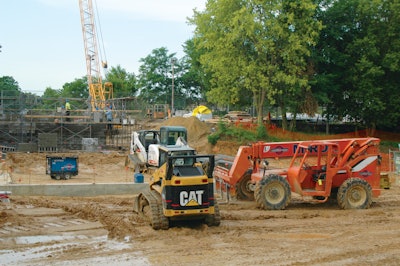
All of the contractors I've spoke with recently have told me that today's business climate is forcing them to cut expenses and take work further from their home offices. Considering the added costs and logistical problems with working further a-field, it's a shame that so few are working hard to answer the question, "Which equipment can I rent at lower cost than owning?"
Equipment is a major cost component of most construction operations, and you have more control over the cost than you think. The problem is that most contractors do nothing to track equipment utilization.
Equipment costs money every minute of every day; 24/7. Whether you are using it or it is sitting in the yard, you are running up a cost-to-own balance daily. In fact, if you own it, the unit is probably over 60 months old with high maintenance bills also taking a toll. Add in operating costs that accumulate every time you turn it on and pretty soon we are talking real money.
At the end of the year, you could have accumulated ownership and operating costs in excess of the rental cost to complete the same tasks. Throw in logistics costs you avoid when you rent, and pretty soon you start figuring out it may be a good idea to track utilization.
How much do you have to use a unit to justify owning it? We are talking annual utilization here and not weekly or monthly. I would say you need at least 60% utilization; that also assumes you charge off the unit cost and collect for it in the process.
Equipment utilization figures need to be collected for each year (by hours used), ownership and operating costs compiled and both a cost and billing rate established for each unit. (Hey, it sounds like you are a rental company!) The trick is to charge off more than the total cost and produce a return on the cost of the equipment.
Having better control over equipment costs could help you avoid laying off personnel and at the same time improve profit margins.
It's time to track those hours!