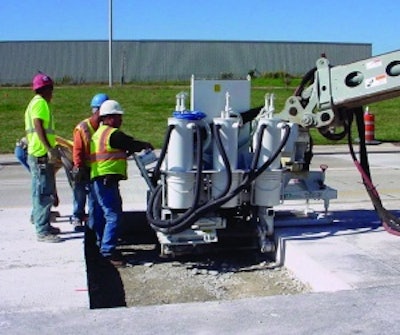
Concrete dowel pin drills are a great way to enhance productivity on jobsites -- but, as with any piece of equipment, they come with their fair share of safety requirements and must be operated with safety in mind at all times. By knowing the available options and other jobsite factors to consider, operators can spend less time worrying about safety and more time focused on the job at hand.
Fortunately, as products have evolved and developed, the safety of both workers and bystanders has been enhanced. Today's concrete dowel pin drills are typically offered as chassis-mounted units with wheels for easy mobility, and in equipment-mounted configurations for pairing with common jobsite carriers, such as skid steers. Single-gang units can be adjusted to quickly drill precise, clean holes, while multi-gang and equipment-mounted models allow multiple holes to be drilled with the same quality, speed and accuracy.
Workers can operate the drills in a comfortable, upright position, thanks to the mounting configuration and conveniently located control panels. They are also designed to absorb the majority of the drilling impact, eliminating many of the hand, arm and back injuries commonly associated with older, hand-held units.
Because today's dowel pin units work so much faster, operators spend less time drilling and see fewer fatigue-related injuries. Less time spent drilling also means less time on the jobsite -- workers are able to complete concrete patching projects faster and get crews off the busy roads.
Wireless Wonder
Both hydraulic and pneumatic drills offer similar productivity and safety advantages. However, each does come with a few safety concerns.
Hydraulic drills provide much smoother operation, but do tend to get warm during use and can overheat. As the drill heats up, so do the compressed fluids in the hydraulic line. If the line were to spring a leak or a hydraulic hose were to break, the operator could receive serious burns from the hot fluid.
To address this issue, some manufacturers offer remote operating devices. These wireless control systems allow workers to remain a safe distance away from the machine during operation. In the event of a hose leak or break, the operator would be able to shut down the hot machine without getting close to it.
Because they utilize more air, pneumatic drills tend to hit with more force than hydraulic models. As a result, they can drill faster, further increasing productivity. However, the increased vibration these drills produce can injure operators and lead to possible hazards from flying debris. Again, the use of the wireless remote has resolved both issues.
Remote operating systems offer other advantages for both hydraulic and pneumatic units. In the case of equipment-mounted models, wireless remotes allow the operator to control the drill from inside the cab. This takes the operator off the road and out of the way of traffic, plus prevents him or her from being struck by the drill as it rotates on the end of a boom. It also reduces required labor, since only one additional worker is needed to occasionally guide the drill in place.
Wireless remote systems provide workers with a safer option to operate on-grade and on-slab units, as well. Rather than standing next to the machine to control it, the operator can stand down in the grade. Again, this positioning removes the operator from live traffic lanes, while also keeping him or her away from heat and noise given off by the compressor.
Clearing the Air
There are other potential hazards that go along with concrete drilling operations. One of the biggest is dust emissions.
Whether it's being ground, sawed or drilled, concrete emits a significant amount of dust containing crystalline silica, which has been shown to cause serious and even fatal side effects when exposed to large amounts. In some industries, OSHA has placed limitations on how much exposure a worker can be subjected to in an eight-hour workday.
Concrete dust can also be detrimental to traffic flow. It can travel across a worksite, into adjacent traffic lanes, and make it difficult for drivers to see the road ahead -- including workers on the jobsite.
Fortunately, dowel pin drill manufacturers have introduced dust collection systems to help reduce the amount of emissions. Though all are targeted at the same function, the approach has been different. From a contractor perspective, it's important to consider the proven effectiveness of such dust collection systems.
The National Institute for Occupational Safety (NIOSH) has tested some systems and can offer direct information on the test results. In testing of one system, NIOSH found it reduced concrete dust emissions by up to 89 percent. This level of dust reduction results in not only a safer working environment on the jobsite, but also a safer environment for traffic.
Additional Considerations
Other factors associated with drilling operations, such as noise, flying debris and heat, should also be recognized and addressed.
All workers on the jobsite, including operators, flaggers and others, should wear the proper hearing, eye and dust protection equipment as per local requirements, which vary with each project and location. Typical requirements will likely include earplugs or earmuffs, safety goggles, and masks or respirators for further protection from dust emissions.
It's also important to follow safety guidelines when cleaning the unit and performing routine maintenance. Prior to cleaning at the end of the day, first disconnect the unit from the air compressor and any power connection, then bleed off air that may be stored in the unit. Take a few minutes to allow the unit time to thoroughly cool down -- especially when working with hydraulic drills -- before proceeding with routine cleaning and maintenance tasks.