Be sure to always properly train your operators to ensure they are making the most of their work and compacting each surface efficiently to ensure density. Under compaction can cause decreased strength, reduced fatigue life, accelerated aging/decreased durability, rutting, raveling and moisture damage. While over-compaction can affect the integrity of the material and damage the roller.