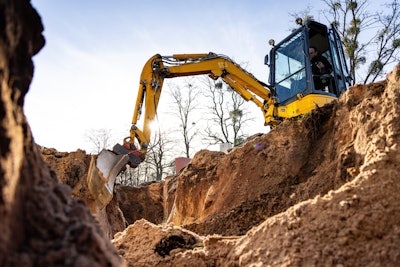
Construction sites often are a beehive of activity. When working around heavy equipment, one mistake or overlooked safety protocol can lead to an accident that injures your workers and derails your project.
There’s simply little room for error when operating heavy equipment. In fact, according to OSHA, as many as 75% of struck-by fatalities occur during heavy equipment use, such as trucks and cranes.
Common risks and losses include falling materials, operator blind spots, a tip-over or rollover, electrocution, and equipment not being locked out during maintenance or when an operator dismounts. When equipment safety isn’t championed prior to the start of a project and each day on the job site, the risk for injury, damage, and delays rises exponentially.
8 Best Practices for Heavy Equipment Use
Below are eight ways you can increase safety around heavy equipment on your job sites. Often overlooked is that the best time to begin your safety efforts is before a project gets underway.
Questions to ask your team in advance include where are we getting the equipment—do we have it or are we renting it? Are there any maintenance or performance issues? How will it be used on a particular job? Who’s best qualified to operate it?
Eight ways to increase safety around heavy equipment:
1. Inspect equipment first
Before operating a piece of equipment, confirm it’s in good condition. Walk around the machine and look for obvious signs of wear-and-tear or oil and hydraulic leaks. Inspect machinery at the end of the day, too. When run over an extended period, equipment can overheat and catch fire. Part of maintaining equipment is knowing when to shut it down before it reaches its limit. Of course, machines naturally break down over time, so it’s essential to budget for equipment replacements.
2. Know your equipment limitations
For example, forklifts are often pushed beyond their weight limits. To avoid accidents, workers should measure the weight of materials to be moved against the equipment available. Consider multiple trips with the same forklift or bring in bigger equipment to meet the load demand. When a project scope changes, so too can equipment needs. Be sure to bring in the right equipment to safely do the work.
3. Integrate nuanced training programs
Have a safety professional audit and update your safety plan before a new project begins—revisit the plan during a project to ensure it reflects any changing job site conditions. Given the scope shifts from project to project, determine how and when training will be conducted, what type of training is needed for each project or job site, as well as which staff members can effectively lead training sessions. Ensure operators have been properly trained on equipment—new, or rental equipment, may have features an old-school operator’s not accustomed to using. Have safety conversations daily on the job.
4. Always have a spotter
Equipment spotters identify hazards, exposures, and risks that the operator—whose vision in a machine may be limited—may not notice. While often overlooked due to cost, hiring a spotter is far less taxing than an accident that could injure your workers, delay your project, and potentially damage your company’s reputation.
5. Communicate with the operator
Accidents often occur when the operator is moving too quickly—a sign you may not have the right person operating the equipment—or has significant blind spots. If a spotter notices the operator is neglecting key safety principles or showing signs of fatigue while using equipment, it’s their job to communicate with the operator, and in extreme cases, cease operations immediately. All it takes is one incident for serious injuries and damage to occur.
6. Eliminate electrocution risks on site
Electrocution becomes a significant risk in high voltage areas. For example, if an excavator arm reaches too far into an area adjacent to a power source, it could lead to injury or death for the operator as well as those nearby. A spotter can help determine if equipment is getting too close to power lines.
7. Factor in the weather
Extreme cold or heat can take its toll on an equipment operator, who often sits for long periods of time with little movement. Before work begins, contractors should identify any environmental factors that could negatively impact their workers and take steps to mitigate them.
8. Slow down
Yes, time is money, and every project has a deadline. All the more reason to take time to ensure your team has the proper safety protocols in place, practices them daily, and holds one another accountable. Safety boils down to common sense. Nearly all accidents we see occur from rushing. Help keep your projects on track—and profitable—by avoiding accidents.
Equipment spotters identify hazards, exposures, and risks that the operator—whose vision in a machine may be limited—may not notice.@dusanpetkovic1 - adobe.stock.com
Make Safety Everyone’s Responsibility
While you and your leadership team lead the way in minimizing risk on your job sites, safety is everyone’s responsibility. Cultivate this mindset through a positive work environment where you encourage your workers to take the necessary steps to protect themselves and their peers.
While looming deadlines and tight budgets often take precedent when a project is in flight, building a culture of safety day in and day out and taking the time to hold everyone accountable for safety ensures a better outcome for your workers, projects, and bottom line.
Ensure Your Policies and Limits are Up to Date
Even with a robust culture of safety, accidents do happen. Insurance policies can cover physical damage caused by machinery on and off the road and general liabilities, including litigation. Talk with your insurer or agent to ensure your policy limits are sufficient to help cover your risks, as replacement and repair costs today may be much higher than just a few years ago. Your insurer or local expert may also offer safety services to help manage your risk.