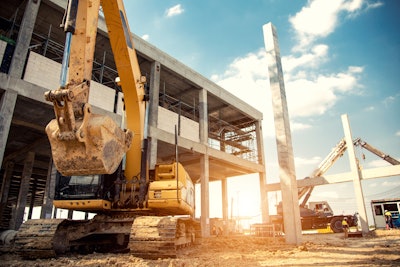
One of the biggest challenges the construction industry is facing today is rising fuel costs. Due to the industry's reliance on heavy equipment such as trucks, cranes, and yellow iron, 98% of all energy use across the industry comes from diesel. With diesel prices increasing by as much as 55% per gallon, the industry's high rate of fuel consumption has become even more costly over the past few years.
Adding to the pressure is increased regulatory and investor scrutiny on CO2 emissions. Concrete production is one of the world’s largest emitters of CO2, accounting for about three times as much CO2 pollution as aviation, a figure that is especially concerning given that the world’s building stock is expected to double by 2060.
As a result, stringent government regulations and hefty fines (including those for heavy equipment) are being introduced to minimize the industry's overall carbon footprint. With fuel costs on the rise and emissions reductions targets looming, construction companies are looking for ways to reduce fuel usage without compromising productivity. But without real-time visibility into fuel consumption, construction companies have no way of tracking or acting upon their fuel expenditure or emissions.
That's where real-time Internet of Things (IoT) data comes in — and it is playing a bigger role than ever before, pushing the construction industry into the modern digital age. Through the adoption of IoT sensors that provide real-time insights on fuel use, construction companies are taking control of their data to save costs, reduce emissions, and improve operational efficiency. In fact, according to a recent analysis of some of Samsara's construction customers, organizations saw a 28% reduction in idling within their first year using the platform.*
The best way to illustrate this is through the lens of an industry leader like Summit Materials. By leveraging real-time sensor data, Summit Materials is able to stay resilient in the face of today’s challenges and position themselves to meet their ambitious sustainability goals in the future.
How Summit Materials is Saving $1.8M on Fuel Costs
Summit Materials is a provider of integrated construction materials, with more than 400 sites across 23 U.S. states and British Columbia, Canada. With such a large operation, fuel represents one of their largest costs.
“We consume about 35 million gallons of diesel annually,” said Karli Anderson, executive vice president, chief people and ESG officer, and head of communications at Summit Materials. “With the increase in fuel costs, we have every incentive as a business to reduce our fuel use because of the benefits in terms of both cost and emissions reduction.”
Idling, which occurs when a vehicle’s engine is left running when it’s not in motion, is one of the biggest contributors of fuel waste. Researchers estimate that idling from heavy-duty and light-duty vehicles in the U.S. alone wastes about 6 billion gallons of fuel annually, contributing to millions of tons of CO2 emissions and costing as much as $11 billion annually.
Like many companies, Summit Materials identified idling as one area they could optimize to reduce fuel use. But before adopting the right technology solutions, they could only track fuel usage based on fuel purchased, rather than actual fuel used. Now with IoT sensors real-time reports, Summit Materials is able to gain visibility into idling trends across their fleet, as well as granular data on idling. By connecting this real-time data with their existing systems, Summit Materials has unlocked a new, proactive approach to managing fuel consumption.
As a result, Summit is saving approximately $1.8 million per year on fuel costs, a significant bottom-line benefit that reflects the savings that many companies across the construction industry are realizing through the right technology investments.
Achieving ESG Goals with Real-time Data
It’s not just about cost savings, real-time data is also helping construction companies keep up with increasing stakeholder expectations around sustainability, particularly for environmental, social, and governance (ESG) reporting. In response to the massive volume of emissions generated by the construction industry, new standards for off-highway equipment are mandating lower emissions levels or replacing legacy equipment altogether, and failure to follow these standards has led to companies having to pay as much as $819,000 in fines.
In addition, construction companies looking to lower their net emissions can also leverage carbon offsets (also known as carbon credits), which are tradable certificates associated with activities that lower carbon emissions.
By participating in the offset market, construction companies can shrink their net carbon footprint by funding projects that reduce emissions elsewhere. Construction companies are now using real-time data to meet these new requirements and demonstrate their commitment to sustainability.
This information has become central to Summit Materials’ ESG initiative.
“From an investor perspective, what they want to see is consistent, incremental progress to use less resources, reduce costs, and reduce emissions over time,” said Anderson. “To be able to show, through data, how you're notching progress gives you a whole other level of credibility with the investment community and gives them significant confidence that you're not just throwing a number out there, but in fact, you are actually showing evidence of how you are reducing your impacts.”
Summit Materials’ Fuel Efficiency Program is just the beginning of their ESG goal of achieving net-zero emissions by 2050. By leveraging IoT data, as well as by taking advantage of the offset market, Summit Materials is on track to report on progress against their ESG goals.
“By attacking the carbon footprint of our vehicles, equipment, and material production, as well as with a little help from the credit and offset market, we’re able to show a clear path to a 75% reduction in emissions going through the entire value chain of the business,” said Anderson.
Real-time Data is Transforming the Construction Industry
Looking ahead, connected operations technology has the potential to be game-changing for the construction industry. For example, construction companies are increasingly looking to electric vehicles (EVs) to power their operations, helping reduce costs and lower emissions.
Research suggests that by 2030, owning an EV will be significantly cheaper than owning a gasoline or diesel vehicle (including for heavy-duty vehicles); alternative energy also means zero tailpipe emissions.
Electrification is a complex process that requires organizations to rightsize their fleet based on data such as vehicle type and class, lifetime usage, daily maximum range, and average fuel economy.
Real-time data is critical to these decisions. Summit Materials, for example, is already using data on their existing assets to inform their electrification journey and make smarter decisions about the future of their fleet.
As the industry continues to innovate, and new inventions emerge, such as concrete that traps CO2 from the air — construction companies will need to remain agile. Organizations that take advantage of IoT technology and the real-time data it provides are well-positioned to succeed in the future.
*Based on analysis of anonymized data across 329 customers, comparing average idling per customer during month 1 vs. month 12 post-implementation.