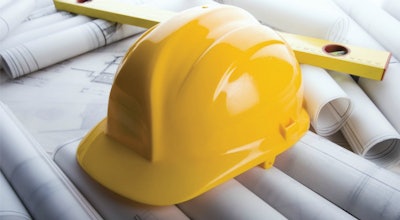
Like other investments in your company, jobsite safety will pay off in the long run by reducing accidents and workers compensation claims and improving your bottom line.
John had been sent ahead of the crew to “clean and prep” a lot at a local fast-food restaurant that would be receiving a new concrete drive-thru lane. Arriving with two other employees, the three-man crew immediately began to jack hammer out the current asphalt drive-thru area so they could prepare for the formwork.
Before John cut what he thought might be his last bit of asphalt to dig out, a car turned right into the shallow hole he created. With his back to the lot’s entry, John never saw the car until it was almost too late. Fortunately nothing more happened to John than a quick increase in his heart rate. While the driver apologized for almost hitting John, he also asked why there were no safety signs or barrels. John sheepishly answered, “Uh, I dunno!”
This scenario is too easy to learn from, yet that is exactly why I feel it is critical to address. Though most of us, as contractors, realize the importance of safety, we often push it down on our lists of things to teach our workers. Worker safety, and the safety of any passersby, is critical to our success.
At the risk of “preaching to the choir” let me offer tips that will help you work toward raising the level of safety within your business.
- Quit talking about it and train, train, train!
- Make safety a discussion at each weekly meeting. Discuss ideas to make the work and work site safer.
- Invest in safety flares, barricades, tape, flags, etc. Keep a healthy supply of disposable items (i.e. tape, flares) and rent barricades, signal boards, etc.
- Make safety items standard equipment in proposals, site plans and inventory. Safety thinking begins when you make it part of the way you do business.
- Provide instruction on safety products that stresses proper handling and maintenance. Workers who are correctly instructed the first time tend to repeat correct behavior.
- Hold employees accountable for safety defects. Defects can include unsafe work practices and neglecting to use required safety products on a job.
- Appoint a safety coordinator or specialist for each crew. Give one employee the added responsibility to monitor and lead others in safety-related issues. Give these safety people additional training in safety products and procedures.
- Inform customers of safety products that will be used on a job and remind them to honor such items. Customers are the biggest violators of moving barrels, tape, etc. Clarify your emphasis on maintaining safety for your crew and your customer’s employees.
- Replace damaged safety products. Prevent safety tape from being tied off on empty buckets, broken-off broom handles or paint cans. If your barricade is wobbly, spend the bucks to invest in a new one.
- Reward crews for completing jobs “incident free.” Crews repeat good jobsite practices when they are rewarded for them.
- Discipline non-compliant safety habits and terminate when needed. Workers “get it” when you are serious about safety.
- Make safety a personal improvement issue for yourself. Model positive and proactive safety behavior for your own crews to observe. They will practice what you preach if you practice what you preach.
Work hard at establishing safety as a “non-negotiable” for your company. If you do, you will begin to experience all kinds of new benefits like safer work areas, happier customers, more confident employees, a more positive insurance rating, less costs and more profits.
Brad Humphrey is president of Pinnacle Development Group, a consulting firm specializing in assisting contractors in the United States and Canada. Join Brad’s weekly column by signing up at www.thecontractorsbestfriend.com.